第4章 マクロレーザープロセシング(レーザーマクロ加工)
3. レーザー切断
1. 概要
1.1 はじめに
レーザー切断は日本の産業界において最も普及されているレーザー応用技術である。歴史は長く改良を積んだ結果、従来の板金加工の板厚範囲は言うに及ばず、軟鋼で25mm以上の厚板切断も可能となってきた。また、薄板では精密で微細な加工もできるようになり、加工精度も大幅に改善されて従来の機械加工に十分対抗できるようになってきた。これは特にパルス発振技術の改善と、高い周波数による擬似連続波(CW-like)の発振形態を可能にした発振器技術に負うところが大きい。最近のレーザー切断では、特に発振器の高出力化と切断加工原理の理解の深まりから、軟鋼やステンレスで板厚30mmを超える極厚板の切断加工もできるようになってきた。そのため適用範囲も広がり産業応用の展開が大きく変わってきた。また、光伝搬特性や光路長からくる集光特性など変化が加工の過程で考慮されるようになったことによって、現在では極薄板の精密微細な切断から極厚板の大板の切断までレーザーで実現できるようになってきた。
目次へ ∧
1.2 切断加工の原理
レーザー切断とは、レーザー吸収による熱作用及び噴射ガスのアシストガスによって材料を強制的に分離する加工法をいう。金属の場合を例にとれば、レンズまたはミラー等の集光光学系によって集光されたレーザー光が材料表面に照射されると、材料のごく表層部(例えば、金属によっては数〜数10nm)で波長吸収され分子振動を誘起することから急激に発熱し昇温する。その結果、表面の照射地点には瞬時に溶融池または蒸発穴が形成される。この状態でアシストガスを噴射しながらレーザービームまたは材料が相対的に移動すると、照射方向(深さ方向)に活性化ガスによって誘起される酸化反応と噴射ガスの運動エネルギーによって溶融金属が強制除去され、除去された部分に連続的な切断溝(カーフ)が形成される。レーザー切断はこのような現象を利用した加工法である。図1にレーザー切断機構を基にした金属材料の切断モデルを示す。
レーザー切断で最も重要なのは切断フロントの状態である。切断フロントにおける温度と溶融膜厚が切断を左右するため、この関係を考察する必要がある。切断フロントでの相対温度は、切断速度が速くなるにつれて切断フロントの相対的な位置が熱源の中心軸に近づくことから極めて高くなる。また、アシストガス噴流の一定ガス圧の下では、切断速度が遅いとレーザー光の真下における切断溝が大きくなり溝内で溶融金属は多く発生するものの、その分ガス噴流のフロントに滞留する時間が長くなることからガス運動量の影響をもろに受けて、直下の溶融金属膜は大量に強制除去されてかえって薄くなる。反対に、切断速度が速いほどレーザー照射の位置とガス噴流の衝突個所が次々と移動することから一点における滞留時間が短くなる。その結果、フロントでの切断幅が小さくなり溶融金属の除去量がむしろ減少し、高熱が作用する熱反応フロントにおける溶融膜厚は大きくなる。このことから、溶融膜厚は切断速度が高速になるほど厚くなる。図2にその結果を図示する。このようにレーザ一切断をつかさどり、切断を維持するのは切断フロントに生じる温度と一定の溶融膜厚であり、これが切断時の加工速度を決定している1)。
