進化し続ける積層造形
積層造形は、技術と材料が目まぐるしく進化する状態にあり、その進化に伴って、他の方法では実現できない解決策をますます多くの用途にもたらし続けている。
3Dプリントとも呼ばれる積層造形(Additive Manufacturing:AM)は、30年以上前に初めて登場して以来、急速な成長を遂げてきた。1984年、3Dプリントプロセスに関する初めての主要な特許を、光造形法の発明者であるチャールズ・ハル氏(Charles Hull)が取得した。ほぼ同じ時期に、3D押出の熱可塑性部品を発明した米ストラタシス社(Stratasys)も複数の特許を取得している。それ以来、多くのことが業界内で成し遂げられてきた。
光造形法は、ポリマーと金属の両方をプリントするためのさまざまな種類のレーザ技術と同様に、産業用レーザを使用するものだった。
ポリマー
ポリマー部品を造形するための複数の技術が存在する。液槽光重合法(vat photopolymerization:VPP)では一般的に、紫外(UV)光源を使用してフォトポリマーを硬化する。熱は、エネルギー源としても使用できる。光造形法としても知られるVPPプロセスは、レーザを使用して造形タンク内で液状の樹脂層を1層ずつ硬化することによって、物体を造形する。米エンビジョンテック社(Envisiontec、現在のETEC)は2002年に、DLP(Digital Light Processing)プロジェクターを、フォトポリマーを硬化するための代替光源として使用するシステムを発表した。これらのシステムは、一部の用途においてレーザベースの光造形法の代わりに使われるようになった。一部の例外を除き、DLPシステムは、それよりもフレームが大きな光造形法よりも、小さな部品の造形に利用されている。小型部品用のVPPは、歯科分野のさまざまな用途に一般的に用いられている。
ポリマー部品製造に対する2番目に主要な技術は、粉末床溶融結合法(Powder Bed Fusion:PBF)または選択 的レーザ焼 結 法(Selective Laser Sintering:SLS)である。レーザエネルギーによって粉末状ポリマーの層を溶融し、1層ずつ融合することによって部品を造形する(図 1)。SLSに用いられる最も一般的な材料は、ナイロンとしても知られる、ポリアミド(PA)12である。良好な材料特性を備えた完全に機能する部品が、出力される。部品は溶融粉末から作られるため、表面仕上げは粗く、平滑化や塗装などの後処理が通常は必要である。さまざまな産業用途において、部品設計にもよるが、製造個数が最大で数万個までの少量生産の部品に対して、従来の射出成形に代わってSLSが使用されている。1987年に、テキサス大オースティン校からスピンオフしたDTM社(後に米3Dシステムズ社[3D Systems]が買収)が、このプロセスを初めて開発した。
ポリマーの3Dプリント手法の最後を締めくくるのが、材料押出法(material extrusion:MEX)と材料噴射法(material jetting:MJT)である。前者は、熱溶解積層法(Fused Deposition Modeling:FDM)として広く知られており、加熱して溶かした熱可塑性樹脂をノズルから吐出して部品を造形する。後者は、産業用インクジェット技術を利用して、フォトポリマーを造形プレート上に選択的に噴射し、UV光を当てることによって硬化する。これら2つのプロセスには、レーザ技術は利用されない。
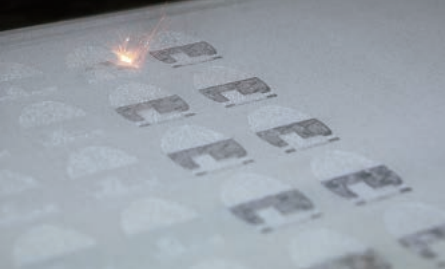
図1 粉末床溶融結合(PBF)システムでプリントされた金属工具部品。(画像提供:独EOS社)
金属とセラミック
機能的な金属及びセラミック部品の製造方法は、基盤技術の価格が低下したことを受けて、ここ数年で著しく進歩した。金属AMプロセスとして群を抜いて最も一般的なのは、PBFである。ポリマーに対するPBFプロセスと同様に、加熱された不活性の造形チャンバの中の金属粉末を、レーザビームで溶融して部品を造形する。造形プロセスは、プリント対象の金属合金の融点に達することで、粉末を融合して機能的な金属部品を生成する。部品には支持構造が必要で、造形完了後にそれを除去する必要がある。ポリマーのPBFと同様に、部品は溶融粉末から作られるためにかなり粗く、所望の表面仕上げを得るために、平滑化、研磨、または機械加工が通常は必要である。また、PBFプロセスの間に増大する負荷を軽減するために、部品の熱処理が一般的に必要である。一部の用途に対しては、最大限の密度を達成するために、熱間
等方圧加圧法(Hot Isostatic Pressing:HIP)が必要となる場合がある。アルミニウム、チタン、コバルトクロム、ステンレス鋼、ニッケル基超合金、銅など、幅広い種類の材料が、このプロセスで使用できる。
指向性エネルギー堆積法(Directed Energy Deposition:DED)は、溶接に似たプロセスによって、金属材料を溶かして金属部品を造形することで特徴づけられる、一連のプロセスである。材料は、金属ワイヤまたは金属粉末として供給することが可能で、材料を溶融するための熱源は、レーザまたは電子ビームによって供給することができる(図 2)。
関連する非加熱プロセスの1つに、金属粉末ストリームを高速に加速することによって部品を造形する、コールドスプレー法がある。このカテゴリーに分類される技術はどれも、粗くて精度の低い部品しか生成しないため、最終形状を得るために機械加工が必要である。DEDは一般的に、大型部品に適用される。加工が難しい金属が使用される場合は特に、正味の形状に近い、完全に機能する部品の生成は、長い加工時間の短縮につながる。一部の用途においてはこれが、従来のコンピュータ数値制御(Computer Numerical Control:CNC)加工に勝るメリットとなっている。CNCのような減法製造プロセスでは、金属の一部を取り除いて所望の形状にするためにエネルギーが必要で、かなりの廃棄物が排出される。より持続可能なプロセスをメーカーが追い求めるこの時代において、それはマイナス面でしかない。
金属部品を製造するためのその他の非加熱プロセスとして、金属またはセラミック部品に対するVPPと、結合剤噴射法(binder jetting:BJT)がある。前者では、金属またはセラミックを充填したフォトポリマースラリーの硬化に、レーザビームが使用される場合がある。後者は、結合剤をインクジェットから噴射して金属粉末を接着させるものである。どちらの方法にも、最終製品の製造に焼結が必要である。
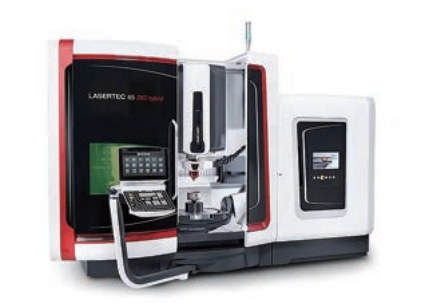
図2 「LASERTEC 65」は、指向性エネルギー堆積法による積層造形とミリング加工を1つの装置に融合したものである。(画像提供:DMG森精機)
(もっと読む場合は出典元へ)
出典元
http://ex-press.jp/wp-content/uploads/2022/09/030-033_ft_additive_manufacturing.pdf