大型光部品の半径を精密測定
変位測定、干渉計ベースの曲率半径計測により、環境補正と適切な計測手順をもって、3ppm以内の不確かさで半径を測定できる。
半導体リソグラフィ、リモートセンシング、その他高精度アプリケーション向け光部品の製造は、表面形状や曲率半径など、レンズパラメータの厳しい制御を必要とする。このような厳しいアプリケーションに取り組んでいるエンジニアは、各工程での結果が成功裏に終わることを確実に保証するよう曲率半径測定の不確かさをコントロールしなければならない。
曲率半径を測定するための最も正確な方法は、変位測定干渉計とフィゾーレーザ干渉計を組み合わせた干渉計半径スライドを使用することである。問題は、意図するアプリケーションにとって十分であるかどうかということだ。
フィゾー干渉計を使って基本的な曲率半径測定構成で半径を測定する際に、次の2段階がある。まず、測定される光部品を透過型球面原器(TS)からの球面ビームと調整してヌル干渉縞になるようにする(図1a)。干渉縞がなくなった時、測定物の曲率中心がTS基準面の曲率中心に正確にアライメントされている。その位置は共焦点として知られている。
テスト表面を支持するマウントの軸位置が記録され、次にマウントが、テストされるパーツの表面上の点がTS基準面の曲率中心まで移動する(図1b)。この位置は、キャッツアイと言われることがよくあり、テストパーツに当たる光の鏡像反射、疑似ヌル干渉縞になる。支持マウントの軸位置はキャッツアイの位置で記録される。共焦点とキャッツアイ間にある支持マウントの軸位置の差がテスト面の曲率半径になる。
このコンセプトは単純で自明であるが、物事は細部が難しい。もし測定不確かさ0.01%が必要なら、上述の簡単な測定で所望の結果が得られる。しかし精密光部品では、0.01%の不確かさ(100ppm)では不十分である。これらのユーザーは、これよりも1ケタ、2ケタ優れた不確かさ(1〜10ppm)の達成を求める。
このレベルの精度を達成することは、3つの主要な誤り源を取り除くか、補償する必要がある。これらは大きい方から順に、アッベ誤差、エンドポイント不確かさ、ステージ位置不確かさ。
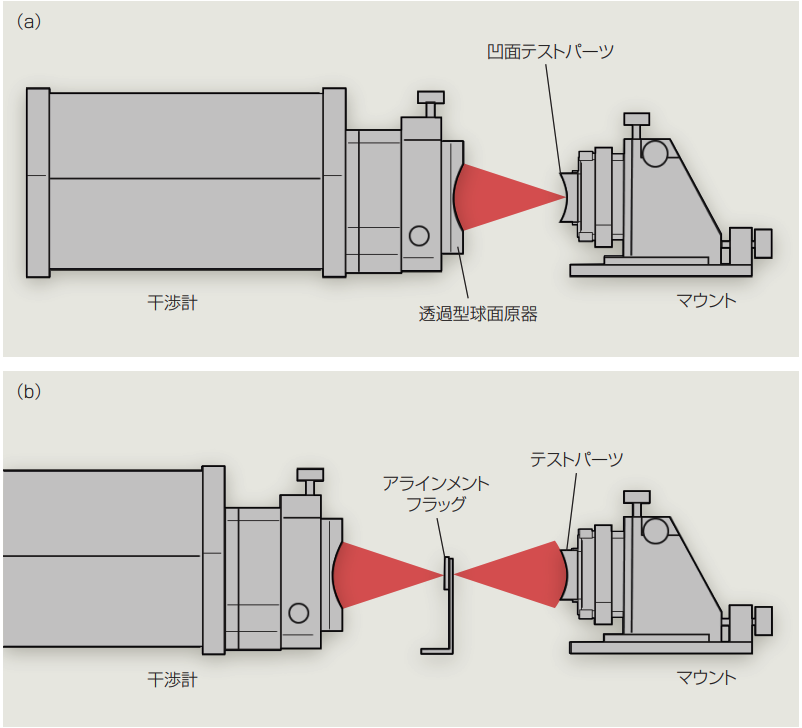
図1 フィゾー干渉計を使って基本的な曲率半径測定構成で半径を測定する際、テストする光部品の共焦点(a)とキャッツアイ(b)の位置が決まる。これらの位置間のサポートマウントの軸の差がテスト面の曲率半径になる。
アッベ誤差
光軸に沿った動作の正確な量を正しく測定するには、精密リニア変位測定機器に接続されたテストパーツの位置を決めるために、適切に設計されたマウントとレールシステムが必要になる。テストされるパーツのz軸動作を測定する通常の方法は、ガイドレールとエンコーダ読み取りヘッド(図2a)に接続された可変マウントのパーツを支持することになる。エンコーダヘッドはステージとともに動き、エンコーダスケールの目盛を読み取る。