金属切断では切断フロント(切断前面)近傍の切断面で、集光スポットの高密度熱源による鉄の燃焼速度(又は、溶融反応速度)は極めて速く、酸素の分子の拡散速度(酸化反応速度)はそれより遅いとされている2)。また、高速度カメラで観察した荒田らの報告によれば、lm/min前後の比較的遅い速度ではビーム移動に伴う溶融速度と酸化速度は断続的になり、周期的な条痕ピッチを形成しているとしている3)。また、それ以上の切断速度で連続的になるとしている。しかし、この速度範囲を超えた薄板・中厚板の切断速度でも、或いは速度のより速い場合でも一定の規則性をもった条痕が生成されることや、厳密には間隔が必ずしも一定ではないなどのことから、現在のところまだ全てが明らかにはなっているとは言い難いと思われる。
ともあれ、溶融速度と酸化速度の時間差や溶融・凝固と再燃焼のヒートサイクルの周期的挙動と、レーザービームの移動に伴うポインティングスタビリティーとそれに乗じる出力変動(パワーリップル)の微変動(脈動)等によって、レーザー切断面の上面に面あらさに相応した条痕が形成されることは考えられる。これらの間隔は板厚が厚く切断速度が遅いほど大きく、板厚が薄く速度が速いほど間隔は小さくなる傾向を示す。なお、その下面はドラグラインと呼ばれ、上部からのアシストガスのガス噴流によって下方に押し流されて形成されるラインで、ほぼ上部の条痕を引きずったように現われ、さらに下方では溶融金属の流れが遅れてくることからドラグラインの遅れが発生する。同じ板厚では、切断速度が速いほどこの遅れは大となり後方に大きく曲がる。典型的な切断面の断面写真を図3に示す。
目次へ ∧
1.3 切断の加工の特徴
レーザービームは工具として優れた性能を有している。その主な特徴を切断加工の立場から列挙するとつぎの通りである。
① 赤外線レーザーによる切断は、基本的に比較的長波長の波長吸収による発熱のメカニズムを利用した熱加工である。このため、表面における波長吸収と熱の発現は被加工材によって異なる。また、レーザーは光であり空間を減衰することなく伝搬できるので非接触切断が可能で、材料に対する直接の力学的な負荷や汚染はない。
② レーザービームは極めて小さなスポットに絞ることができ、材料に照射された集光ビームは焦点近傍で109から10W/cm2という極めて高いパワー密度を有する切断熱源になり得る。それゆえに集光ビーム中心部では瞬間に溶融除去または蒸発するが、レーザースポットから少し離れると溶融、及び酸化反応は促進しないため、切断される材料の切断幅及び熱影響層は極めて小さい。
③ 高反射材料に対する切断ではレーザー光が材料に殆ど吸収しないので、吸収性を高めるために特殊な表面処理や尖頭値の高いパルスピークを用いない限り一般には困難であるが、切断される材料の脆さ、硬さ、剛性などに拠らず切断が可能で、NCプログラムソフトとの連動によって、型を用いることなく高速で形状を切り出すことができる。
