スマートフォン製造を可能にするレーザ技術
非接触で高速かつ高精度の加工を実現するレーザは、高密度プリント回路基板、タッチスクリーン、有機発光ダイオード(OLED)パネル製造等に欠かせないツールとなっている。
今日のスマートフォンはコンパクトで頑丈なパッケージの中に高度なタッチスクリーンディスプレイを組み合わせて、膨大な処理能力を実現している。レーザ加工は、これら製品を構成するほぼすべての重要なコンポーネントの製造過程において重要な役割を果たしている。実際、レーザはこれらデバイスで実現されている高機能化、小型化、耐久性に対応するための鍵となる技術になっていると言える。本稿では、スマートフォンや他の先端マイクロ電子デバイスを製造する際に一般的に使用されているより重要なレーザを用いたプロセスのいくつかについて紹介する。
図1は、従来の液晶ディスプレイ(LED)と新しい有機発光ダイオード(OLED)と名付けられた2種類のスマートフォンについて、それらの主要コンポーネントの構成を簡略化し示したものである。いずれのスマートフォンの構造も、背面カバー、プリント基板回路(PCB)、ディスプレイ、タッチスクリーンの4つの要素に分解することができる。言うまでもなく、それらの要素のひとつひとつは、それ自身多数の異なるコンポーネントで構成されている。
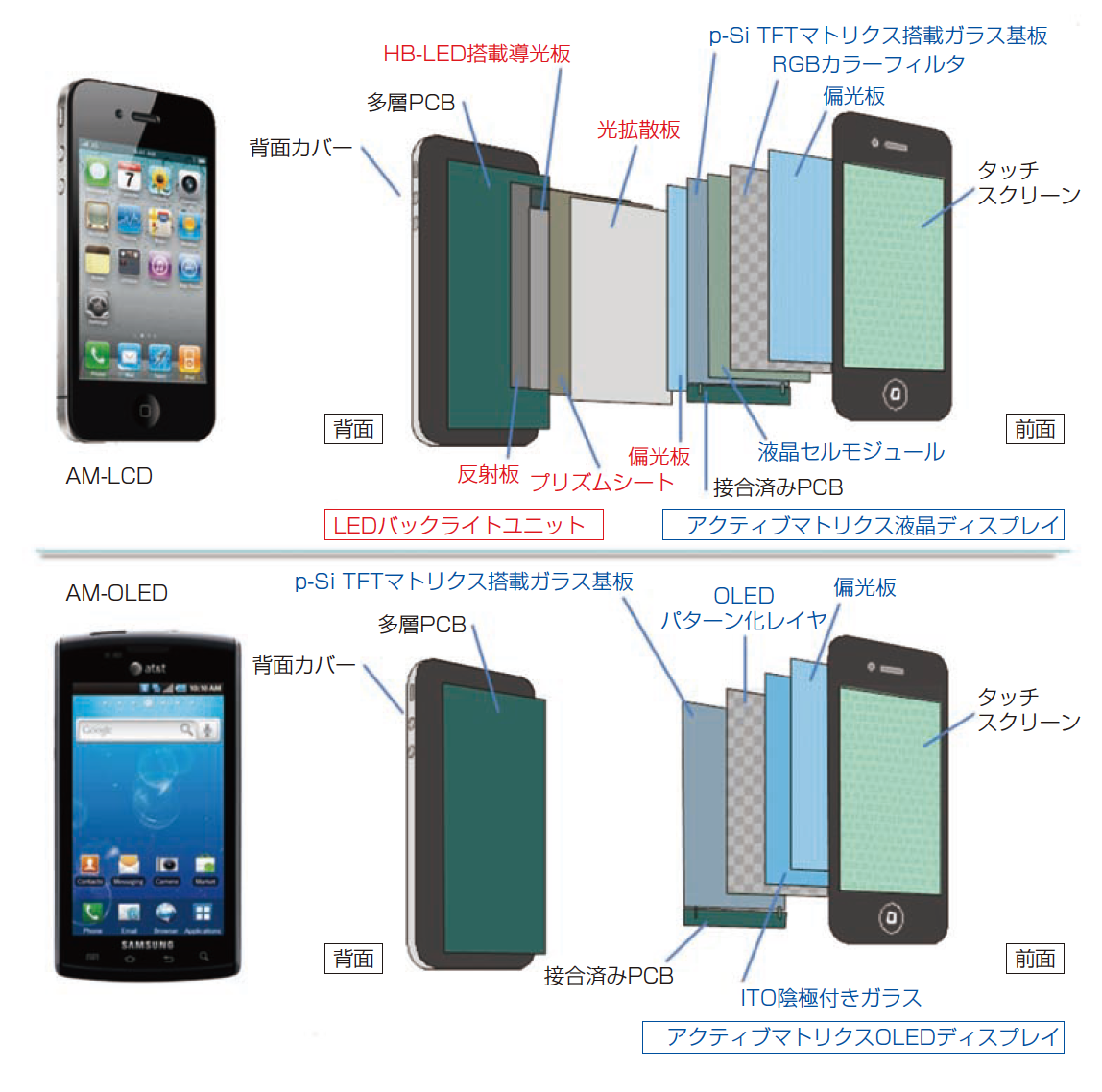
図1 液晶ディスプレイ(LCD)および有機発光ダイオード(OLED)ディスプレイを搭載するスマートフォンの構造。
プリント回路基板の作製
スマートフォンの電子回路には、PCB上に集積される数mm サイズの集積回路(IC)が採用されている。IC間を相互接続するための導電配線が電気的絶縁基板に構成されている。一般的なPCBでは何層もの配線がなされ必要に応じて電気的に接続されている。
スマートフォンでは、機能や処理速度の向上に対応するため駆動装置が複雑化したPCBを求めている。具体的には、より小型のパッケージにより高密度の回路を集積することが求められている。従来の硬質材料の代わりにフレキシブル基板を採用することで、最終的な製品のサイズと形状は自由度を持つことになる。
従来のPCB製造手法では、一連のフォトツールの作成を必要とする。フォトツールとは要求される回路要素の実際のパターンを透明及び不透明領域を持つフィルム状のマスクであり、基板上の層に対して各1枚製作される。これらのマスクは光源として紫外線(UV)ランプを使用してフォトレジストがコーティングされたパネル上にコンタクトプリント(密着印刷)がなされる。露光が施されたパネルは、化学薬品で現像され、銅をメッキすることにより回路配線を形成する。
しかしながら、湿度と温度によってマスクとパネルの材料は伸縮するため、位置あわせを維持することが困難である。このことは、スマートフォンに使用されている高密度相互接続(HDI:High Density Interconnect)基板向けに正確な位置あわせを維持することが難しいことを意味する。
これに代わる手法として、集光したレーザ光を走査しパネル全体に直接パターンを描画するレーザダイレクトイメージング(LDI)がある(図2)。
このアプローチを用いた場合、サイズ、向き、形状を必要に応じてその場で変更することが可能となり、位置精度を維持することが可能である。
LDI における具体的なレーザに求められる要件は、入手可能なフォトレジストの感度に対応する紫外線(UV)出力、高品位のビーム特性、マルチワット(数W以上)の発振出力、24時間週7日間の連続動作に耐えうる信頼性を確保していることである。この用途向けの現時点での先端技術は、LD励起でモードロック発振により第三高調波(355nm)のUV発振を実現するコヒレント社のPaladinである。このレーザでは最大24Wまでの出力モデルが、この用途に貢献してる。特にこれらのレーザ製品に採用されている全固体構造は、耐久性、高信頼性、長寿命を可能にし、更には優れたモード質と位置安定性、出力安定性、低ノイズなどの特性を提供している。

