第4章 マクロレーザープロセシング(レーザーマクロ加工)
2. レーザー穴あけ
1. 概要
1.1 はじめに
レーザー除去加工のなかでも穴あけ加工の歴史は古い。1960年固体ルビーレーザーが発振してレーザー元年を迎えた訳であるが、その2年後の1962年には、ルビーレーザーによる最初の材料照射が行われ、その加工ターゲットがカミソリの刃への穴あけ加工であった。それから20年も経たない内に、Nd3+:ガラスレーザーなどによる産業用の穴あけ加工機が誕生し、古くは時計の軸受け(人造ルビー)の穴あけ加工に用いられた比較的効率がよく出力増大が容易であったCO2レーザーの高出力加工機が出現し穴あけ加工も本格化した。汎用機による紙巻タバコのフィルター部やスプレーノズルなどの穴あけ加工が行われた。また、Nd3+:YAGレーザーによるエンジン部品の穴あけなども応用例として有名であり、最近ではプリント基板の高密度実装技術などにも応用されている。昨今では時代の要請に応えて、YAG高調波による微細穴加工も発展の兆しを見せている。
目次へ ∧
1.2 レーザー穴あけ加工の特徴
レーザーによる穴あけ加工は穴加工の一種であるが、前者がレーザービームとアシストガスだけの作用によって穴をあけるのに対して、後者は穴の内部を加工するか、レーザー加工機の付加的機能によって空洞部(穴)を形成することによるもので用語の厳密な意味に相違がある。付加機能とはCNC制御テーブルによる微小域回転や、偏心又は回転機能を有するレンズなどの特殊光学系によるもので、回転半径を自由に選択し得るものである。また、CNC加エテーブルによる比較的大きな領域の穴加工(板厚に依るが、薄板軟鋼では約φ2mmより大きい穴)は輪郭・形状切断加工(円形状、穴加工)に属するために、穴あけ加工とは言わないのが普通である。したがって、本章で取り扱う加工は本来のビームによる穴あけ加工である。回転ビームによる穴あけ加工は別途扱う。
レーザーによる穴あけ加工は種々の材料に適応され、使用レーザーにはCO2レーザーは元より、微細穴あけ加工にはNd3+:YAGレーザー、Nd3+:YLFレーザー、Nd3+:YVO4レーザー等の固体レーザー、並びに紫外域のYAG高調波も広く用いられている。
ここで、レーザーによる穴あけ加工の特徴を述べる。
1) レーザー光を集光すると、そのスポット径は極めて小さくすることができる。一般の産業用レーザーにおいても、実際にCO2レーザーで約120/zm、Nd3+:YAGレーザーでも約40/zm前後にまで絞ることができる。さらに、非球面レンズを用いればCO2レーザーでも90μm以下にすることは可能である2)。従って、短時間にしかも極めて微細な穴あけ加工ができる。
2) 上記の理由から、レーザー穴あけ加工に対して106〜109W/cm2程度にまでパワー密度を上げることができ短い時間制御が可能なことから、従来穴あけ加工の困難であった難加工材のW、Ti、などの超硬合金、ダイヤモンドなどのモース硬度の高い宝石類、セラミックスなどへの加工も可能である。