④ 材料表面に発生する熱は極めて狭い範囲で高温になり、一般の鉄系材料では材料の溶融温度まで瞬時に昇温する。また、低融点材料においては瞬時に蒸発温度にまで昇温する。従って、加工される材料の熱特性は、材料固有の熱的な物性値によって決まる。
⑤ レーザーによる切断加工は一般に高速切断が可能で、一点に関与する時間が短いために材料に対する熱的な伝達は小さい。そのため、加工された材料の熱歪、熱影響層は他の熱加工法に比較して小さい。また、光であることから一般の機械加工のような工具の磨耗、振動、騒音などはない。
などの特徴を有している。
目次へ ∧
1.4 切断加工の種類
レーザー切断はその切断のメカニズムから、①溶融切断、②蒸発切断、③割断(かつだん)に大別することができる。このうち溶融切断はレーザー照射によって溶融現象を伴うもので、積極的な溶融切断と消極的な溶融切断とがあり、前者はアシストガスに活性ガスの酸素ガスを用いる反応切断(酸化切断)であり、後者は不活性ガスのアルゴン(Ar)ガスまたは窒素(N2)ガスを用いる非反応切断(無酸化切断)である。また、アシストガスに窒素と酸素の割合が3:1である空気を用いて行なう中間的反応切断もある。それぞれ切断面の光沢が異なり酸素の多いものほど光沢は少ない。
蒸発切断は特に融点が低い材料や非金属に多い。赤外線のレーザー波長を吸収して発熱し、瞬時に熱分解及び劣化を伴う蒸発現象によって切断されるものである。この場合のアシストガスには通常、燃焼を防止し蒸発ガスを除去する目的で不活性ガスや空気を用いる。割断はガラスなどの熱伝導性の悪く脆い材料、例えば、ガラスなどにおいてレーザー照射したとき圧縮・引張応力によって生じるクラックを積極的に加工に利用したものである。これら分類の関係を図4に示す。
目次へ ∧
1.5 切断の加工パラメータ
(1)レーザー切断加工因子
レーザー加工は、レーザー出力やパワー密度に代表されるレーザーエネルギーと、レーザーの照射時間や材料の送り時間に代表される関与時間と、材料の光に対する熱定数、波長吸吸収性、材料成分からくる熱的な反応速度によって支配される。このうち、切断はレーザーの応用加工の中で最も加工システム全体に直接的に影響される。すなわち、発振ビームの安定性や加工機の剛性、或いは伝送、集光などの特性や、加工ノウハウなどによって加工品質は大きく左右され、レーザーの持つ切断ツールとしての性能を発揮させるためにはバランスされたトータルな技術が重要である。
図5にはレーザー切断における品質に影響を及ぼす諸因子を示す。レーザー切断品質に影響を及ぼす加工因子(パラメータ)は非常に多い。最近、板厚に対する焦点位置の関係や、光の適正な入射角と径(Fナンバー)または焦点深度(レイリー長)など光技術的な側面から技術的改良が加えられてきた。
目次へ ∧
レーザー切断は、殆ど光と同軸でアシストガスを同時に噴射する。切断はアシストガスの種類と条件(圧力、流量)に大きく依存する。このアシストガスには以下に示すような役割がある。
