超高出力ファイバレーザによる切断加工の進歩
超高出力ファイバレーザは、空気アシストを使った鋼材の切断など、高速で高品質な厚材切断が可能で、他の切断手段に勝る多くのメリットがある。
10〜40kWレベルの超高出力(ultrahigh power:UHP)ファイバレーザは、この数年間で切断用に急速に普及しており、切断に適用される最大レーザ出力は、ますます高まることが予想される。本稿では、この出力レベルの切断加工結果を紹介し、UHPファイバレーザの利用を促進している多くの要因について解説する。その要因とは、生産性の面で顕著なメリットがあること、切断品質が高いこと、切断可能な厚さが大きいこと(本稿では厚さ230mmの鋼材を40kWで切断する例を紹介)である。
ここでは、出力が10kW以上のものをUHPレーザと定義する。UHPレーザは、新しい加工方式を可能にして、レーザ切断の新たな市場への拡大を促進するものである(例えば、最大50mmの鋼材を、空気アシストガスを使用することによって、高出力プラズマよりも4倍高速に切断する)。応用結果からは、UHPレーザが、窒素や酸素を使う切断プロセスを、空気アシストによる高品質で高速で経済的な切断に置き換えて、鋼材の切断方法を変えていることがうかがえる。
レーザ切断は、約50年前に誕生して以来、目覚ましい技術的進歩を遂げてきた。商用レーザ切断機が登場して、いち早く導入した企業によって量産に使われ始めたのは、1970年代のことである。1980年 代 には二 酸 化 炭 素(CO2)レーザ切断システムの利用が拡大し、1990年代終盤から2000年代初頭にかけては、高出力ファイバレーザが登場した。2000年代終盤には、kWレベルのファイバレーザ切断機が開発されて、レーザ切断は、ニッチな特殊用途に適用されていた状態から、主流の製造プロセスへの移行を果たした。ファイバレーザ切断は、板金のレーザ切断市場の大半を占めている。組み込みが容易、信頼性が高い、メンテナンスの必要性が低い、資本コストと運用コストが比較的低い、切断スループットが高い、出力調整が可能というのが、その主な理由である。
2010年代終盤から2020年代初頭には、レーザ切断の市場成長が2つの方向に分岐し始めた。1つは市場の低出力側で、資本設備コストの削減を目的に、1〜3kWの切断機の需要が急増していることである。その一方で市場の高出力側においても、UHPレーザの需要が増加している。こちらは、経済的なコストで高い生産性と技術的能力が得られることがその要因である。この期間にレーザ切断は、他の板金製造プロセスではあり得ないほどの著しいペースで、出力が増加した。製造業向けの展示会に出展される切断機の最大レーザ出力は、2015年の6kWから2022年には40kWと、7倍近い増加が見込まれている(図1)。この3年間だけでも、システム出力は15kWから40kWへと2.5倍も増加している。
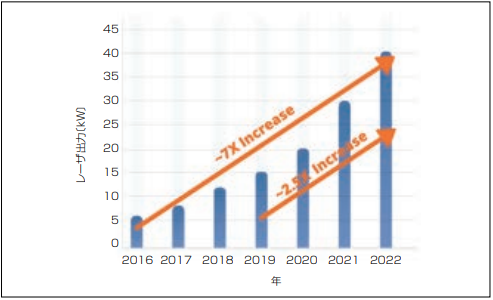
図1 切断システムに使用されるファイバレーザの最大出力の2016年以降の推移
なぜ今なのか
信頼性の高い高出力ファイバレーザは、UHP切断が普及し始める数年前から存在し、2013年には既に、100kWの産業用ファイバレーザが提供されていた(1)。しかし、ここ数年でレーザの1kWあたり価格が急速に低下したことでようやく、UHPレーザ切断を導入するハードルが引き下げられることになった。それだけの光出力レベルを過酷な切断環境で確実に処理するための切断ヘッドや、UHP切断システム用の切断ライブラリも、提供されるようになった。
