レーザアシストμ-LAMプロセスが赤外オプティクスを切り開く
赤外オプティクスやセラミクスなど、高硬度、低破壊靭性を持つ光学材料を直接加熱し熱的に軟化させることで、マイクロレーザアシストダイヤモンド旋削は、材料除去率を高め、製造コストを削減する。
幅広い材料、金属と合金、セラミクス、ガラス、半導体、複合材料を含め、これらは所定の形状、精度、仕上げ、表面完全性などサービス要件を満たすように製造される。金属と合金一般は、加工が容易である。高破壊靭性、低硬度、無指向性結合、低空隙率、破砕につながる大きなひずみ、高衝撃エネルギーのためである。一方、セラミクス、半導体、光学結晶および多くの赤外光学材料などの非金属は、共有結合またはイオン結合、塑性変形のためのリミッテッドスリップシステム、高硬度、低破壊靭性を特徴としていることから、加工が一層困難になっている。
マイクロレーザアシスト加工(μLAM)と呼ばれる新技術が、勢いづいている。対象となるのは、光学結晶、シリコン(Si)、 フッ 化カルシウム(CaF2)、セレン化亜鉛(ZnSe)、ゲルマニウム(Ge)、硫化亜鉛(ZnS)を含むIR材料である。米マイクロラム社(Micro-LAM)で行われた材料研究からも明らかなように、μ-LAM技術の価値提案に含まれるのは、光学結晶やIRオプティクス製造中の工具寿命の拡張、生産性増大、部品品質改善である。
レーザアシスト加工
μ-LAM技術は、チップの変形や生成帯で被加工材料を直接加熱し熱的に柔らかくする。これにより材料の展性が増す。材料の堅さが低下したことで向上した展性により、チップ形成が容易になり、脆弱さが低減し、最終的な材料除去率が高くなる。すべてが工具性能向上と生産性向上につながり、さらに製造コスト低下になる。
μ-LAMプロセスによる光学グレードの結晶の加工性を検証するために、15pmの位置決め精度フィードバックシステムを持つダイヤモンド旋削超精密旋盤(UPL)で加工試験が行われた。そのようなUPLは、光学レンズ、光学金型インサートやミラー、小型高精度機械コンポーネントの製造用に設計されている。
分析のために、μ-LAMシステムをUPLに搭載して、回折Siレンズを加工した(図 1)。μ-LAMシステムのツールポスト、OptimusT+1は、既存のツールポストを置き換え、組込み時間60分以下のボルトオンシステムである。レーザコントロールはUPLに接続されているので、Mコードコマンドでそれをコントロールできる。
OptimusT+1は、光ファイバケーブルとコリメートレンズで1064nm YAGレーザに結合されていた。ダイヤモンド工具は、レーザ波長に対して光学的に透明であり、ビームを工具の切断刃半径に正確に向ける集束レンズの役割を果たすように製造されている。これにより、材料の切断ゾーンだけが加熱され、柔らかくなる。
切込み深さ、横送り、切断速度およびレーザパワーなどの加工パラメータを最適化した後、いくつかのSiレンズを作製し、表面仕上げ(粗さ)、表面美観(スポーク、脆弱帯)、形状精度もしくは不揃いトレランス、工具寿命(製造された部品数に基づいて)、生産性(生産性を高めるように加工パラメータを詰める)を評価した。
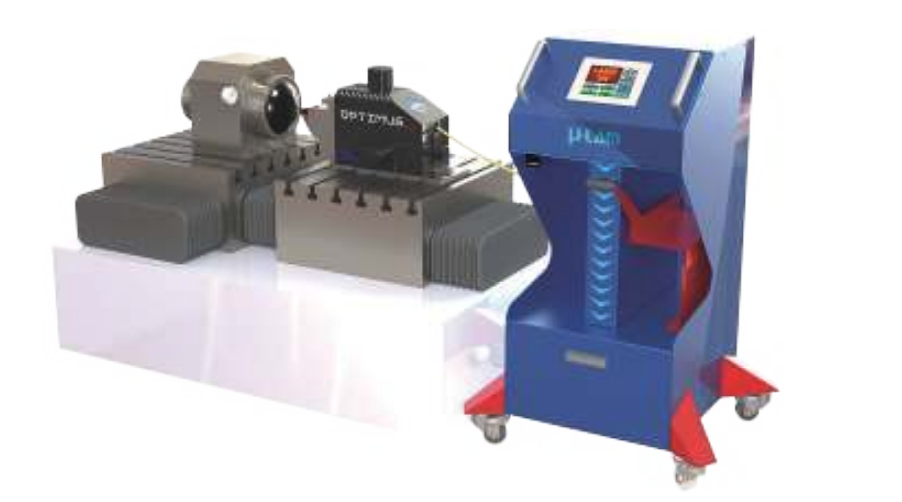
図1 超精密旋盤に組み込まれたOptimusT+1とレーザコントロールステーション。現在のセットアップは、凸型Si回折レンズを加工する位置に設定されたシステムを示している。
直接比較
光学グレードSiは一般にIRイメージングシステム用のレンズとして使用される。以前は、一般に加工がより容易(軟質)であることから、Geが好まれる材料だった。しかし、ゲルマニウムに対するシリコンの優位性はいくつかある。軽量、バルク材料が低コスト、優れた熱安定性と機械的特性、主に高硬度であること。
シリコンの硬度増は、使用時の部品不良を最小化するので好まれるが、それは加工を一段と難しくもする。シリコンの硬さと摩損性のためにダイヤモンド工具は急速に摩滅するので、成形品の品質が悪くなり、高い形状誤差が生ずる。μ-LAMプロセスは、シリコンや他の光学結晶の加工で大きな利点を示した。μ-LAMプロセスでは、一時的に加工対象を柔らかくする(硬さを弱める)ので、工具の摩耗が著しく少なくなる。
IR光学系に使用される直径50.4mmの一般的なシリコン回折レンズは、たとえば、周辺部不揃い許容値は0.5、表面粗さは<10nm Sa、表面品質60-40、スポークなし、グレイまたは脆弱帯なし。ここでの最重要課題は、0.5周辺部(<160nm)不揃い許容値を達 成することで、これは保存状態のよい(摩耗していない)工具の刃先でしか達成できない。
(もっと読む場合は出典元へ)
出典元
https://ex-press.jp/wp-content/uploads/2018/01/pa_IR.pdf