i. レーザー照射で生じた溶融物や蒸発ガスを速やかに除去し、切断溝を形成するとともに流れ出た下面の溶融付着物を取り除く。
ii. 酸素ガスをアシストガスに用いた溶融切断である酸化反応切断では、酸化反応によって生起される酸化反応熱とレーザーエネルギーの相乗作用によって、切断の速度と切断品質の向上をもたらす。反面、不活性ガスを用いた場合には切断可能な板厚や速度は抑えられるが、切断面の酸化は防止または抑制される。
iii. 形成する切断溝の周りを冷却し、熱影響部を抑える効果があり、同時に切断によって生じる溶融物や飛散物から加エレンズ(集光光学系)を保護する役割がある。
目次へ ∧
切断用に普及している産業用の炭酸ガスレーザーは4kWまでであるが、特に近年では厚板指向が一般化し高速化を追及する過程で、高出力化は進んで出力6kWクラスでも切断に用いられるようになってきた。図6には軟鋼の場合を例に、レーザー出力と切断加工板厚の関係を示した。
上の曲線は比較的小規模な加工機、若しくは実験室的に切断可能な値で、下の曲線は大型加工機やビーム伝送距離の大きい場合の安定加工領域である。レーザー出力と切断能力の関係は、上図に示すように、直線的ではないが比例関係にある。また、その性能は現場環境や加工システムの大きさではその切断性能は異なる。この主な原因は、ビーム伝送による光剛性や径の拡尢及び折返しミラー等の中継点による光の減衰等の影響で、結果的にビームの集光特性が異なることに起因する。
目次へ ∧
切断において最も重要な因子の一つにレーザービームの品質、すなわちビームモードがある。基本モードであるガウスモードは集光性に優れ、最も小さく絞ることができることから、特に切断に適している。レーザー切断におけるガウスモードの場合の利点として挙げると以下のようになる4)。
i. 出力と速度平面における良切断領域が拡大する。
ii. 一定板厚を切断できる速度の選択範囲が広い。
iii. 面粗さが良好である(特に、薄板では顕著)。
iv. 切断幅が小さく、テーパが少ない。
一般に、発振能力が大出力になるにつれてビームモードは低下する。
目次へ ∧
光は進行方向と直角に電界ベクトルが振動しており、この電界ベクトルの方向によって偏光が生ずる。電界べクトルの方向が一方向だけの場合を直線偏光と呼ぶ。直線偏光の場合、平行に切断できるはずの切断溝は、偏光の方向との関係で偏りを生じる。一般に、平面上構成された共振器からでるビームは直線偏光のビームであるが、発振器より取り出されたビームはリラーダを介してx、y方向で位相差を利用して方向が時間とともに同じ半径で均しく回転する円偏光に変換して切断に利用している。また、図7には、代表的な偏光方向による切断面の状態を示す。ただし、実際のレーザー切断装置は発振器の筐体内に円偏光ユニットなどを設置して、円偏光度は80%以上になるように設計されている。これにより、切断には実用的に差し支えないとされている。
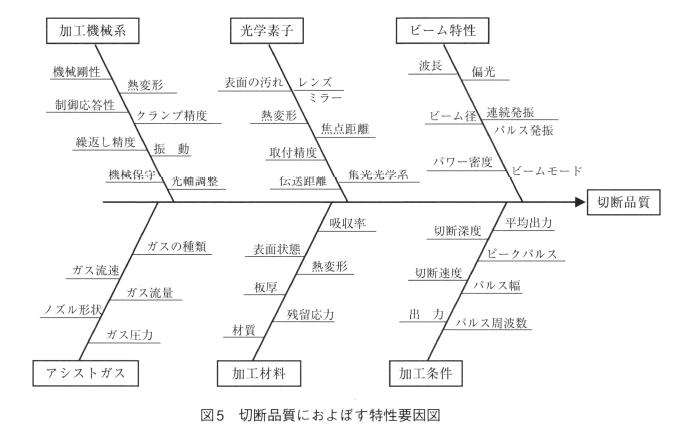