3) レーザーは光であることから非接触加工が可能であり、機械加工で用いているドリルなどのような工具の磨耗がなく、また、工具の径によって決められていた最小加工穴径の限界は外されて、従来加工が困難であった数10μm径の穴あけが可能である。
4) レーザーによる穴あけ加工ではビームを斜めから入射して加工する斜め穴あけ加工が可能である。その角度は光が材料表面で全反射する臨界角に左右されるが、十分にこの臨界角以内であれば斜め穴あけ加工を実現することができる。また、光であるがゆえに光学系によって微小の回転穴加工も可能でフレキシビリティーを有する。
5) レーザー光とアシストガスの作用による穴あけ加工では、アスペクト比(穴径に対する穴深さの比)を10以上に取ることができるが、穴の深さには限界があり、板厚が厚くなると特殊な工夫を行なわない限り、穴の表と裏面では径が異なりテーパを有することになる。
穴あけ加工は、大板から部材や製品を切断して切り離す時においても、最初のスタート点を決めるためのピアス加工としても行なわれている。時間は長くなるものの軟鋼で板厚20mm台の厚板まで穴あけ加工が可能である。穴あけ加工は通常はパルス波による断続的加工である。薄、板の穴あけ加工には連続波(CW)を用いる場合があるが、これは殆ど板厚が9mm未満であって、極薄板や厚板の場合、或いは穴加工をきれいに施す場合にはパルス加工を行なうのが普通である(図1)。
ピアス加工は、従来ではパルス波を用いて少しずつ穴あけ加工を行なっていたが、高出力化に伴って現在では、ややデフォーカス状態の連続波でそのまま材料に照射して、一挙に溶融金属を吹き上げながら穴加工を行なう場合もある。表1には産業界で実際に行なわれている鉄系材料における発振形態と穴あけ加工の適用例を示す。また、図2には軟鋼(SPHC)6mmの板材にパルス発振と連続発振での穴あけ加工の例を示す。連続波による加工では表面穴径は10倍以上あるが、加工時間は半分以下である。しかし、短時間に穴があきさえすれば、スパッターや溶融物が穴の周りに付着しても構わないといった従来の考えから、現在では後処理を考えて、時間が掛かってもきれいに加工するといった考え方が主流になってきた。それに伴って穴あけ加工技術も変化して、パルスによる穴あけ加工で周波数やデューティー比を段階的に変化させて飛散金属を細かく、且つ少なく制御し、穴の周りに溶融金属を多量に付着すること無しに穴あけ加工ができるようになってきた。
目次へ ∧
1.3 穴あけ加工の原理