図2 レーザダイレクトイメージング(LDI)では、フォトレジストがコーティングされたパネル上でUV レーザビームを走査することにより、所望の回路パターンを形成する。
高密度プリント基板の孔あけ加工
HDI 回路基板の製作におけるもうひとつの重要な工程は、回路基板の異なる層の間を電気的に接続するためのマイクロビアと呼ばれる小径孔を形成する技術である。レーザドリル(孔形成)は競合する他の技術に比較してはるかに実用的で、コスト上の利点が得られる好適な手法になっている。例えば、孔径が250μm以下になると、機械的なドリル(孔形成)は著しく高価になり、150μm以下になると全く非現実的になってしまう。
スマートフォンのPCB(プリント回路基板)のマイクロビアの孔あけには、100〜500W出力のCO2(炭酸ガス)レーザが最も使用されている。
この用途で傑出した例は、9.4μmの発振波長において225W の出力を有する「DIAMOND K-225i」が挙げられる。一般的にPCB基板材料に使用されているFR4、RCC(樹脂被覆箔)、ポリアミド、PTFE及びアラミド(サーマウント)に対しては、この波長(9.4μm)はCO2レーザでより一般的な発振波長10.6μmより実質的に高い吸収特性を有するため、有効とされている。
しかしながら、回路密度がさらに増加し、孔のサイズが75μm以下になると、この応用ではUV レーザに移行する動きが見られている。高出力のUV光源は、孔の周囲の熱影響部(HAZ: Heat Affected Zone)を最小限に抑えたクリーンで高品位のマイクロビアが提供できる。さらには、UV光は赤外光であるCO2レーザでは困難な樹脂と銅を同時に孔形成できるという利点をもつ。
この用途において典型的なレーザ光源は、Qスイッチの全固体レーザで第三高調波を発振するタイプが用いられる。
コヒレント社のAVIAシリーズでは、現在45Wまでの出力モデルが提供可能である。
高出力と高繰返周波数(>100kHz)発振で優れたビーム質を実現しており、精密なマイクロビアの孔明けが高速で実現されている。
ディスプレイガラスの切断
スマートフォンを軽量化するため製造メーカーはより薄いガラスを使用し始めている。しかしながら、薄いガラスは落下や乱暴な扱いに耐えうるようにしなければならない。さらに、タッチスクリーンでは、ディスプレイのガラス部を日常的に押すことが操作上求められている。
機械的なガラス切断では、基板の厚さが薄くなると適切に処理することが難しくなる。特に微小な亀裂やデブリが形成されたり、エッジに重大な機械的なストレスを残してしまう。
レーザガラス切断は、マイクロクラックやチッピングの問題を排除し、残留応力を生成しないで高いエッジ強度を保つことができる非接触の加工プロセスである。
レーザスクライビングと呼ばれる手法では、CO2レーザ出力は連続的に切断を生じさせるためにガラスの表面に集光される。すべてのガラスは10.6μmに強い吸収を持っているため、レーザの全エネルギーがガラスの表面上またはその周辺に集中し急速に加熱が引き起こされる。液体や空気の噴射によりガラスを急速に冷却することにより、その結果得られる熱衝撃(歪)によって100μmほどの深さのスクライブ溝が形成される。
(もっと読む場合は出典元へ)
出典元
https://ex-press.jp/wp-content/uploads/2012/06/201206_0034feature04.pdf