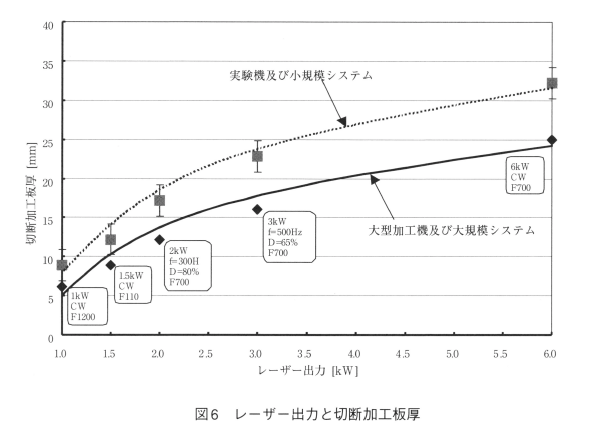
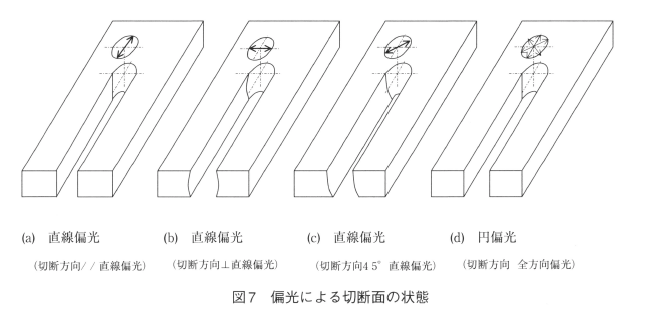
目次へ ∧
2. 切断加工の実際
2.1 金属材料の切断
金属材料のレーザー切断は板金関連業界で早くから普及した加工法である。材種は殆ど全種が対象で、切断可能な板厚も年々その範囲を伸ばしてきた。現在、厚板仕様のレーザーは出力6kWクラスまでが切断に用いられており、軟鋼で板厚は1インチ以上の切断が可能である。一般にレーザー切断は安定したドロスフリー切断が条件であり、ピンポイント条件で可能な切断は含めない。
レーザー切断の加工パラメータには、主に出力、板厚、切断速度(加エテーブルの送り速度)等がある。代表的な軟鋼材を用いた場合の切断速度と切断深さの関係を図8に示す。使用レンズの焦点距離は127mmで、出力は3kWまで0.5kWずつ変化させ、切断速度はまでを図示した。切断速度が遅いほど、またレーザー出力が大きいほど、切断深さは大きくなる。
また、切断速度と切断板厚の関係を図9に示した。切断板厚の限界は切断出力によって決まり、lkWでは12mmまで、また2kWでは19mmまで、さらに3kWでは25mmまでが切断可能である。ただし、この値は機械の一般サイズ(材料的に約1.5m〜3.0mの範囲)での保証値であってシステムが大きくなるとそれだけ光路長が増すので、この保証値も変化する。
目次へ ∧
レーザーの発振形態には連続波とパルス波があるが、CW切断は被加工物の形状が大きい場合や高速切断の場合に多く用いられる。特に薄板でのCW切断面のドラグラインや条痕は緻密且つ滑らかで面あらさは比較的小さい。これに対して、パルス波切断は低入熱で、精度を要する精密加工に適している。特に、微細加工や高精度加工、または、厚板の小穴加工、コーナ部加工、シャープエッジ加工、切断開始に用いるピアシング加工などに用いられる。切断加工の例を図10に示す。アシストガスに窒素等を用いて無酸素雰囲気の中での薄板切断では、いわゆる「光切断」が実現する。この場合、酸素切断より速度は高速化する。また、高反射材料に対する切断では、吸収性を高めるための特殊な表面前処理や、尖頭値の高いパルスピークを用いる。レーザー切断では、切断される材料の脆さ、硬さ、剛性などに拠らず切断が可能である。
目次へ ∧
厚い板材においては、酸化反応を主体とした切断現象が支配的になる。厚板切断では焦点深度の大きい長焦点レンズが用いられる。その結果、切断速度は比較的遅く、切断幅(カーフ幅)の広い切断が行われる。逆に、この幅がアシストガスの流れを下面にまで誘導する効果をもたらすが、酸化燃焼に伴う溶融金属を切断溝から除去することによって生じるスラグも多量に発生する。切断条件の範囲を超えると、ドロスが発生して切断溝裏面に付着するようになる。レーザー切断においては、板厚に応じた最適速度範囲が存在する。また、厚板切断では自然条痕を伴ったレーザー特有の面性状を呈する。鉄系の切断では純度の高い酸素の供給が重要で、噴射ガスの運動エネルギーが充分に切断溝の下面まで届かなくなったところで、切断限界になる5)。図11には、12mmの軟鋼の中・厚板切断の事例を示す。