CO2レーザーやNd3+:YAGレーザーなどのような赤外線領域のレーザーによる加工は、材料表層での光吸収によって原子・分子が振動し、さらに共鳴振動によって熱伝導する。レーザー加工は材料がこの過程で急激に発熱することを用いた、いわゆる「熱加工」である。穴あけ加工はレーザー照射によって材料表面で溶融・蒸発を起こすことによってなされる。金属の場合、殆どは溶融状態に達したところにアシストガスの強力な噴射ガスが衝突して溶融金属が飛散・除去されるが、その後の新生面にレーザーが照射されて、再び酸化・溶融が起こる。この繰り返しで、ビーム強度の強い中心部から下方へと掘り進むプロセスをとる。これが一般的なレーザーによる穴あけ加工である。穴あけ加工には連続波とパルス波のレーザー光が用いられる。
低融点材料の穴あけ加工は、瞬時に溶融または燃焼し蒸発するか、非金属の場合には熱分解および熱劣化してアシストガスによって強制除去される。さらに、短パルス・超短パルスの穴あけ加工では、加工部近傍で光吸収が起こり蒸発気体によるプラズマ発生と急激な温度上昇による局部的な爆発と、これによる圧力波および溶融物、ガスの飛散などの物質作用によって穴が形成される。
目次へ ∧
比較的厚板の場合の穴あけ加工には、アシストガスを併用したパルス加工を行なうことが多い。軟鋼の場合、板厚としては9mm程度まではアシストガス噴流と共にレーザー光の発振周波数を固定して穴あけ加工を行なうが、板厚がそれ以上になると周波数を段階的に上げていく手法をとる。デューティー比(%)も同時に上げてゆく場合もある。いずれにしても、厚板に対してはパルス波レーザーによって時間を掛けて少しずつ溶融除去し、スパッターの飛散をより細かく抑えながら行なうのがー般的である。
アシストガスに酸素を用いる場合においては、アシストガス自体が酸化反応を誘起しつつ、溶融金属を切断溝から強制除去するための運動エネルギーにもなっている。しかし、集光したビームは焦点位置以降では徐々に広がってゆき、レーザー光は壁面での反射と吸収によって減衰してゆくことから、板厚方向に進むにつれて深く狭い穴から溶融金属を外部に効率よく排除することが困難となり、更にはレーザー光とアシストガスの効果的な到達が難しくなることで、穴加工の進行が止まる。穴加工の途中段階で内部に溶融物が残留する場合もある。したがって、集光ビームの結像点以降は深さ方向に進むにつれて光が広がり、パワー密度が低下することも影響するが、それ以上に、加工穴内で生起された溶融・飛散物を効率よく外部へ排除することが重要となる。低融点材料を除き、一般の金属材料の除去加工では、照射による瞬間的な蒸発の割合はさほど大きくはないとされている3)。
目次へ ∧
