工業部品検査でのビームプロファイリングの利用
レーザビーム診断ソフトウエアには意外な利用法がある。例えば、マシンビジョンツールとして製造過程で穴のサイズや形状検査に使える。
マシンビジョン検査システムは、イメージングデバイス、一般的にはカメラだが、これとコンピュータや画像処理ソフトウエアを組み合わせたものだ。画像処理では、ピクセルのカウント、対象物の計測、パタン認識、エッジの検出を行う。レーザビームプロファイリングシステムも、同様の技術の組み合わせに依存している、カメラ、コンピュータ、専用ソフトウエアだ。しかし、一連の独自診断機能があり、国際標準化機構(ISO)規格のビームサイズ、形状、直径計測、それにビームプロファイルの2D および3D グラフィック画像が含まれる。
先頃、ある成形デバイスの量産メーカーが1つの課題に直面した。同社は、幅も深さも100μm以下となる穴のサイズと形状を計測する必要があった。マシンビジョンアプローチは、デバイスの両サイドから穴の直径や楕円率を計測する点で効果的であった。しかし、その技術は穴の内部の何らかの障害物とその厚さを検出することができなかった。その結果、穴の多くは「良品」とされたが、後の検査で不合格になった。
限界
穴が真円ではなく直径が正確でなかったら、ビジョンシステムはこうした条件を正確に不合格と判定する。しかし、高速検査工程で穴の内部の障害物は十分に検出されず、マシンビジョンシステムの合否判定率は不適切となり、自動化工程のメリットが台無しになってしまう。
決められた分量の物質が、最終アセンブリ中に穴を通過する必要があった。デバイスは、アセンブリが完了するまで検査はできないので、穴のサイズが正しくないことが見つかったデバイス、あるいは一定量の物質が穴を通らないデバイスはどれでも不合格になり、再加工しなければならず、その結果生産性が落ちる。最終アセンブリに先行して、検査で合格と不合格を区別できれば、大幅なコスト削減になる。
穴は、内部に障害物がない正しいサイズのものでなければならなかった。そのメーカーは、穴の両サイドを100μm 以下で計測できるビジョンインスペクションシステムをテストした。このアプローチは穴の直径を正確に検出することはできたが、成形過程で穴の内部に生ずる障害物を検出することができなかった。
ビームプロファイリングの利用
そのメーカーは、代替アプローチとして、オフィール・スピリコン社のBeam Gageソフトウエアが走る4.4μmピクセルSP620USBカメラをテストした。目標は、正しい穴のサイズが検出でき、穴に障害物質がないかどうかを判定することだった。このテストでは、オフィール・スピリコン社に予め検査して合格となっているデバイスと、不合格と判定されたデバイスとが提供された。
提案されたテストでは、固定された光源を用いた。光源はデバイスの上方2インチの検査される穴を覆う位置にあり、光は穴を通過した後は発散する。カメラはデバイスの真下に設置されており、穴を通過してくる円筒状の光の方を向いている。このコンセプトは、合格サイズの穴からは、光ビームの径は一定で再現性のあるサイズになるという考えに基づいている。大きすぎる穴(これは典型的な不良)では、ビームが広がり、正確な計測をすると不合格として判定される。
このアプローチは、動的テストに近似するものとして提示された。穴を通過する光は、最終組立製品で穴を通過する材料と同じであると見なされる。予め検査して合格となっているデバイスを用いて、中心穴の正しい直径が設定された。これらのディスクは、合格と見なされる数値基準設定に用いられた。これとの比較で不合格デバイスでは、検査により穴の径が大きすぎた。
このセットアップでは、成形部品は表面を下向きに設置し、光が背面から入力するようにした。図1は、固定位置の光源、デバイス、デバイスの真下のカメラを示している。
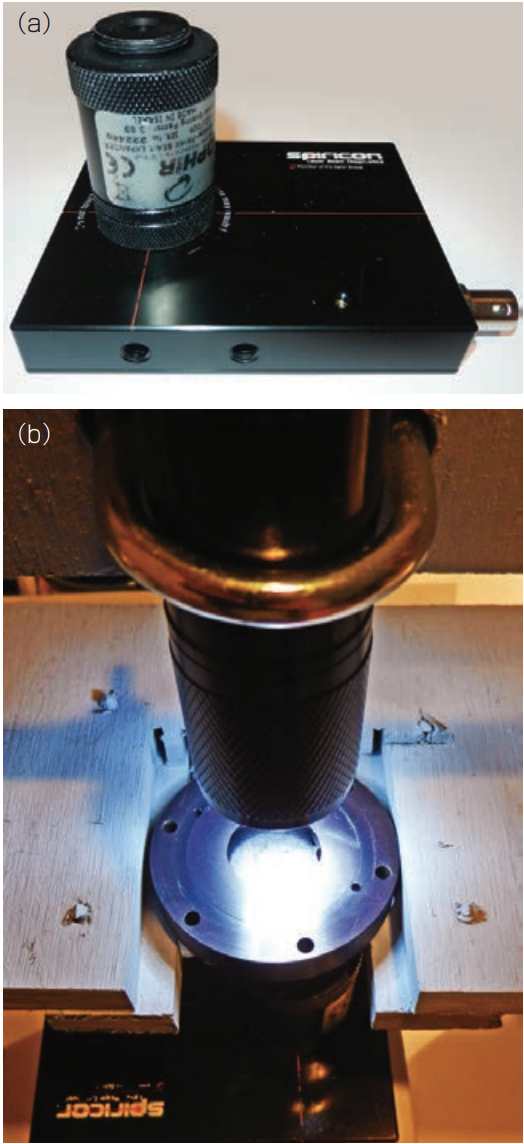
図1 4 倍の拡大レンズを持つUSB カメラ( a )を固定組立部( b )とともに用いて成形デバイスの穴のサイズと形状を計測する。固定組立部には、垂直照明があり、検査されるデバイスを照射する。USBカメラと拡大レンズはデバイスの真下にある。穴の直径と深さは< 100μm(写真は、オフィールフォトニクスグループ提供)
(もっと読む場合は出典元へ)
出典元
https://ex-press.jp/wp-content/uploads/2014/02/0022feature02.pdf