概念的には、これは非常に簡単なセットアップであり、数ミクロンの測定精度では効果がある。問題は、ガイドレールを完全に真っ直ぐにできないこと、テーブルを完全に平坦にできないことである。このため、マウントにはいささか「揺動」が出て、アッベ誤差が生ずる(図3)。
簡単な例で、テーブルの平坦さとレールの直線性に対する半径測定の感度を指摘することができる。テストパーツの中心がテーブルよりも約100㎜上にあり、マウントの脚が100㎜離れていると仮定すると、単純な幾何学により、生ずるアッベ誤差はテーブルの平坦さと同じであることになる。同様の議論は、ガイドレールの直線性についても可能である。これらの誤差に対しては、トレランスが1〜5μmが妥当である。
簡単なエンコーダスケールを使用するとき、スケールを光軸の高さまで上げることでテーブルの平坦さが原因のアッベ誤差を少なくすることができるが、それでもまだ、誤差を最小化するために、極めて正確にガイドできる真っ直ぐなガイドレールが必要である。エンコーダベースの半径測定ソリューションを使用すると、1μm以下の不確かさを達成することは非常に難しいことが分かっている。
アッベ誤差を完全になくすには、測定軸をフィゾー干渉計の光学軸と一致させることが必要である。これは、2つの異なる方法で達成可能である。最も一般的な方法は、コーナーキューブを、テストパーツの背後、光軸上に置き、変位測定干渉計(DMI: Displacement Measuring Interferometry、図2b)を用いてこのキューブの変位をモニタする。
この方法を使うと非常にうまくいく。唯一の欠点は、ステージ位置測定のエアパスが、高開口数(NA)、つまり短半径光部品にとっては計測値が大きくなることだ。空気路が長いと、空気ゆらぎによりDMI測定が不安定になる。不確かさを最小にするには、アベレージングと最適な環境調整とが必要になる。
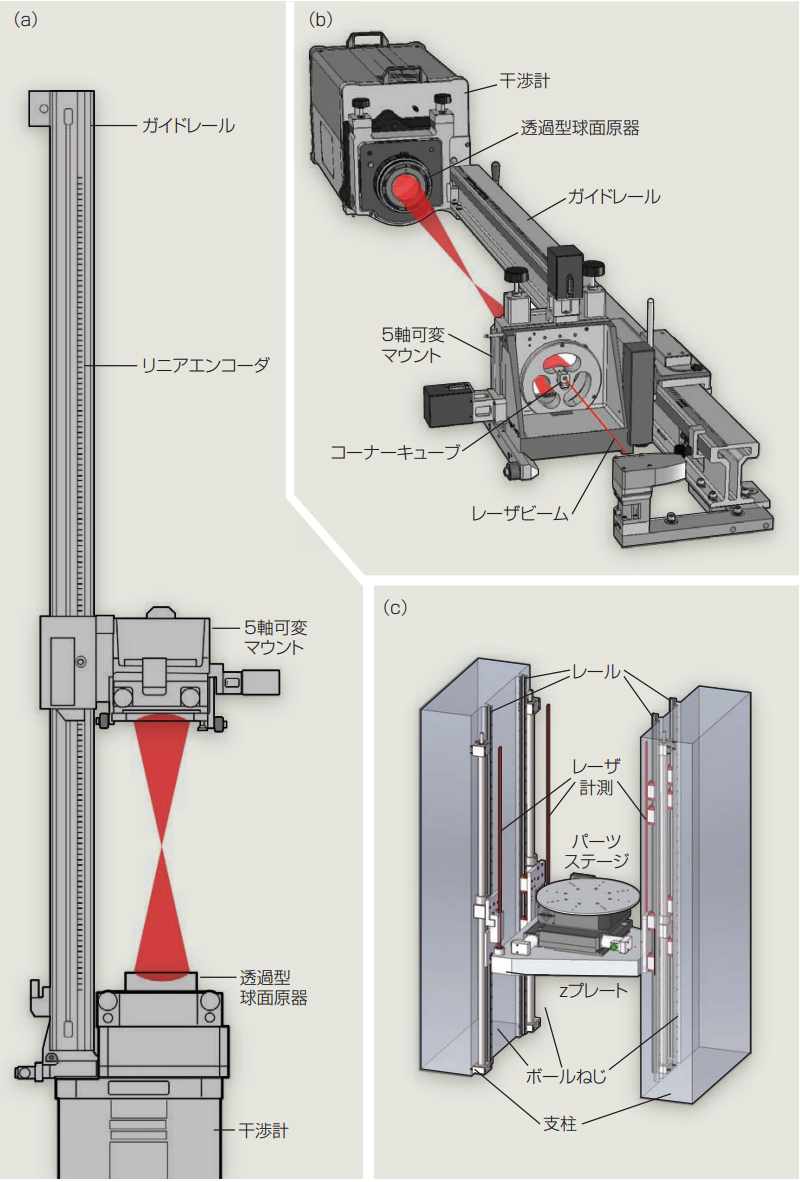
図2 光軸に沿って正確な移動量を正しく測定するするには、テストパーツを位置決めするために、正確な直線変位測定デバイスに接続され、適切に設計されたマウントとレールシステムが必要になる。
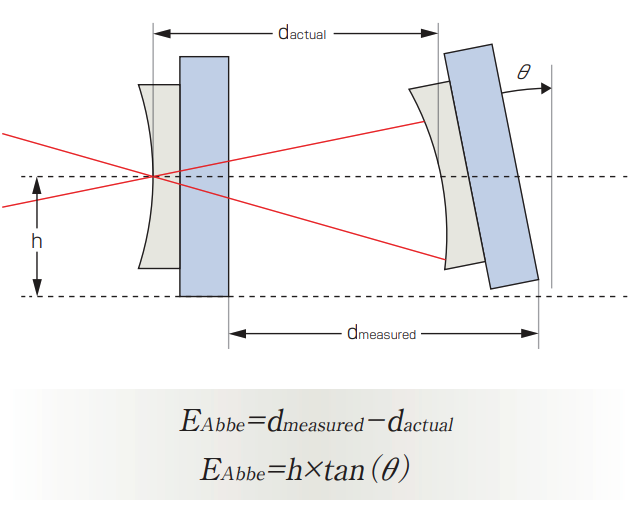
図3 半径測定では、ガイドレールを完全に真っ直ぐにできない、またテーブルを完全に平坦にできないために、マウントにわずかな「揺動」が生ずるので、アッベ誤差が出ることになる。
(もっと読む場合は出典元へ)
出典元
https://ex-press.jp/wp-content/uploads/2014/07/7f8b4c05f6451715206b6360cce2696c.pdf