極薄板や薄板のレーザーによる穴あけ加工の場合は、レーザーの集光ビームを照射すると瞬間的で爆発的なプラズマ発光などを伴って穴があき、熱源中心近傍に位置する部分は瞬時に抜ける。さらに次の瞬間には熱源の裾の部分によって横方向へと熱拡散が起こり穴径を拡大する。このように極めて短い照射時間内に2段階の過程を経て加工が行なわれる。したがって、投入された全レーザーエネルギーが全照射時間を通して加工に関わるのではない。図3には、穴あけ加工における投入エネルギーに対する関与エネルギーに関係を示した。穴径が増大すると貫通するエネルギーも増えて、実際の関与エネルギーは減少する。このような加工プロセスはレーザー穴あけ加工特有のものである4)。この場合の例として、極薄板や箔(10/μm)をYAGの第3高調波によって穴あけ加工された場合の例を図4に示す。正確な実測は難しいが、加工穴の材料表面ほどには材料内の実質的な熱影響層は大きくはない。
シミュレーションによると、ほぼ連続波に近い穴あけ加工では、レーザー照射によって材料表面にできた溶融金属がアシストガスによって穴の周辺部分へと押し出されて盛り上がっていく様子が見てとれる。穴が貫通すると、ガスの流れは一変して側面より下方への強い流れとなる3)。また、等間隔に穴あけを実施すれば、一面に穴加工を施したマトリックス状の多数穴あけ加工も可能である。薄板の穴あけ加工の理論では、Nd3+:ガラスレーザ一Qスイッチによる単パルス当たりの加工深さを、熱的な解析を行なった例がある5,6)。
ここで、Edはエネルギー密度(J/cm2)、Qは被加工材の密度(g/cm3)、は被加工材の蒸発潜熱(cal/g)、cは被加工材の比熱(cal/g・°C)、Tvは沸点(°C)である。基本的に蒸発による除去深さを扱ったもので、その深さが理論的に求まり実験値とよく合うとしている。
しかし、現在の高出力複数パルスによる穴あけ加工では、そのメカニズムがもう少し複雑で、そのようにシンプルな理論で定量的に求めることは難しく、まだ、その妥当性を含めて十分解明されてはいる訳ではない。その理由は以下のようである。高出力では、出力を増しても深さは単純比例しないこと、また、照射によって起こる溶融金属挙動、不純物成分、蒸発蒸気、スパッター、プラズマなどによる光吸収と進行が妨げられる現象があり、その間隙を縫って届いた光照射によって再度加熱され溶融する。これらの穴あけ加工過程の諸挙動はランダム現象である可能性があるなど、複雑な現象が表面と穴内部で生起されるために、純粋な理論式だけで記述するにはやや難があり、加工実験との完全一致には無理があると思われるからである。しかし、膨大な実験値の統計処理による実験式やシミュレーションなどでは一定の範囲で定性的傾向の説明は付くものと思われる。
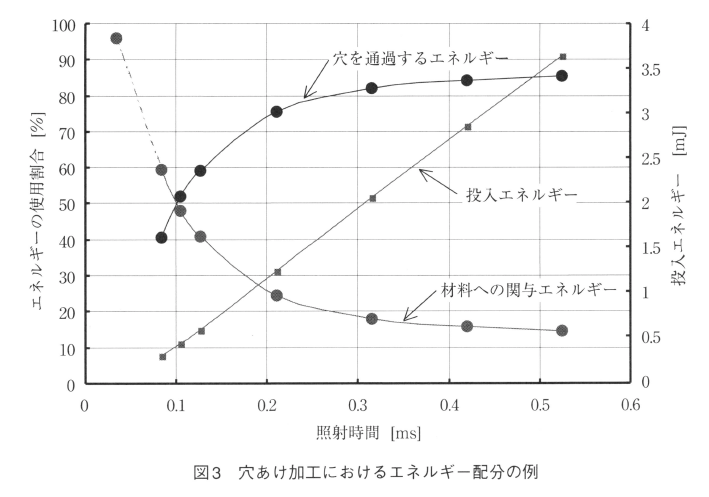
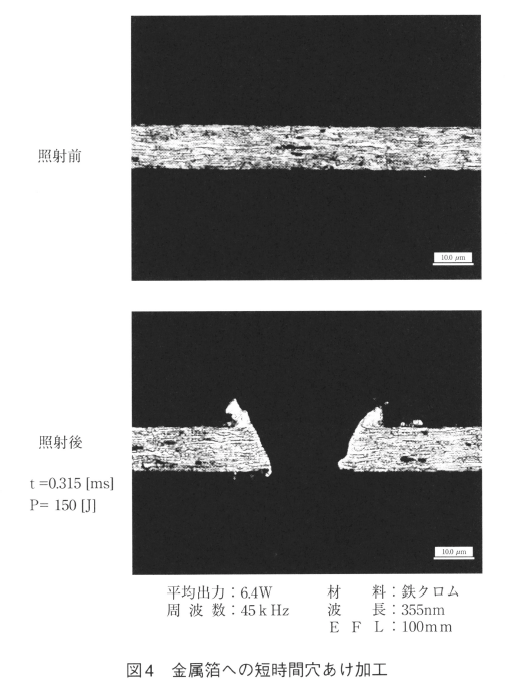
目次へ ∧
1.4 穴あけ加工の種類
(1) 垂直穴あけ
