超高速レーザによるCIS薄膜太陽電池の効率の改善
CIS薄膜太陽電池の集積相互接続を形成するためのナノ秒レーザアブレーションや機械的スクライビングによるパターニングプロセスは、熱影響や機械的圧力によって薄膜に損傷が生じるのに対し、ピコ秒レーザ加工は、それらに代替するかなり優れた手法であるといえる。
光起電(PV)モジュールの市場は、年間40% を超えるペースで成長している(1)。成長するソーラーPV 業界の中で、薄膜太陽電池はますますその市場シェアを拡大し続けている。CIS(copper indium diselenide:セレン化銅インジウム)、より具体的にはCu(In, Ga)(S,Se)2薄膜太陽電池は、バルクシリコンウエハに匹敵する光電気変換効率を達成する可能性を秘めており、最大約13% もの効率を実現する製品モジュールが実証されている(2)。
接合分離、レーザドーピング、レーザ切断または溶接など、多くのレーザ処理によって、結晶および薄膜太陽電池が、効率的で信頼性の高い方法で製造できるようになっている。薄膜太陽電池モジュールの全体的な変換効率を向上させるための重要な手法は、モノリシック型シリアル相互接続を集積することによって実現される。この手法では、大きなモジュールを直列に接続されたより小さなセルへと分割することによって、モジュールからの高電圧/低電流出力を実現し、モジュール内の抵抗損を低減する。そしてこのプロセスにおいて、ナノ秒レーザアブレーションや機械的スクライビングを採用する代わりに、よりパルス幅の短いピコ秒レーザを使用する方が、格段に高い性能が得られることが実証されつつある。
シリアル相互接続の形成プロセス
典型的な薄膜太陽電池モジュール(約0.5m×1m)は、約5mmのストリップ幅の個々のセルに分割される。薄膜太陽電池は、金属接合面と透明導電性接合面の間に光吸収層がはさまれた構造になっており、太陽光は透明導電膜を通して吸収層に照射される(図1)。CISに対する基板構成において、金属接合面はガラス基板上に蒸着される。
モノリシック型シリアル相互接続では、薄膜層に3つの機能的ラインパターンを形成する必要がある。最初のパターンはP1(パターン1)と呼ばれるもので、p接合面であるモリブデン(Mo)層のガルバニック絶縁を実現するものである。P2では、Mo層から酸化亜鉛(ZnO)層への接合性を高めるためにMo層上のCIS層を除去する必要がある。このZnO層は、後のプロセス工程において蒸着され、透明なn 接合面として機能する。P3のパターニングプロセスにおいてこのn 接合面を絶縁することで、モノリシック型シリアル相互接続が完成する。
