デジタル画像相関による3次元表面変形の測定
同期させた2台の高速CMOSカメラに解析ソフトウェアを組み合わせることによって、製品設計エンジニアが使用する正確な機械的変形データを生成することができる。
デジタル画像相関(DIC:digital image correlation)は、高解像度のマシンビジョン用デジタルカメラを使用して、2次元または3次元において表面変形を正確に測定する、非接触式の測定手法である。この技術の初期の開発が始まったのは1980 年代半ば、米サウスカロライナ大学(University of South Carolina)の機械工学部においてであった。
1980年代には、デジタルカメラは実質的にはまだ存在しておらず、研究者や博士号を目指す人々の間では、高品質のスキャナを利用して、フィルム写真技術による画像をデジタル画像に変換することが行われ始めていた。このようにして写真から生成されたデジタル画像は、2次元の表面変位を測定するためのマッチングアルゴリズムのテストに使用され、続いて歪みの測定に使用されるようになったが、そのプロセスは非常に時間のかかるものだった。
その後、幅広い分野でハードウェアが進歩し、マシンビジョン用デジタルカメラは解像度、ノイズレベル、収録速度が大幅に改善され、コンピュータのCPU(central processing unit:中央処理装置)はかなり高速で効率的になった。これによって、エンジニアはさらに堅牢で高速なDICアルゴリズムを開発できるようになったとともに、試料作成手法の研究と改良も進められて最大限の空間分解能が実現されることとなった。次の目標は、2台のデジタルカメラを同時に使用して、3次元の表面変形を測定することだった。1998年に、初めての商用のターンキー式2次元および3次元DIC システムが、米コリレーテッド・ソリューションズ社(Correlated Solutions)によって発売された。同社は当時、創設されたばかりの新興企業だった。
基本概念
製品の設計段階においては、最もコスト効率の高い材料を使用して、機能や安全性の要件を損なうことなく、堅牢な設計を考案することが重要である。機械的性質については、3次元CAD(computer aided design)モデルを作成し、有限要素解析(FEA:finite element analysis)を行うことが最初のステップである。これによって理論的に、応力を集中させるべき箇所や、特定の荷重条件下で故障点となり得る箇所を導き出すことができる。
このコンピュータモデルを検証するためには通常、テスト試料上で応力が高いと予測された箇所に実際に歪みゲージを配置し、モデルと同じ位置と方向で力を加え、歪みゲージからの歪みデータを、先ほどのFEA モデルの理論データと比較して解析する。通常は両者のデータは一致しないため、合理的な結果が得られるように、テスト(またはコンピュータモデル)を調整する方法を検討する必要がある。
デジタル画像相関を適用すれば、試料の表面全体にわたる変位と歪みが測定され、歪みゲージを正確に配置する必要がなくなるため、時間のかかるこのプロセスは不要になる。最終的な結果としては、試料表面の全視野にわたる3次元の変位および歪みの測定結果が得られる(図1)。理論的なコンピュータモデルの検証は、材料を効率的に使用して品質の高い製品を設計するための重要なステップである。DICは、より高速により豊富なデータを提供することによってこのプロセスを大幅に高速化する。DIC システムの多くの主要な利点の1 つは、サンプルに対して機械的な操作を加えることなく、全視野にわたる3次元表面歪みを試料の表面積全体に対して測定する点である。これによって、歪みゲージは不要となり、人的時間がかなり短縮される(図2)。
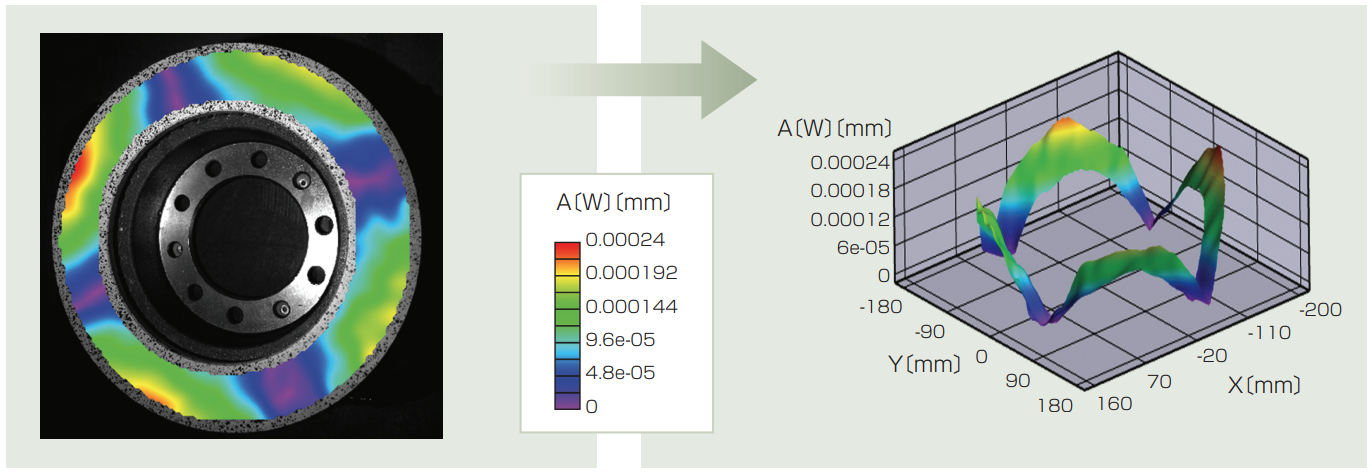
図1 フォトロン社の高速カメラ「SA5」を使用する高速DICシステム「VIC-3D」から取得したブレーキローターの全視野にわたる3次元変形測定 結果(提供:コリレーテッド・ソリューションズ社)。
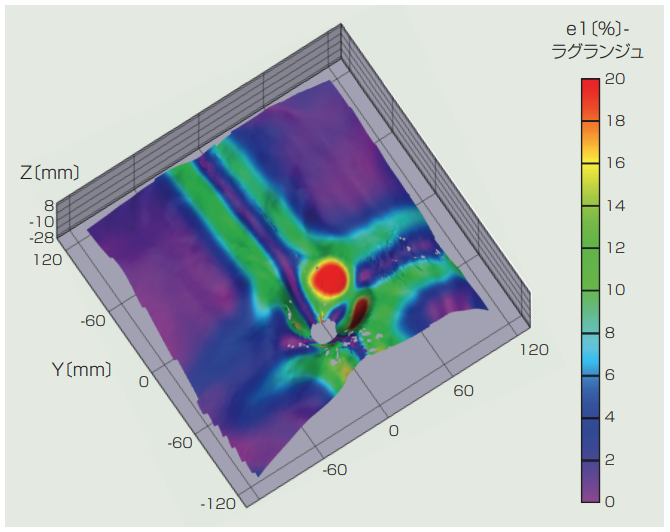
図2 銃弾の衝撃を受けた後のケブラー製ベストの第1原理計算による歪み(e1)を3次元等高線図に示したもの。データは「VIC-3D HS」システムを用いて収集した。VIC-3D HSにはフォトロン社の「Fastcam SA-X」カメラ2台が搭載され、1024 × 1024 ピクセルの解像度で12,500フレーム/秒の速度で画像が集録された。このようなシステムには、カメラ、電子回路、ソフトウェアに加えて、ステレオマウント、LED 照明、レンズ、アクセサリ部品が一般的に搭載される。2台のカメラを正確に同期させることが、3次元DICにおいて非常に重要である(提供:コリレーテッド・ソリューションズ社)。
(もっと読む場合は出典元へ)
出典元
https://ex-press.jp/wp-content/uploads/2012/12/201212_0028feature03.pdf