一般的な金属材料の穴あけ加工は、表1に示すような条件で行なわれる。主に軟鋼の場合を示したが、この場合でもアシストガスは必ずしも酸素ガスのみではない。特に軟鋼で板厚が9mm以下の板材においては不活性ガスの窒素や、窒素が4分の3を占める空気(工業用エア一)などを用いることもある。ただし、高出カレーザーで加工する場合において加工穴径が2mmを超えるような穴加工は、現在ではCNC加エテーブル駆動で切断の要領で行なうことは十分に可能となってきた。図5には穴あけ加工の概念図を示す。また、図6には3mmのステンレス鋼材にレーザーを照射し穴あけ加工したものである。加工条件は平均出力260W、周波数200Hz、デューティ比25%、ガス圧力0.1MPa酸素ガスで2秒間の照射であった。
材料表面はパルス波により照射された溶融部が爆発的に飛散し除去される。このような飛散物をスプラッシュと称するが、このスプラッシュの飛散痕が材料表面の穴の周りに見られる。一般に、板厚が厚いほど加工穴径が上面と下面の差が大きくなる。パルス波と連続波ビームの組合せ、或いは周波数の組合せなどによって穴の内部を整形し径の平行度を得る方法もある。いわば研削加工における荒加工に対して仕上げ加工を施すようなものである。
目次へ ∧
任意の角度で斜めに穴をあけるメリットは大きいが、一般的な機械加工では難しいとされている。しかし、レーザーではそれが可能である。特に、Nd3++:YAGレーザーは斜め入射が可能で、材料に対する入射角(垂線からみた入射角)は60°までほぼ安定して斜め穴加工を実施することができる。材料面からみた場合には、入射角は材料に対して斜め30°から加工することに匹敵する。これはNd3+:YAGレーザーの波長(λ=1、064nm)は金属に対する波長吸収がよいこともあるが、それ以上にピーク出カが20kW以上というようなパルス尖(せん)頭値の高い発振機能を有していることによるところが大であるとされている。図7にその例を示す7)。材料は板厚3mmのステンレス(SUS304)鋼材で、図(写真)の下段は角度のみを変化させパルス発振で穴あけ加工の例で、上の段はこのビームに光学的に微小な半径で回転を加えたものである。いずれも入射角が30°から可能であることが分かる。このような方法を用いて実際に航空機でタービンブレードの穴加工を行っている。
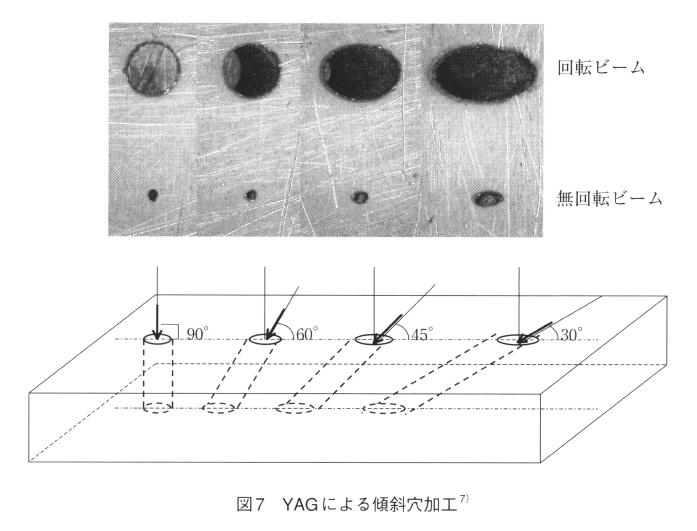
目次へ ∧
上の例でも挙げたがレーザービームを何らかの方法で回転させて穴あけ加工を行なう場合がある。同様に光学的にビームを偏心させて回転し、その回転ビームを用いて穴あけ加工を行なうこともできる。図8にはその原理の一例を示す。このようにして得られた回転ビームによって加工を行えば、穴径は若干大きくはなるものの、入射穴径の真円度は向上し上下の穴径の差を低減することが可能である。図9には、通常のビームによる穴あけ加工と回転ビームによる穴あけ加工の実施例を示す。偏心量を増してゆくことで、例えば、回転半径r=0.3mm以上の条件下では加工材料の上面と下面の穴径がほぼー致するようになり、ほぼ平行の穴加工が実現する8)。