目次へ ∧
厚板の例を示す。図12には、ステンレス(SUS304)で、板厚が20mmの無酸化切断の例を示す。使用レーザーはCO2レーザーの6kWで、光路長し=7.5m、ノズルφ=8mmのところで切断をおこなった。周波数は2kHz、CW-like切断で、そのときのガスは窒素で圧力は1.8MPaであった。送り速度はF=400mm/min、使用レンズの焦点距離はEFL:254mm(10インチ)である6)。
また図13には、軟鋼(SS400)で、板厚が32mmの酸化反応切断の例を示す。使用レーザーは、同じくCO2レーザーの6kWで、ノズルφ=6mmで光路長L=8.0mのところで切断をおこなった。周波数は1kHz、デューティー比は70%の切断で、酸素ガスの圧力は0.2MPa、あった。送り速度はF=475mm/min、使用レンズの焦点距離(EFL)はEFL:254mm(10インチ)である7)。
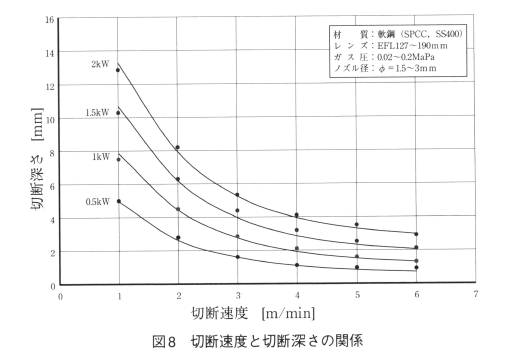
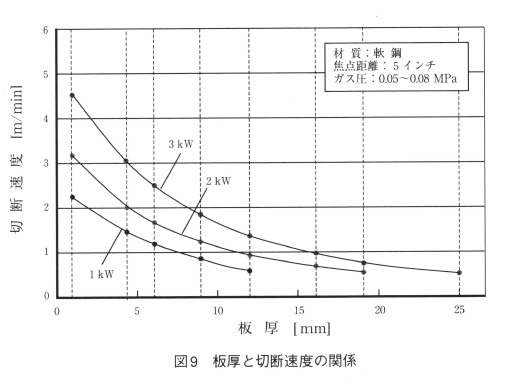
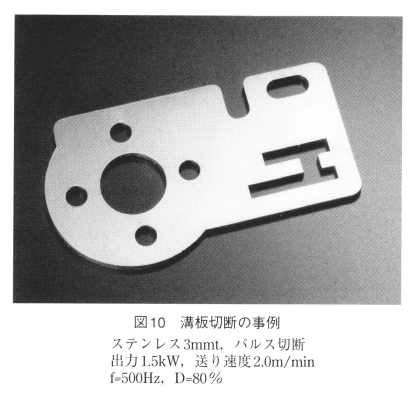
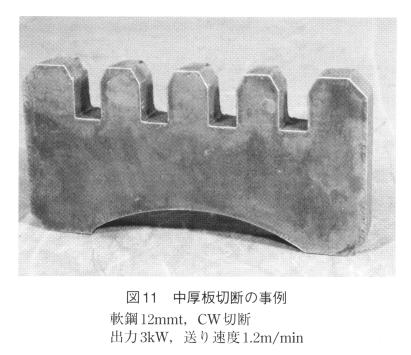
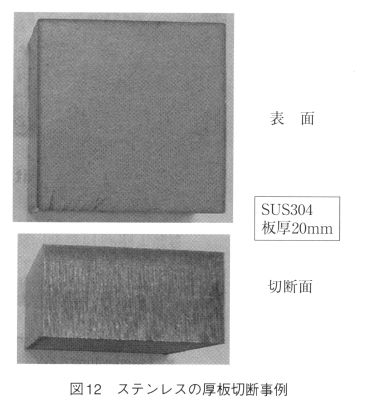
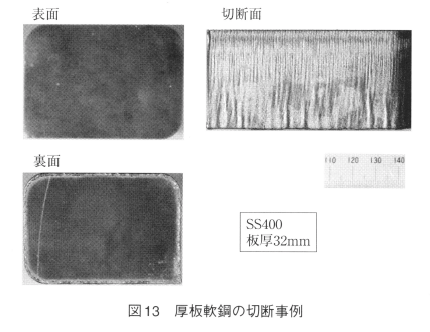
目次へ ∧
2.2 その他の特殊切断加工法15)
レーザーの切断に伴う現象や加工性が明らかになるにつれて、原理的な面から検討された結果、出力2〜3kWクラスのレーザー発振器を用いて、従来法による切断可能な範囲を大幅に越えた新加工法式が開発されたその例を紹介する。
目次へ ∧
BS切断はレーザー光と特殊ノズル及び高圧アシストガスの組合せからなる切断法で、レーザー照射により発火点に達した材料表面を、アシストガスの高圧酸素噴流によって燃焼させ、材料の自己燃焼を伴う酸化反応によって生起される溶融拡散速度と、高圧ガス用に設計された特殊ノズルからの酸素ガスジェットの流速がバランスしたところで切断溝が形成される一種のレーザー・ガス切断である。酸素ガス噴流とレーザービームが同軸で達成された例を図14に示す。その加工例では、出力2kWで板厚40mmの軟鋼がドロスフリーで切断している。
目次へ ∧
光学系を工夫して集光ビームに微小半径の回転を与えっつ切断する方法で、軟鋼の厚板やステンレスの厚板切断を可能にした方式で、これを回転ビーム切断法という。集光レンズの直後に角度aを有する傾斜ウィンド又は光学ウェッジ等を挿入すると、ビームがこの光学素子を通過する過程で屈折し、従来の光軸上の焦点からややシフ卜して集光する。この光学素子に回転を与えることで、微小のシフト量を半径とする回転ビームが形成される。回転ビームと材料移動によってビームはニブリング加工にように相対的に三日月状の間欠的な切断を行なう。この方法で、2kWクラスのレーザーで板厚30mmのステンレス鋼の切断とφ1〜2mmの穴径の穴あけ加工も可能である。図15に原理図とステンレスの加工結果を示す。アシストガスにはガス圧を0.1MPaの酸素を用い、回転数を毎分1500rpmとした時、板厚は25mmで切断速度は350mm/minであった。また、穴あけ加工は穴径がφ1〜3mmを得ている。
