ナノ秒パルスファイバレーザ、金属切断で進歩
ナノ秒パルスレーザは、材料マーキングの用途で広く利用されていることはよく知られているが、それほど知られてはいないものの増加しつつある用途として、ノズルやアシストガスを不要とする、幅広い種類の金属材料の微細切断がある。
ナノ秒パルス幅のファイバレーザがマーキングの用途で有効であることはよく知られている。この10年間で、金属マーキングに対する主流のレーザ源となっており、また、平均出力がますます高まっていることから、エングレービングの分野でも利用が増加している。パルスエネルギーは一般的に数ミリジュール未満で、ピーク出力は約10kW、平均出力は今や100Wにまで達しているため、その能力はかなり高い。
英SPIレーザーズ社のパルスファイバレーザは、半導体シードレーザに光ファイバ増幅器を組み合わせたマスターオシレータパワーアンプ(MOPA:Master Oscillator Power Amplifier)をベースとしており、従来のQスイッチ設計と比べてパルス特性に対するかなりの制御が可能になっている。
このようなナノ秒ファイバレーザが生成するパルスは、立ち上がり時間が短いという特長がある。そのため、ガウスエネルギー分布を持つ従来のQスイッチパルスと比べて、対象材料に対するより効果的なビーム結合が得られる。スキャナベースのビームデリバリシステムを備えるナノ秒ファイバレーザは、動作波長1.06μmで、非常に高速な材料加工速度を達成することができる。
通常はマーキングに適用されるナノ秒パルスファイバレーザだが、現在では多用途性と制御にかなり優れていることから、エングレービング、アブレーション、スクライブ、テクスチャリング、微細切断など、さまざまな微細加工用途でも他の手段と渡り合えるまでになっている。1kHz〜1MHzという幅広い繰り返し速度と、3〜500nsの可変パルス幅制御を備えることから、これらのナノ秒範囲のパルスファイバレーザは、連続波(CW:Continuous Wave)モードと変調疑似CWモードで動作することができる。
金属箔
薄い金属箔を完全に貫通するためには、切断速度がナノ秒パルスファイバレーザのシンプルなシングルパス処理を制御するパラメータとなる。また、この処理は通常スキャナベースであるため、加工ガスは不要である。