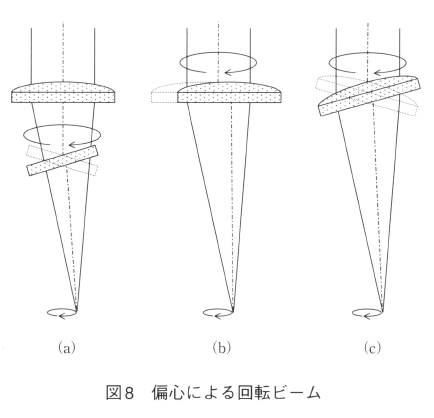
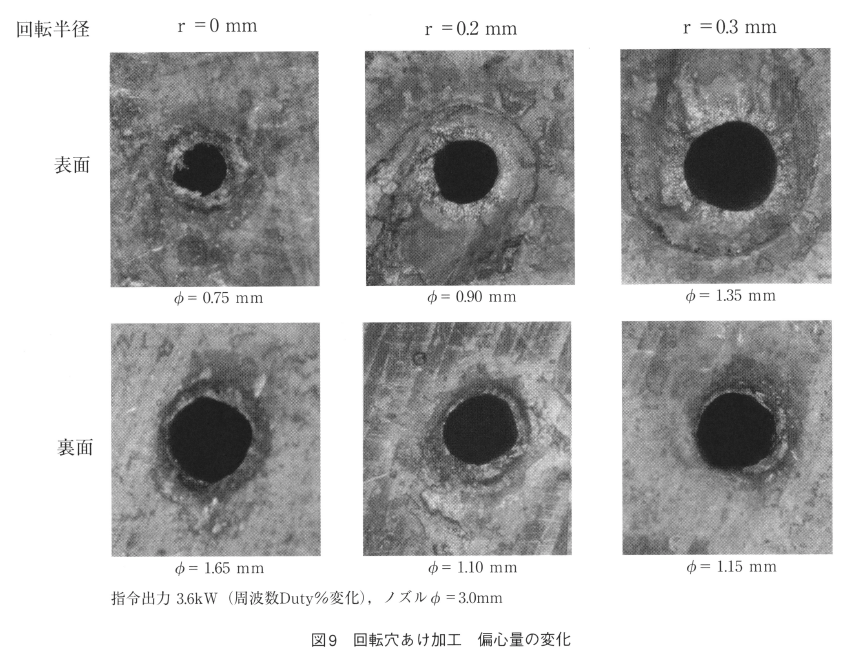
目次へ ∧
1.5 穴あけの加工パラメータ
(1) 焦点位置
一定の厚みを有する板材の場合、レンズの集光位置が穴形状や深さに影響を与える。レンズの焦点位置と材料の相対的な位置関係によって異なる(図10)。YAGレーザーによってルビーに穴あけ加工をしたときの例に拠れば、焦点位置が材料内部にある場合には、ほぼ中央に中太りが生じ、加工物外部に焦点位置を移すと、穴形状は中央部が細くなり、その後に円錐状になるとしている1)。この度合いは同じ材料の場合でも用いるレンズの焦点距離によっても異なり、材料の種類によっても異なる。より深い穴あけ加工を行なう場合や、より平行の穴形状を必要とする場合には、穴の深さが変化するにつれて焦点位置を移動させる方法も現在では行われている。
目次へ ∧
レンズの固有の値である焦点距離(EFL)は、焦点深度に関連して加工深さと穴径に関しては有効である。短い焦点距離のレンズを用いる場合は、穴径は小さく1パルス当りの深さは大きいが、あまり長い深さを得ることはできない。穴径は多少大きくなるが、長く平行な穴あけ加工を行なう場合には長焦点レンズが有利である。これらは光学の理論的な事実そのものでもある。ただし、穴加工深さは焦点距離に単純比例するものではない。また、現在では加工深さを得るためにはパルスショット数を増す方法で繰り返し照射することで対応している。
目次へ ∧
レーザーによる穴あけ加工は、加工に使われる出力やエネルギーに依存する。穴あけ加工については連続波もパルス波も用いられることは述べたが、特に一定の厚さを有する板材の場合には、パルス照射を繰り返すことにより深さを稼いでいる。パルス照射回数を増やすことは断続的ではあるが照射時間を増やすことである。図11にはパルス照射回数(時間)と加工穴径の関係を示す。また、厚板の穴あけ加工についてはパルス波でしかも周波数を徐々に段階的増加する方法が取られている。これによれば軟鋼の場合で、板厚20mmまで穴あけ加工を行なうことができる。穴径は板厚にほぼ比例して増大する。これは板厚が増すことは穴あけに時間を要することから、付随して穴径も拡大することによる。
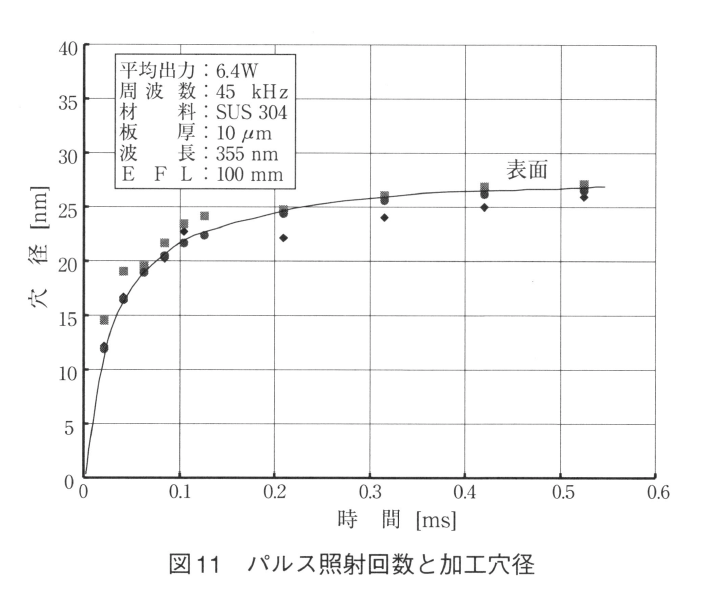
目次へ ∧
2. 穴加工の実際
2.1 金属材料の穴あけ