機械的に切削されたP3トレンチはMo層にまで及ぶが、機能的には、導電性のZnO層のみを分離すれば十分である。通常はこのパターンが5mm ごとに繰り返され、電力を得ることができない領域であるデッドエリアがかなり多く生成されることになる。
集積相互接続に一般的に適用される構造形成プロセスは、P1に対するナノ秒レーザアプレーションと、P2およびP3に対する機械的スクライビングのいずれかをベースとする。どちらの手法においても、熱影響と機械的圧力によって薄膜に損傷が生じる。ナノ秒レーザによるP1の形成では主に、約100kHzの繰り返し速度と毎秒数メートルの加工速度が適用される。残念ながら、このプロセスには選択性がないため、通常は何らかの損傷が生じてしまう(4)、(5)。
P2とP3については、処理はさらに複雑である。1つの層を別の薄膜の上に形成する必要があるためである。ナノ秒レーザによる構造形成には必ず、ミクロンの範囲の熱拡散長が伴い、これによってP2とP3に対する選択性が失われる(6)。そのため、製造工程では一般的に、P2とP3に対して機械的スクライビングを採用し、Mo 層の上のCIS層またはCIS/ZnO層を削り取ることによって50〜70μm幅のトレンチを形成する。構造形成されたラインにはムラがあり、安全性を保つために150〜250μm という大きな距離を空ける必要が生じる。さらに、達成可能な加工速度は1m/秒程度に制約され、また、スクライビング用のニードル(針)は寿命に限りがある。
多くの研究機関や企業が、機械的スクライビングに代わる適切なレーザプロセスを見出すための研究に取り組んでいる。独ミュンヘン応用科学大学(MUAS:Munich University of AppliedSciences)のレーザセンターは、オーストリアのハイQレーザ社(HighQ Laser:ニューポート・スペクトラ・フィジックス社[Newport SpectraPhysics]傘下の企業)による超高速レーザ「picoREGEN」を、波長1064nm、パルス持続時間約10ps、最大繰り返し速度950kHz、最大出力30W で使用することによって、3つすべてのパターニング工程を実現することに成功した。独アバンシス社(AVANCIS)のR&Dパイロット製品ラインからの300×300mm2のサンプルに対して、これが適用されている(図2)。