テスト設定
本稿のテストでは、40kWの「IPGYLS-40000」 と30kWの「IPG YLS30000-ECO2」という、高電力変換効率(Wall-Plug Efficiency:WPE)のファイバレーザを使用した。ファイバコア径は100μm、切断ヘッドには「IPGCut-HP」を使用して、さまざまな金属の切断速度と品質を評価した。筆者らの知る限り、100μmのファイバコア径で40kWのレーザ出力というのは、産業用レーザ切断にこれまでに適用されたレーザ光源の強度として最高レベルである。100μmのファイバコア径を選択したのは、150μmのコア径よりも切断速度がさらに10〜25%高くなるためである。
高い切断速度
この実験により、ステンレス鋼、炭素鋼、アルミニウムというテスト対象のすべての金属に対して、レーザ切断速度は、40kWまでの平均出力の増加に伴って増加することが示された。図2は、厚さ6〜40mmの炭素鋼に対し、空気アシストガスを使用して12〜40kWのレーザ出力を適用した場合の切断速度の増加を示したものである。金属の厚さが大きいほど、速度の増加率は高くなる。例えば、厚さ12mmの炭素鋼に対して出力を15kWから40kWに上げると(出力の増加率は270%)、切断速度の増加率は280%であるのに対し、厚さ20mmの炭素鋼の場合は、切断速度は420%増加する。厚さ30mmの炭素鋼の場合は、出力を30kWから40kWに上げると(出力の増加率は33%)、切断速度は66%増加する。これは、さらに高出力のUHPレーザによって、厚材切断の生産性がさらに高まる可能性を示唆している。
UHPレーザの高い切断速度を利用して、サイクルタイムを大幅に短縮するには、特に厚みのある材料の場合は、高い加速度で部品を切断することが重要である。近年、一般的な切断機の最大加速度は、さらに高いレーザ出力に対応するために、1gから3gに引き上げられている。ハイエンド側では、6gもの加速度を備えたUHPレーザ切断機が登場しており、切断パスが大きくずれることがないようにそれだけの力を支える機械設計が採用されている。
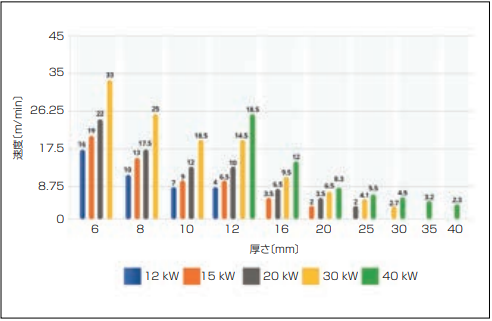
図2 炭素鋼に対する空気アシストを使用したドロスフリー切断の速度と出力の関係
部品あたりコストの低下による投資回収期間の短縮
UHPレーザ切断は、(低出力の場合と比べて)部品あたりコストがはるかに低く、投資回収期間の短縮と収益性の増加につながる。レーザ切断において、運用コストの大きな割合を占めるのは、ガスの消費で、ガスのコストは部品の厚さとともに著しく増加する傾向にある。
UHPレーザ切断に必要なガス圧力とノズルサイズは、低出力切断と同等かそれ以下である。しかし、切断速度が著しく増加するため、部品あたりの切断時間が短くなり、ガスの消費量は大きく減少する。例えば、一般的な厚さ16mmのステンレス鋼を30kWのレーザで切断すると、15kWのレーザと比べてサイクルタイムは半分になるため、ガスの消費量は半分になる。