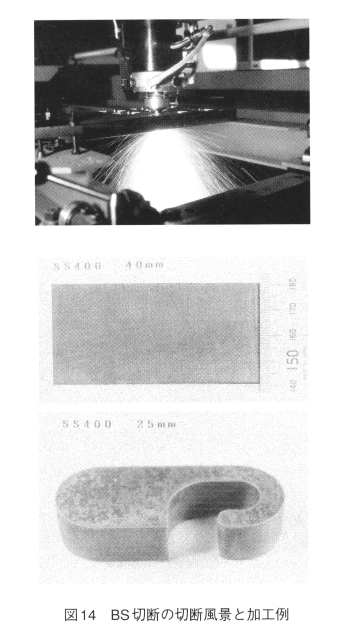
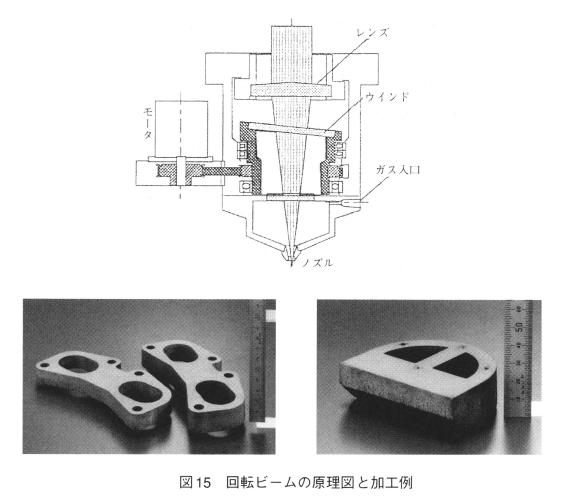
目次へ ∧
2.3 非鉄金属の切断
(1)木材の切断8)
木材の加工は切断が中心である。木材の場合は切断面が粧目面、板目面、木口となる場合があり、さらに繊維に平行と垂直に区分される。また、含水率が異なり、年輪に春材、秋材による密度の変化があることから木材の切断は複雑である。レーザー光が減衰する加工限界に近い部分で、この年輪界の影響が加工特性に影響する。材料の燃焼を防ぐために不活性ガスやエアーをアシストガスに用いて加工する。図16に比較的多孔質で均一材料のカツラ材の切断例を示す。切断幅は1mm未満であるが、薄板の広葉樹材では0.3mm前後のカーフ幅で切断が可能である。加工断面はやや黒ずんで炭化するが、最近の技術では、例えば、塩素系漂白剤などによって薬品処理を施すことでかなり制御できるようになってきた。
目次へ ∧
ファイバーボードやパーチクルボードなどの木質材料は木質のチップなどを圧縮して固めた木質系材料で、多くは建築材料として用いられている。しかし、繊維や木質チップを押し固めた製造上の性格から、天然材の自然の空隙率を有しない硬い材料である。ファイバーボードは木材などの植物繊維質の粉砕片や切削片などの小片に合成接着剤を塗布して人工的に成板した板である。また、ファイバーボードは繊維束を含めてパルプ状にした繊維を水若しくは空気などを媒体にしてシート状に成型し、これを乾燥熱圧締して製板したものである。このような製法から本質的には不均質で不連続であるため、熱の伝達は素材の細かさや密着度に左右される。したがって、小片の大きめの場合は切断幅や深さにムラができることがある。図17に木質材料のレーザー切断例を示す。出力は300Wで加工、500m/minである。材料は細かい不連続な木質繊維の圧縮材なので、パルス切断によって熱の関与時間を短くすることで熱影響層を小さくすることができる。
目次へ ∧
複合材料はプラスチック系、木質系などがある。いずれの複合材料も、材料中に熱的な性質や方向性が異なるものを含むため、熱加工を基本とするレーザー加工は一般に難しい。
図18には、木質系複合材料の例として11層からなる板厚18mmの合板を例に挙げる。アシストガスにエアーを用いて切断したもので、条件次第では綺麗に切断することができる。交互にサンドされた材質の熱的性質の極端に異なる場合には、各層間の溝幅に差が生じる。現在では高出力で高速に加工することでかなり解消できるとされている。