ステンレス材の穴あけ加工の例を図12に示す。同じ板厚が2mmOSUS304で発振形態を連続波(CW)発振とパルス発振で比較したものである。アシストガスは窒素(N2)で圧力を0.2MPaで、連続発振の場合は出力2kW、照射時間は0.5秒で、パルス発振の場合は、ピーク出力が2kW、周波数100Hz、デューティー比10%で、照射時間は1.5秒であった。連続発振での加工では加工時間が3倍早いが加工穴径は大きく(材料表面でφ0.361mm、裏面φ0.287mm)、パルス発振での加工では、加工時間は3倍であるが、パルス発振の場合の加工穴は小さく(材料表面でφ0.361mm、裏面φ0.287mm)、で連続波(材料表面でφ0.498mm、裏面φ0.396mm)に比較しての30%以上小さい。表面と裏面の穴加工の状況も示す。表面に比べて裏面はそれより小さい径となっている。通常では、穴の内部をほぼ平行に仕上げる成形加工を行なわない限り、材料表面の穴径のほうが裏面の穴径より大きい。
板厚6mmの軟鋼で同様の比較を行なった。アシストガスは酸素(O2)で、連続発振の場合は出力2kW、照射時間は1.0秒で、ガス圧力を0.05MPaで、ノズルギャップを3mmにとって加工した。パルス発振の場合は、ピーク出カが2kW、周波数90Hz、デューティー13〜18%の段階的な変化で、照射時間は2.5秒であった。連続発振では加工時間が早いが加工穴径は大きく(材料表面でφ3.028mm、裏面φ2.519mm)、パルス発振での加工では加工時間は長いが非常に小さく綺麗な穴が得られている。(材料表面でφ0.304mm、裏面φ0.194mm)。
軟鋼の場合において、板厚と穴あけに要する時間の関係を図13に示す。材料はSPCCでピーク出力が3.6kWのCO2レーザーを用い、パルス条件は周波数100Hzで、デューティー比は15%、アシストガスに酸素0.1MPaを用いた。その結果、板厚が増すにつれて貫通に要する加工時間が指数関数的に増大してゆく。
目次へ ∧
2.2 非金属材料の加工
昨今のレーザーによる穴あけ加工はその用途の広がりと、軽薄短小の技術革新に支えられて材料の種類はもちろんのこと、微細穴あけ加工や材料の変化から金属の薄板加工とポリイミドや石英などが多くなってきた。穴あけ加工も従来の金属一辺倒や何でも加工を試みた時代とは異なってきた。ここでも需要の変化に対応した材料の加工を例に採り上げる。
目次へ ∧
炭酸ガスレーザーを用いた微細穴あけ加工は、短パルスの高繰り返しと高い尖頭値を得られるTEACO2レーザーによるものが多い。以下に平均出力80WのTEACO2レーザーのパルス照射による穴あけ加工の例を示す9)。図14には加工条件:10〜15J/cm2、3〜5ショットの条件下で、ポリイミド(板厚125μm、穴径φ200μm)、石英(板厚500μm、穴径φ400μm)及びテフロン(板厚100μm,穴径φ100μm)の例である。ただし、貫通を意図した穴あけ加工なので、オーバーショットである。
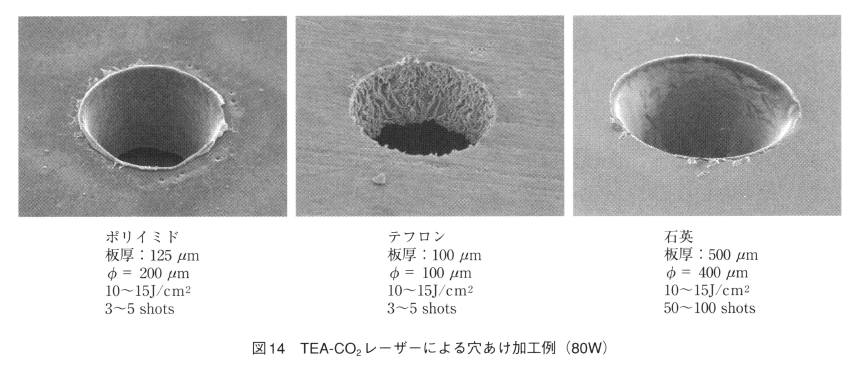
目次へ ∧
