フェムト秒製造技術によって自動車の燃焼効率改善
フェムト秒レーザ加工を使ってガス直噴インジェクタ(GDI)の噴霧パターンと液滴サイズを制御することでエンジン効率に飛躍的な影響が現れ、性能が30%向上する。
世界中の自動車メーカーが、ますます厳しくなる燃費要求に対しての圧力を受けているが、少なくとも2つの面でこれに取り組んでいる。1つは、再生可能、代替燃料で走る駆動系システムの設計、もう1つは既存の化石燃料エンジン設計から燃費を稼ぐことだ。燃費向上では、研究者はGDIからの噴霧パターンと液滴サイズの制御を改善することでエンジンの効率が飛躍的に向上し、性能が30%改善されること
を見いだした。この発見は自動車設計者にとってはすばらしいことであるが、燃料噴射装置を所要寸法と耐久性で機械加工することは極めて難しいことが実証されている。
従来技術である放電加工機(EDM)、機械的打ち抜き加工、それに従来のレーザ穴開け加工では、燃料流量を仕様に合うように操作できるインジェクタノズル作製に必要な精度を達成することはできない。従来のフェムト秒レーザはGDIノズルを一工程で製造する能力があることが実証されているが、研究室で仕様通りに金属を加工することは、工場環境で実用的な自動車部品を24時間毎日連続で加工することとは異なる。
ガス直噴インジェクタ
欧米では、政府に義務づけられた燃費向上と排ガス規制が、強力で高性能なエンジンに対する消費者の要求と相俟って、自動車部品メーカーは製造技術の開発を進めざるを得なくなっている。米国政府は、2025年までに54.5平均マイル/ガロン(MPG)を義務づけている。EUは、環境保護のために積極的な排ガス削減ロードマップを定めている(1)、(2)。
これに応えて自動車メーカーは、ポート燃料噴射装置(PFI)からGDI形式に急速に移行しつつある。GDIエンジンでは、燃料は燃焼が起こるエンジンのシリンダーに直接噴射される。一方、PFIシステムは燃料と、吸気弁から上流する空気とを混合し、混合ガスをシリンダーに送る。GDIアーキテクチュアの優位性は、希薄燃焼で燃料消費と排ガスを抑制しながらエンジン出力を高める点にある。
GDI設計エンジニアは、燃料流量、噴射角度、粒径分布、燃料質量分布、ノズル先端貫入など、エンジン燃料効率やガス排出量を決める要素が、インジェクタの噴霧口形状や内径表面の粗さで直接制御されることを熟知している(図1)(3)。
こうした要求から、燃料インジェクタ製造業界は変曲点を迎えた。これによって業界は、従来技術で対処できる能力を上回る穴開け機能を導入しなければならなくなっている。従来法では噴霧口の側壁は0.5μm平均粗さ(Ra)、個々の穴(H2H)の直径変動が3%以下に収まるレベルは達成できないが、フェムト秒レーザの穴開けでは0.1μmRa、<1% H2Hは容易に達成できる。さらに、フェムト秒レーザ技術は、新たに必須とされた噴霧口品質、個々のインジェクタ生産で求められる工程スループット(<1秒/穴)の両方を提供できる唯一のソリューションである。
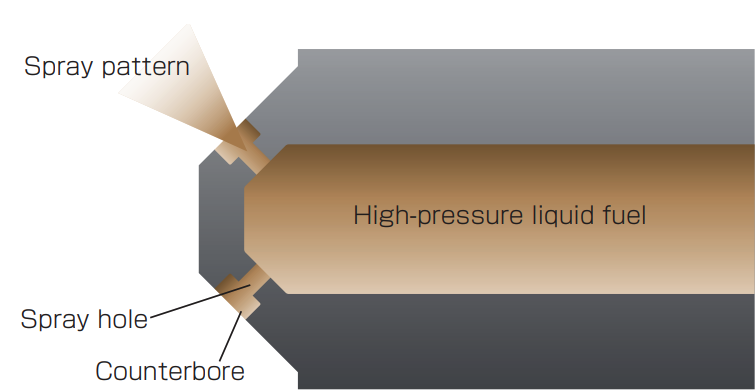
図1 エンジンシリンダー内で燃料を噴射し、霧化する典型的な燃料噴射器の構造を模式的に示した。
フェムト秒微細加工
加工対象に集中する個々のフェムト秒レーザパルスは、材料のわずかな量を気化するが、周辺の材料には影響を与えず、溶かしたり、バリを造ったりすることもなく、熱影響域(HAZ)もない。材料を正確に除去するだけであり、完成品の品質は向上している。
フェムト秒レーザのこのような機能を理解するには、従来の連続波(CW)レーザがどのように材料を加工するかについて基本的な説明からスタートすることになる。レーザ光は簡単に言うと、非常に強度が強い、方向性を持つ電磁(EM)波であり、一般的に波長は紫外(UV)、可視光、赤外スペクトル及ぶ。レーザビームが金属面に当たると、強いEM波によって電子が加速され、他の電子や金属イオンと衝突する。衝突全体の純生産物は急激な温度上昇であり、最終的にはビームが当たった領域は溶けてなくなる。隣接領域では、その熱の多くが拡散し、周辺領域に損傷を与える。
CWレーザに対して、ピークパワーが>1MWのパルスレーザを用いると、短い連続的閃光で材料に当たるEM波の強度は一段と強い。個々の閃光(パルス)ではEM強度は極めて強いので、電子は加速されるだけでなく、その多くはビームの当たった金属の領域から実際に飛び出し、イオン化された多量の材料から、高圧プラズマが形成される。微小な爆発によって圧力が緩和され、イオン化された量から材料片が噴霧される。この場合、光電離によって材料は除去されるが、より長いパルス幅のレーザ(ナノ秒、ピコ秒パルスレーザを含む)は、なおも大量の電子衝突を起こし、各パルスの立ち上がりエッジで熱が拡散し、深刻なHAZが生ずる。
このHAZは、加工箇所周辺で数10ミクロン(μm)から数100ミクロン(μm)の深さまで及び、品質が低下した材料部分は何段階かの後処理が必要になる。後処理には、手作業研磨、研磨液加工、酸エッチングなどを使う。後処理工程は一般に精度低下、コスト増、歩留まり低下を招く。
(もっと読む場合は出典元へ)
出典元
https://ex-press.jp/wp-content/uploads/2014/02/FT1-LFWJ1401.pdf