新たな応用を可能にするピコ秒とフェムト秒の高出力レーザ
適切なエネルギー密度と波長をもつ超高速レーザパルスを材料加工に使用すると、金属の穴あけとウエハ、高分子ステント、ディスプレイ用ガラスなどの切断時の熱影響が最小になる。
レーザの産業応用では20年以上にわたり超高速パルスによるコールドレーザアブレーション、切断および穴あけが構想されてきた。最近の10年間は超高速技術としてのTi:サファイア増幅器による初期実験が行われ、精密加工に対するレーザ超短パルスの大きな可能性が実証された。しかし、精密加工にはどれほどの短いパルスが十分条件になるのだろうか? 超短レーザパルスが材料に命中すると、そこでは何が起こるのだろうか?
原理、時間尺度、エネルギー密度
材料内部におけるレーザパルスの吸収は、レーザパルスから材料内部の電子へのエネルギー移動が基本になる。ナノ秒の継続時間をもつレーザパルスの場合、レーザと格子との間に温度の等化(つまり加熱)が起こり、材料の溶解が始まり、最後はその一部が蒸発する。レーザパルスは短いほど電子へのエネルギー移動が高速になる。理想的なパルスは非常に短いため、電子と格子の温度等化に十分な時間を得ることはない。その結果、「ホットエレクトロン」(コールドラティスに対する)は二つの経路で格子に結合する。特定の時間が過ぎると、電子から周囲の格子への熱拡散が始まる。この電子‐格子緩和時
間は材料に固有であり、一般には 1~10psのレベルになる。ほとんど同じ時間スケールだが、少し遅れて、ホットエレクトロンと格子の間には突然のエネルギー移動が起こり、物質の爆発、つまり励起状態にある体積分の蒸発が起こる。これらの説明からは2つの基本的結論が得られる。
1.レーザパルスは継続時間を十分に短くして、電子と格子との温度等化を防ぐ必要がある。金属やその他の材料の多くは 1~10psまたはそれ以下の短いパルス継続時間が要求される。
2.熱拡散とアブレーションの間には時間遅れがあるため、最短パルスの場合でも残留熱が必然的に発生する。したがって、コールドプロセスは最小の熱拡散が重要となり、0 ~10psまたはそれ以下のパルス継続時間が必要になる。
コールドプロセスにはピコ秒またはフェムト秒のパルス継続時間が必要条件になるが、それだけでは十分条件とはならない。ホットエレクトロンが非常に高いエネルギーに曝されて過熱すると、熱拡散効果が現われ、熱発生のプロセスに変わる。経験則によると、ピコ秒とフェムト秒のパルスによるアブレーションが起こると、測定できない熱影響、つまり熱侵入深さの浅い約1J/cm2のエネルギー密度のスイートスポットが形成される。
線形吸収対非線形吸収
残念なことに自然現象はそれほど簡単ではない。熱影響は上述の要因ばかりでなく、光学的侵入深さ、つまりレーザパルスのどれだけの割合がどの深さで吸収されるかという要因からも決まる。
穏やかなアブレーションの場合は1μm以下の光学的侵入深さが必要になるが、そこには 3つの理由がある。
1. 光学的侵入深さがアブレーションの深さを決める。あまりにも大きい深さは穏やかなアブレーションにはならない。アブレーションが深いと、表面とエッジが粗くなり、硬質材料や脆性材料の場合はマイクロクラックが生じる。
2. 光学的侵入深さが大きいと、レーザパルスの多くは吸収されずに捨てられ、アブレーションは不十分になる。