つぎに、紫外線の代表的なレーザー加工機である工キシマレーザーでの加工例を示す。エキシマレーザーには波長λ=248nmのKrFレーザーが用いられた。平均出力は60W、加工エネルギーは10J/cm2の条件下で加工された例を図15に示す10)。板厚0.1mmのSUS304の場合、ショット数が1000ショットで加工穴径は表面が約φ0.1mm、裏穴径は約φ0.0901mmであった。また、板厚0.1mmのCu(銅シート材)の場合、ショット数が1000ショットで加工穴径は表面が約φ0.1mm、裏穴径は約φ0.074mmであった。さらに、板厚0.05mmのNi(ニッケルシート材)の場合、ショット数は500ショットで加工穴径は表面が約φ0.1mm、裏穴径は約φ0.093mmであった。
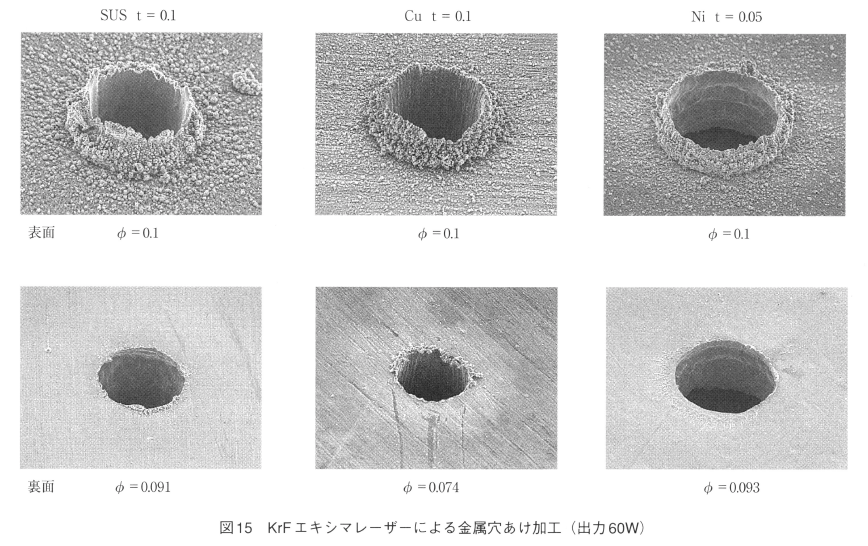
目次へ ∧
プリント基板の穴あけ加工は現在もCO2レーザーが主流である。銅箔に対する加工性のよさからYAG第3高調波も有力な加工手段となっているが、樹脂の加工性から来る有利さに加えて、CO2レーザーはモード改善によって更に穴の小径化につながり威力を見せている。図16にはCO2レーザー(λ=9.3μm)を使用して加工したプリント基板の例を示す11)。プリント基板の代表的な2種類の使用樹脂を採り上げる。ガラスエポキシ樹脂の場合、加工エネルギー30mJでパルス幅15μs、ショット数は5shotsのとき穴径φ=200μmであった。また、エポキシ樹脂の場合、加工エネルギー0.8mJでパルス幅3μs、ショット数2shotsのとき穴径φ=90μmであった。その表面写真と断面写真を示す。
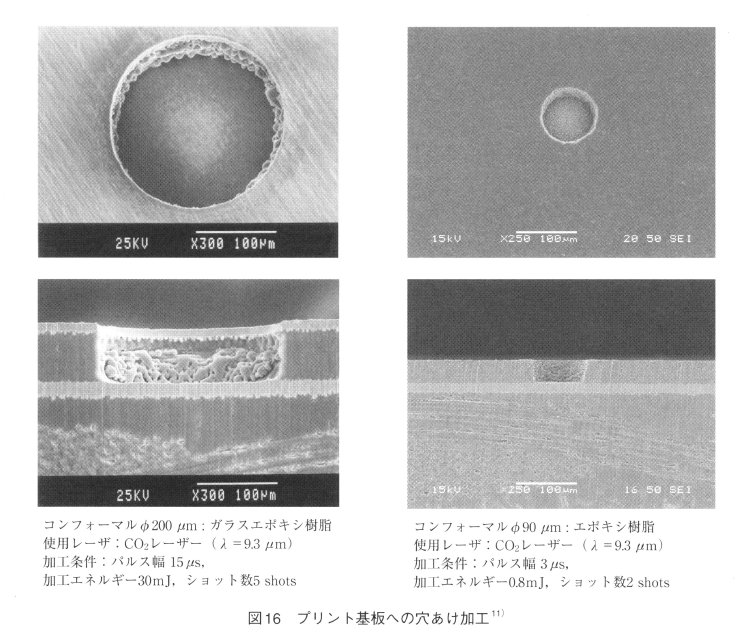
目次へ ∧
[参考文献]
1)小林昭:「レーザー加工」、開発社(1973)同、「続レーザー加工」、pp104 開発社(1980)
2)新井武二:レーザーによる加工シミュレーション(第8報) 2004年度精密工学会秋季大会講演論文集 J18 pp521 (2004.10)
3)新井、堀井、井原:レーザーによる加工シミュレーション(第1報) 2001年度精密工学会春季大会講演論文集 C12 pp103 (2001.3)
4)新井、岩本、井原:レーザーによる加工シミュレーション(第10報) 2005年度精密工学会秋季大会講演論文集 E31 pp103 (2005.9)
5)金弼鉉:レーザー加工技術講座、(第1分冊)工学研究社 昭和46年 (1971)
6)J.E,.Norton & J.G.McMulen, J Appl. Physi. 34 12(1963)
7)写真提供(斜め穴あけ加工):東成エレクトロビーム(株)
8)写真提供(回転ビーム):アマダ 旧、レーザー応用技術研究所
9)写真提供(TEACO2レーザー加工):東成エレクトロビーム(株)
10)写真提供(エキシマレーザー加工):東成エレクトロビーム(株)
11)写真提供(ビア加工):三菱電機株式会社
目次へ ∧