レーザとチラー(冷却装置)の消費電力は一般的に、出力に比例して増加する。しかし、切断機のそれ以外の部分の消費電力は、ほぼ変わらない。従って、上記の例のように部品あたりのサイクルタイムが半分になると考えると、レーザ出力の増加によって、部品あたりの全体的な電気コストは低下することになる。継続的な進歩に伴って、高出力ファイバレーザのエネルギー効率は50%を上回っており、電気コストのさらなる削減が期待できる(2)。
UHPレーザには、高い切断速度以外にも、ガスの消費量の減少につながる要因がある。UHPレーザは高圧空気によって厚みのある炭素鋼を、よりコストの高い窒素を使用する場合やはるかに低速な酸素切断よりも、高速にドロスフリーで切断することができる。窒素と空気のどちらを使用する場合も、UHPレーザは、ドロスフリー切断に必要なガス圧力を低くすることができる。例えば、厚さ20mmの炭素鋼に対する15kWでのドロスフリー切断には、16バール以上の空気圧力が必要であるのに対し、出力が20kW以上になると、10〜12バールで十分になる。ガスの使用量は、圧力にほぼ比例するため(ノズルサイズが同じ場合)、圧力の大きな低下は、ガス消費量の削減と、ガス発生装置の仕様の緩和につながる。
高出力レーザ切断システムは、低出力の場合と比べて生産性が2倍になっても、価格は2倍にはならない。レーザ出力の増加に伴って、1kWあたりのコストが低下するためである。また、レーザコストの増加が、切断機全体のコストに吸収されるため、低出力レーザ機との価格差はわずかになる可能性がある。従って、高いレーザ出力によって生産性が2倍になるUHPレーザ切断機の資本コストが、30〜40%しか高くないとしても、意外ではない。
はるかに高い生産性を実現するUHPシステムは、1台で複数の低出力システムを置き換えることが可能であるため、必要な設置面積は小さくなり、オペレータの人数は少なくなり、施設の準備作業も少なくなる。その一方で、生産性を維持するためにUHPファイバレーザの光源と切断ヘッドに求められる信頼性の要件は、高くなる。具体的には、ファイバレーザの光源に対しては、半導体、コンポーネント、光学系の高品質な統合によって、長期にわたって安定した出力とビーム品質を維持することが求められる。UHP切断ヘッドに対しては、高い光出力、高圧ガス、粉塵、加工熱、高い加速度に対応して、確実に動作することが求められる。
鋼材切断のための新しいプロセス
炭素鋼は、酸素、窒素、または空気をアシストガスとして使用して、切断することができる。図3は、各アシストガスを使用する場合の利点と欠点をまとめたものである。酸素切断は、酸化反応による追加のエネルギーにより、低いレーザ出力で厚みのある炭素鋼を切断する場合に有効だが、レーザ出力を上げても速度はあまり増加しないため、生産性の面で制約がある。一方、炭素鋼の空気切断では、出力の増加に伴って速度が増加する(図2)。例えば、厚さ16mmの炭素鋼に対する酸素切断の速度は、出力を10kWから30kWに上げても毎分2m程度で変わらないが、空気切断の場合は、出力を30kWに上げると速度は毎分9m以上に増加し、酸素切断よりも4.5倍高速になる。
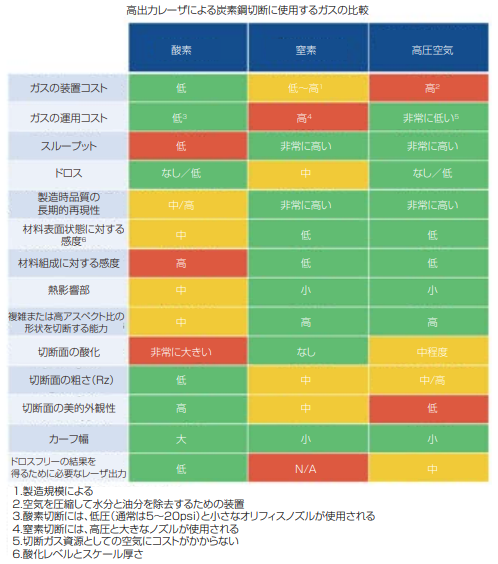
図3 炭素鋼の切断に酸素、窒素、空気を使用する場合の利点と欠点
(もっと読む場合は出典元へ)
出典元
http://ex-press.jp/wp-content/uploads/2023/03/024-029_ft_laser_processing.pdf