スキャナビームデリバリによる金属箔切断は、アブレーションと溶融物除去によって行われ、刻み目のない切断部が得られ、熱影響部(HAZ:Heat Affected Zone)は最小限となる。例えば、電池の銅箔やアルミニウム箔は複合材料となる場合がある。一般的に、20〜40μmの金属芯が複数のプロプライエタリな層に挟まれており、材料の厚さは合計で約100μmとなる(図 1)。このような電池箔は、70〜100Wのパルスファイバレーザによって、1m/sを超える直線切断速度で切断することができるため、レーザ切断の方が機械切断よりも優れた選択肢となる。機械切断には、工具の摩耗や定期的な保守に加えて、全般的に柔軟性に欠けるという欠点がある。
この用途では、切断品質が非常に重要で、刻み目が最小限になることと、薄膜コーティングを傷つけないことが不可欠である。切断品質は、パルスと加工パラメータの最適化によって制御可能だが、一部の材料については、2パスの処理によってエッジ品質が改善されることが明らかになっている。
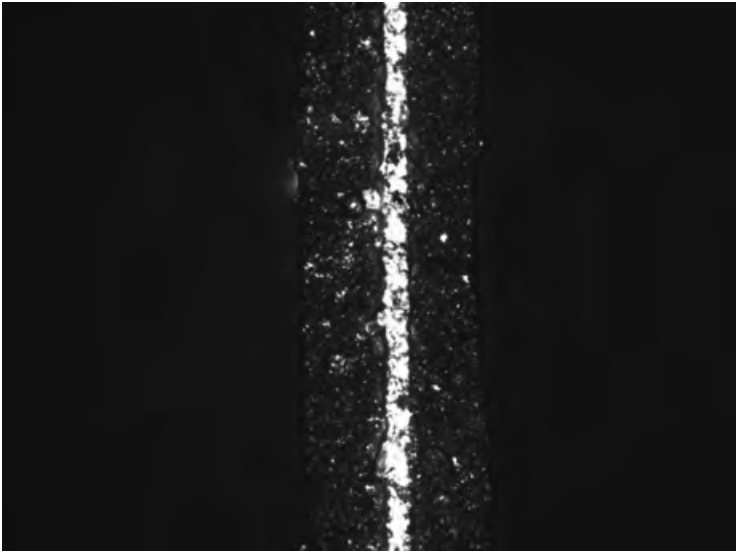
図 1 ナノ秒パルスファイバレーザは、電池箔を簡単に切断することができ、シングルパス処理で切断できる場合も多い。
厚みのある金属
0.5mmまでの厚い金属材料を切断する場合は、材料を完全に貫通するために、複数のビームパスで同一経路を処理することが必要になる場合が多い。しかし、この手法には制約がある。複数のパスによって溝の深さとアスペクト比が大きくなるにつれて、材料表面のビームパラメータの最適化が低下することから、ビームの減衰と、材料加工効率の低下が生じる。この処理は実は自己限定的であり、スポットサイズの調整と、材料内での焦点位置の移動によって、状況を改善することができる。ただし、その効果はほんのわずかにすぎない。
CWレーザによる切断と同様に、ビーム品質の影響は大きい。ただし、パルスファイバレーザの場合は、ビーム品質として重要なのはM2ではなく、達成可能なパルスエネルギーとピーク出力となる。