プラスチック系複合材料においては劣化や炭化が起こることに加え、カーボンファイバーなどを強化材に用いている場合には切断を得意とはしない。幾層にも交互に重ねる繊維と樹脂による繊維強化プラスチック(FRP)の場合は、異なる材料の積層においては熱の滞留や伝達が異なるため、ギザギザな面となるか、境界付近で両サイドに若干熱が広がるなどの影響がでることがある。したがって、精密な加工というよりは荒切断として用いる場合がある。多かれ少なかれ切断面の炭化は免れない。図19にレーザーによるガラス繊維強化プラスチック(GFRP)材料の切断面を示す。加工切断面を樹脂(エポキシ系)で固めて研磨によってスライスすることで得られるプレパラート(薄片)の写真を作成した。アシストガスはエアーを用いておこなったものであるが、加工はもっぱらパルス切断によるが、最適加工を行なえる条件の幅が狭く加工速度が増すと良好な切断幅は得られない。切断面には表面に炭化が見られる。
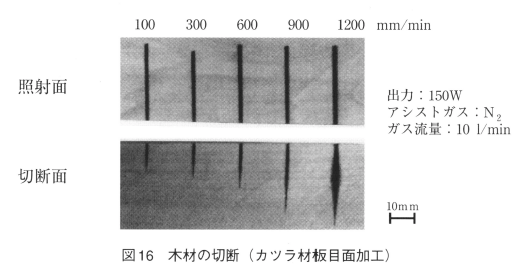
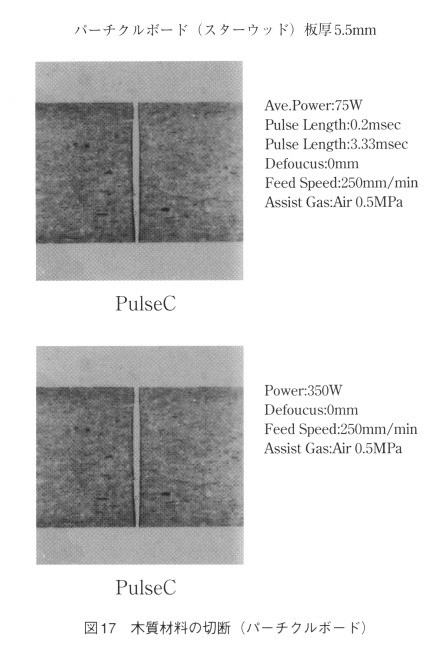
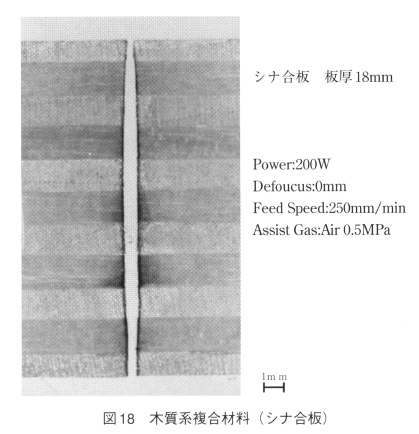
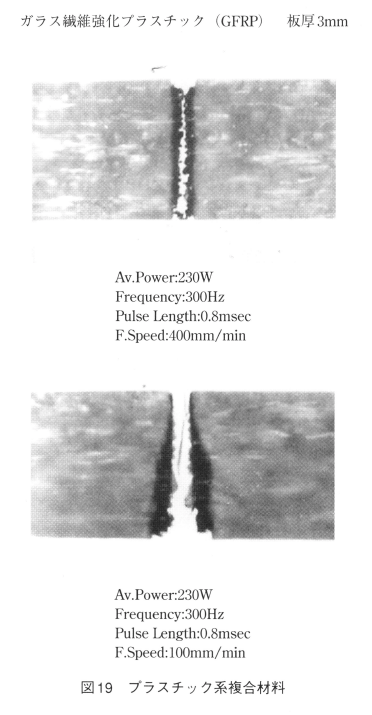
目次へ ∧
2.4 加工ノウハウ
加工を精度よく或いはきれいに切断を試みる過程で多くの加工ノウハウが誕生した。これが今日の切断技術を飛躍的に発展させた(表1)。特に、ステンレス切断における無酸化切断は、切断面も素材に近いか或いは金属光沢有する新しい切断法として普及している。また、レーザー光に対する反射率が極めて高く殆ど吸収しない高反射材料に対する切断加工は、一旦吸収すると反射率が低下することを利用して、初期のピーク値の高いパルス切断や、反射光防止装置との組合せによって加工を実現している。
目次へ ∧
[参考文献]
1) 新井、在間、井原:レーザーによる加工シミュレーション(第3報)2002年度精密工学会春季大会講演論文集 153 pp411 (2002.3)
2) 新井武二:レーザーによる加工シミュレーション(第5報)2003年度精密工学会春季大会講演論文集 179 pp403 (2003.3)
3) Y.Arata、et.al:Trans、of JWRI.8(1979)175
4) 新井武二著 :高出カレーザプロセス技術マシニスト出版(2004.6)
5) 新井、在間、井原 :レーザーによる加工シミュレーション(第4報)2005年度精密工学会秋季大会講演論文集 J82 pp444(2005.9)
6) 写真提供(ステンレス加工) :小池酸素工業(株)
7) 写真提供(厚板加工) :日酸TANAKA(株)
8) 新井武二、他 :CO2レーザーによる木材の加工 木材工業 Vol.31-8(1976.8)
9) 新井武二 :木材及び木質材料でのレーザー応用加工 木材工業 Vol.40-6(1985.8)
10) 例えば、精密工学会編:精密加工実用便覧 日刊工業社 (2000.4)
目次へ ∧