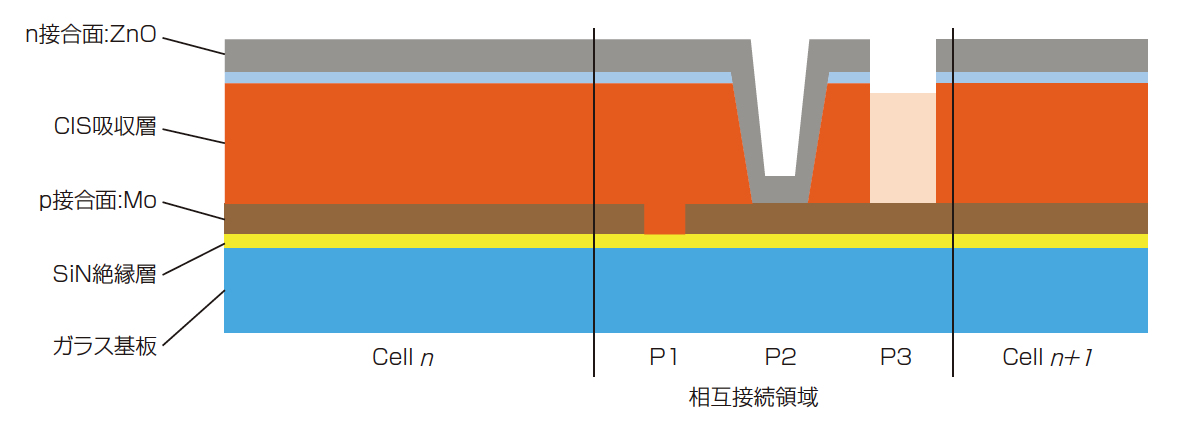
図1 CIS薄膜太陽電池のシリアル相互接続領域の断面を示す模式図。ガラス基板上には、厚さ約1μmのモリブデン層の上に厚さ1〜3μmのCIS吸収層が重なり、1〜2μmの酸化亜鉛層によって覆われている。P1、P2、P3と記された領域は、モノリシック型シリアル接続の構造形成パターンを示す(3)。
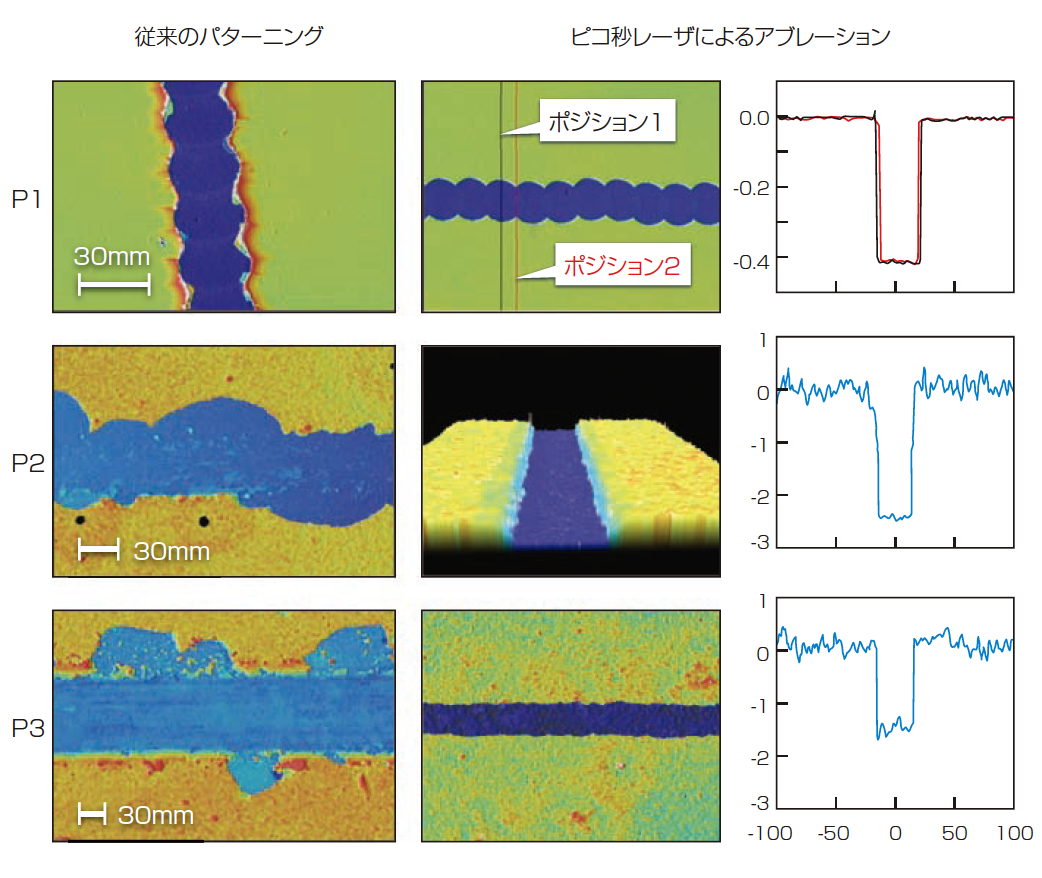
図2 CIS 薄膜におけるモノリシック型シリアル相互接続のパターニング構造を比較した様子を、上からP1、P2、P3ラインの順で示す。左側の共焦点顕微鏡像は、ナノ秒レーザ(P1)と機械的なチップ(針)(P2とP3)によって形成された一般的なラインを示している。右側の共焦点像は、ピコ秒レーザパルスによって形成されたP1、P2、P3のラインである。P1ラインはガラス側から形成されている。レーザラインの幅は通常30μmで、機械切削によるラインと比較して目に見える損傷、チッピング、バリが少ない。機械切削によるラインの幅は50〜70μmで、安全性を保つためにライン間に150〜250μmの距離を空ける必要がある(7)。
P1の加工
Mo層のガルバニック絶縁は、ガラス側から金属層にレーザを照射することによって行われる(図3)。このリフトオフ処理は、直接誘導のレーザアブレーションをベースとしており、レーザのエネルギーを非常に効率的に利用することで、高速な構造形成プロセスを実現している(9)。トレンチは最大950kHzの繰り返し速度で切削される。我々は、最大15m/秒の加工速度を達成した。この上限は、我々が採用したスキャナシステムの速度の制約によるものである。
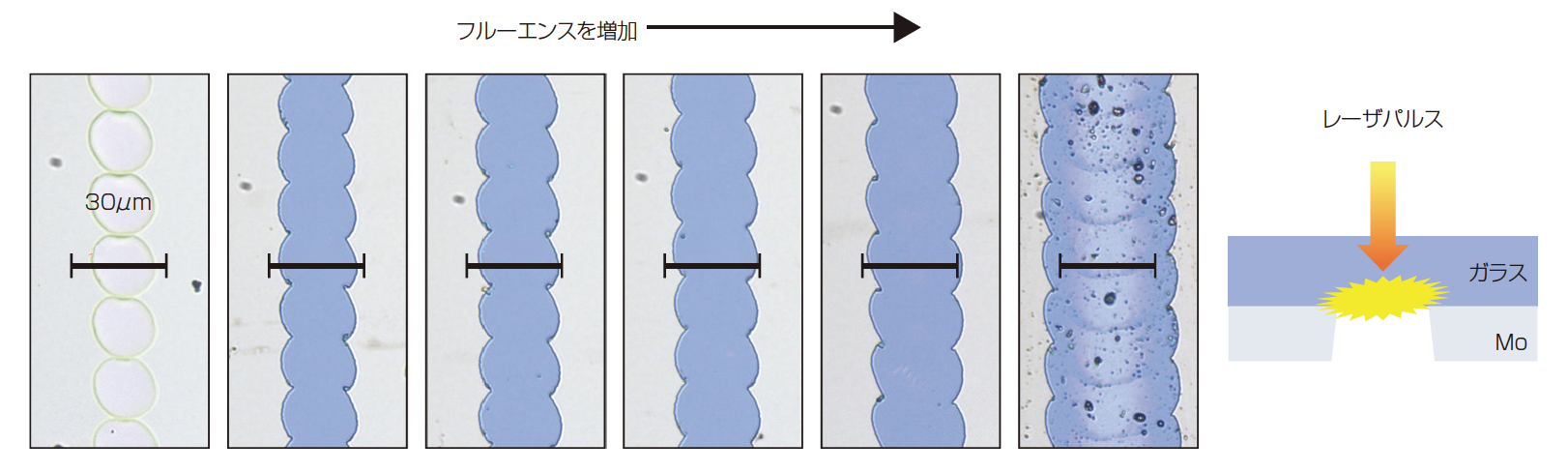
図3 ガラス側から切削したモリブデン層のP1パターン(右側は模式図)。スクライブ速度15m/秒でフルーエンスを増加した様子を示す(前面と背面から光を照射した顕微鏡像)。水色の領域は、切削によってむき出しになったバッファ層である。黒い横線の長さは30μm(8)。
(もっと読む場合は出典元へ)
出典元
https://ex-press.jp/wp-content/uploads/2012/08/201208_0040pa.pdf