ビーム品質の異なる3種類のレーザ(すべて20Wで、同一の光条件で動作)を直接比較すると、最も良好な切断結果を達成したのは、ビーム品質が最も高いレーザ(M2<1.3)ではなかった。品質の高いこのビームはパルスエネルギーとピーク出力が低く、スポットサイズは小さいものの、それらを十分に補うほどではなかったためである。M2 <2のレーザは、結果が最も低かった。パルスエネルギーとピーク出力は高かったが、スポットサイズが大きいために材料に対するエネルギー密度がかなり低くなったためである。M2 <1.6のレーザは、最も優れた結果を達成 た。適度なサイズのスポットに対し、 パルスエネルギーと出力の組み合わせ が最適だったためである。 厚い材料を適切に切断するには、切 り口を効果的に広げてより多くの材料 を除去可能とする、新しい切断手法を採用する必要がある。レーザのスポットサイズを大きくすることによってこれが達成できるが、この方法には、入射エネルギー密度が低下するという悪影響があり、それによって材料除去効率が低くなる。
XYテーブルベースのシステムに特に適したより効果的な方法は、2つのパスの切断ラインを、焦点直径にほぼ相当する距離だけずらし、実質的に切断幅を2倍にすることである。加工後の部品の寸法が許容範囲内に収まり、材料切断部が厚くなるに従って切断エッジがやや先細になるように、注意して プログラミングを行う必要がある。
スキャナベースのビームデリバリでは、商用提供されている標準的なレーザマーキングソフトウエアの「ウォブル」(wobble)機能(もともとは、マーキングラインを広げてより見やすくするために開発されたもの)を使用すると、良好な効果が得られる(図 2)。基本的にこのウォブル機能は、切断経路の軌跡に沿って、ユーザ定義の直径と周波数で円を描くようにビームを振動させる。
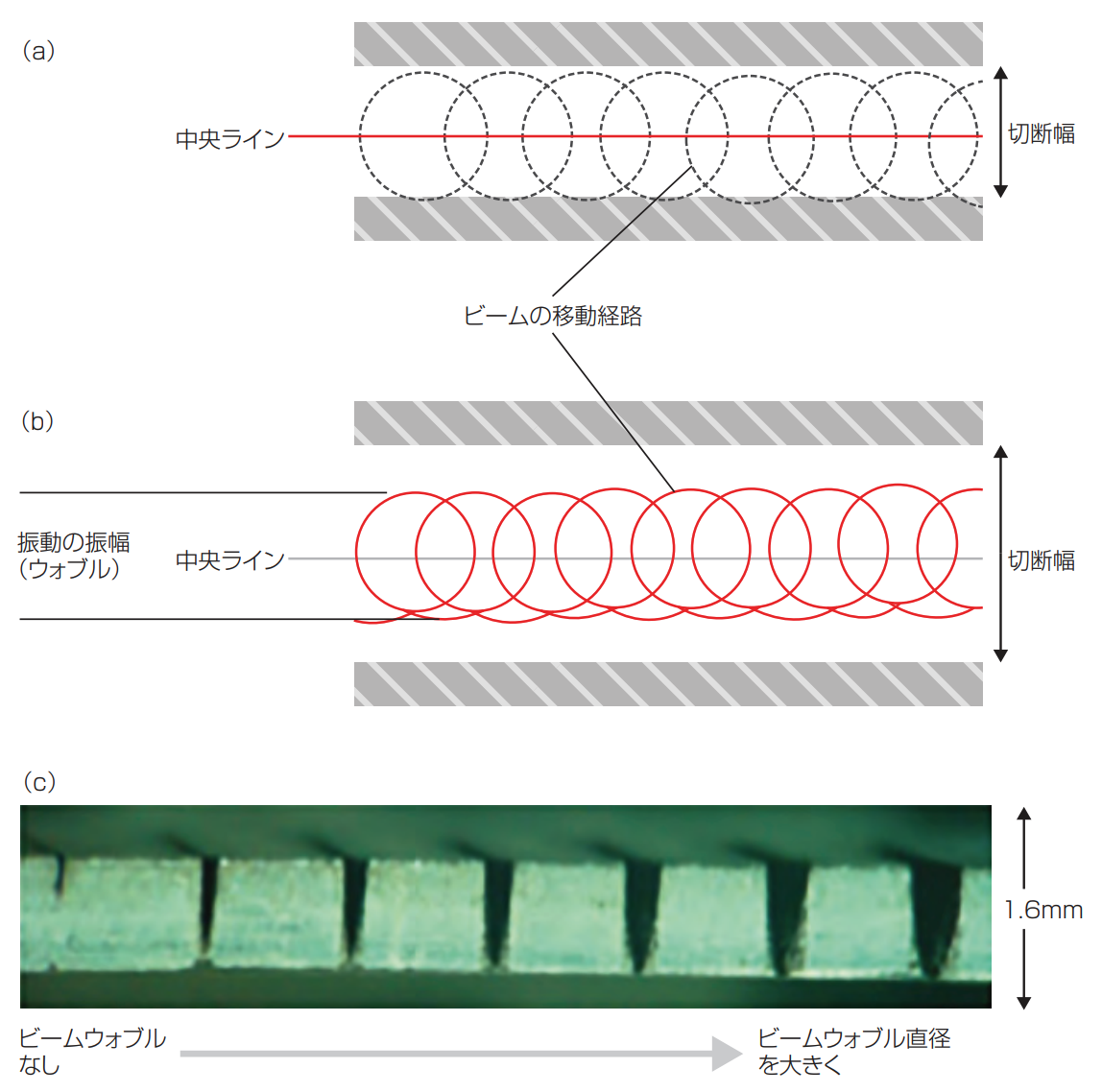
図 2 ウォブル切断の概略図(a)には、標準的な切断経路とそれによって得られる切断幅(b)が示されている。ビームにウォブルを適用することにより、有効切断幅を増加させることができる。ウォブル直径(c)を増加させることにより、金属除去効率は高くなり、切断の深さは大きくなる。
(もっと読む場合は出典元へ)
出典元
https://ex-press.jp/wp-content/uploads/2016/11/LFWJ_Jan16_pa.pdf