3. とくに、材料が基板から選択的にアブレーションされる場合(例えば、薄膜太陽電池のような絶縁体上の薄膜のパターニング)、透過した光は基板材を傷つける恐れがある。
フェムト秒およびピコ秒パルスのピークパワーがあまりにも高いため、多光子過程による非線形吸収は線形吸収よりも優勢になるという主張において、パルスの線形吸収の影響はしばしば無視される。パルスの継続時間とエネルギー密度の境界条件が一致する場合、この説明は誤解を招くことになる。このことを明らかにするために、シリコンの深さ方向の吸収曲線を1J/cm2のエネルギー密度に対してプロットした(図1)。パルス継続時間が6psを超えると、線形吸収は非線形吸収よりも完全に支配的になる。この状況は500fsの場合も変わらない。つまり、望ましい1μmスケールの光学的侵入深さまでの非線形吸収はあまりにも少ない。
紫外波長を選択すると、理論的には最高の性能と結果が得られる(例えばシリコンウエハをダイシングする場合)。シリコン加工では緑色波長でも十分な結果が得られるが、赤外波長は点数が悪くなる。
適切なエネルギー密度と波長をもつフェムト秒パルスとピコ秒パルスは、いずれも熱影響を最小にしなければならない材料の加工に適している。また、継続時間がピコ秒のパルスは非常に簡単な方法で発生できる。産業用途の超短パルスはチャープパルス増幅(PCA)をしなくても、直接ダイオードポンピングと増幅(パワースケーリング)から得ることができる。産業用の微細加工の費用対効果を高めるには、50W以上の平均出力への拡大が必要になる。
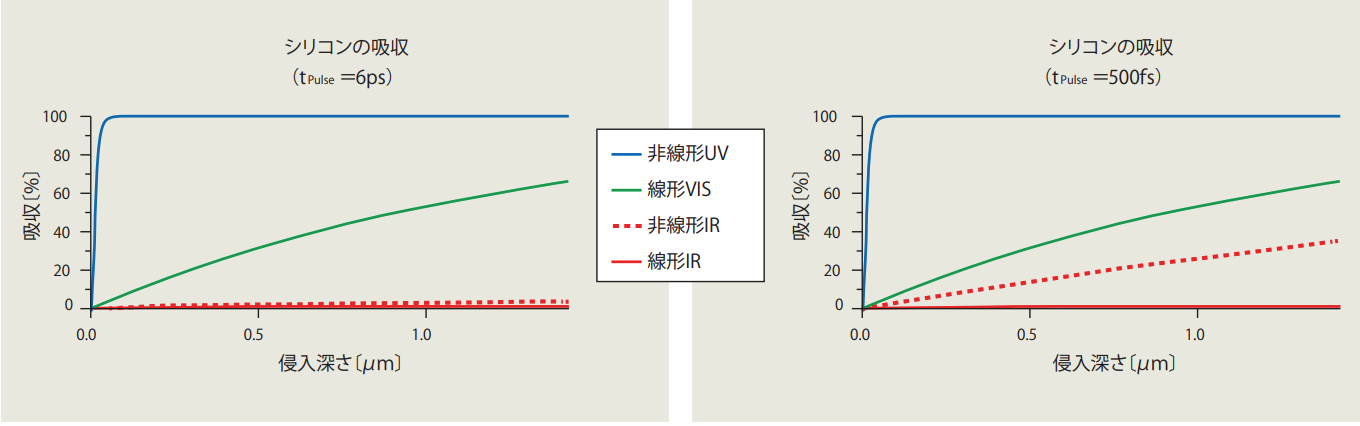
図1 シリコンの吸収曲線を1J/cm2のエネルギー密度に対してプロットしている。6psのパルス継続時間の場合、線形吸収は非線形吸収より支配的になる(左)。500fsであっても、望ましい1μmスケールの光学的侵入深さを実現するには、その非線形吸収はあまりにも低い(右)。
パワースケーリングによる生産性
1970年代からはロッドレーザが使用され、最初は閃光ランプで励起され、その後は半導体レーザによる励起が行われてきた。ロッドレーザは高平均出力のビーム品質限界を拡大できるが、1990年代になると半導体レーザで励起するディスクレーザの技術が開発され、産業用のキロワットCW動作では最も信頼性の高いレーザとして使われるようになった。ファイバレーザとディスクレーザの技術は、伝統的なロッドレーザの技術に比べると、レーザ活性材料の体積に対するレーザ冷却の表面積の比が大きいため、500W以上の出力レベルでのTEM00CW動作が可能になる。しかし、輝度が等しいと、小さなファイバコアはファイバレーザ内部の強度がディスクレーザよりも劇的に高くなる。しかしながら、ピコ秒とフェムト秒のパルスを増幅すると、高い強度が自己位相変調や誘導ラマン散乱などの非線形効果を引き起こすため、超高速ファイバ増幅器では高度なチャープパルス増幅あるいは実現可能パルスエネルギーの6μJ以下に抑えることが必要になる。
(もっと読む場合は出典元へ)
出典元
https://ex-press.jp/wp-content/uploads/2014/05/1112feature04.pdf