プラスチック光学系に挑戦する精密成形ガラス
成形加工とガラス技術の進歩はプラスチック光学系とコスト競争できる成形ガラス光学系の生産を可能にし、その応用範囲を拡げている。
近年、成形プラスチック光学系は精密レンズの大量生産の最適解であると見なされている。プラスチック光学系は研磨ガラス光学系に比べるとコストと性能に利点がある(1)。しかし、プラスチック光学系の参考文献の多くは代替可能なガラスの生産技術、つまり精密ガラス成形(precision glass molding:PGM)を無視している。実際のところ、PGMはプラスチック光学系と同じ利点を確保できるが、ガラスを原材料に使うことの利点も付加される。ガラスレンズはプラスチックレンズに比べると高価になり、非球面、回折素子、実装オプションなどの形状はガラスでは成形できないと誤解されている。そのため、多くの場合、PGMはプラスチック成形に代替できる量産技術としての利点が見過されている。このような誤解は事実と異なり、間違っている。PGMは1970年代の終りごろから存在し、さまざまな用途に対して、コスト効果が確実に得られる技術として使われてきた。ここではPGMにより生産されるガラス光学系とプラスチック光学系とを比較して、前者が正当な代替品であることを明らかにする。
材料特性
光学素子の成形の工程は、プラスチックの射出成形とガラスの圧縮成形のいずれも原材料の選択から始まる(図1)。成形用の代表的な原材料は、その種類はガラスの方がプラスチックよりもはるかに多い。成形可能なガラスの選択肢は100種類を十分に超えるが、光学プラスチックの選択肢は 1桁にとどまる(図2)(2)、(3)。成形可能なガラスは、この広い選択肢に加えて、材料特性に関係する利点も得られる(表1)。成形可能なガラスは比重を除いて、すべての定量的性質が優れた性能を示し、より良い光学的判定基準(屈折率、アッベ数および光透過率)と、その他のより広い判定基準を選択できる。
基本的な射出成形プラスチック光学系、つまり環状ポリオレフィン(COP)、ポリカーボネイト(PC)およびアクリル樹脂(PMMA)の標準の透過率プロフィルは、350から1200nmまでの波長範囲に対して、80%台の上位から90%台の下位までの範囲に収まる。最も成形の容易なガラスの透過率は、同じ波長範囲に対して90%台の上位になる。成形可能なガラスの熱性能は成形可能なプラスチックに比べるとかなり優れ、成形可能なガラスはより高い使用温度を 1桁低い熱膨張係数で得ることができる。成形可能なプラスチックにはPMMAのように、光学的性質に影響を及ぼす水の吸収や複屈折による問題をもつ材料もあり、選択前の評価が必要になる。重量は成形可能なプラスチックがガラスよりも優位にある唯一の大きな利点であり、少なくとも2:1の比率で重量の軽減が可能になる。
定性的性質について述べると、ガラス光学系はプラスチック光学系よりも非常に良好な耐環境性と良好な耐摩耗性が得られる。他方、射出成形プラスチック光学系は別の実装形状や複数の光学面を集積できる基本的な利点をもつが、このことは研磨によるガラスレンズとは違って、PGMで成形したガラスレンズの場合も可能になる。このようなレンズは集積実装フランジをもつ場合が多い。ガラスはレンズアレイ、回折光学面、非円柱外部面などの形状を付加した成形もできる。ガラスはPGMを用いると、プラスチックへの成形品の挿入と同様に、金属ハウジングの直接成形も可能になる。全体として、プラスチック光学系の場合の複雑な形状に比べると、PGMにより可能となるガラスの幾何学形状は限定されるが、複雑な形状に向けてのPGM技術の改善は継続的に行なわれている。
生産者はPGMによるガラス光学系と射出成形によるプラスチック光学系の最終製品を比較するとき、PGMはプラスチック光学系よりも高品質の製品が標準的に得られる技術であると考える場合が多い。このことは前述したように、ガラスの優れた熱安定性、高い光学品質および耐久性にもとづいている。ガラス成形は収縮が少ないので、レンズ間の良好な再現性と性能の優れた一貫性を得ることができる。
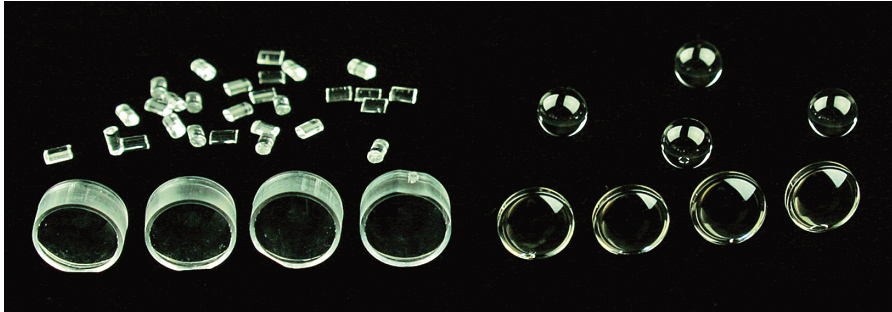
図1 成形光学系はプラスチック(左)またはガラス(右)の原材料を使用する。プラスチック射出成形光学系用の熱硬化性樹脂は押出成形されてペレット状になる。PGM加工は成形前にプリフォームが必要になる。(資料提供:ロバート・カリノフスキー氏)
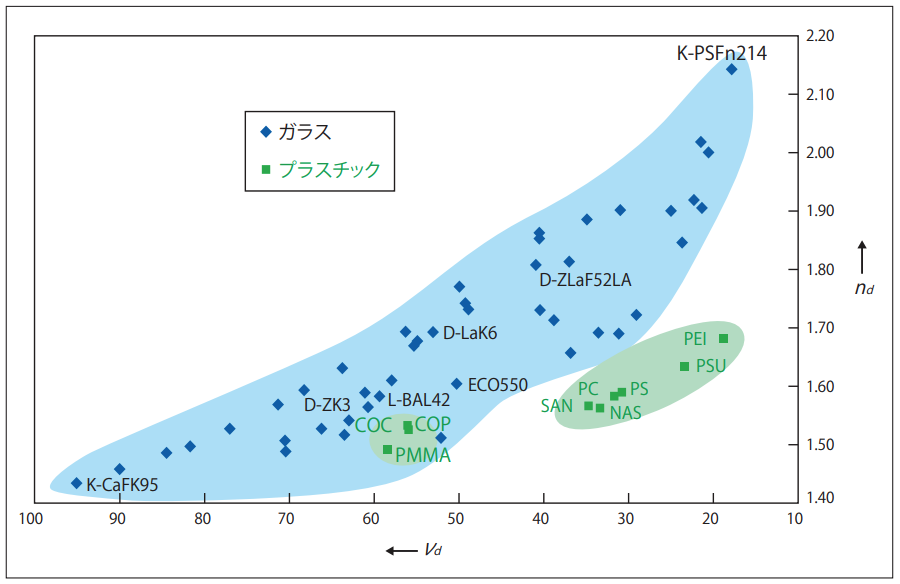
図2 成形可能なガラス材料の代表的な選択肢の屈折率とアッベ数の関係を図示している。ガラスはプラスチックに比べると選択可能な多数の材料がある。これらのガラスのデータは一般の光学ガラスのデータではなく、主要なガラスメーカーから成形用として市販されているガラスのデータであることに注意してほしい。
(もっと読む場合は出典元へ)
出典元
https://ex-press.jp/wp-content/uploads/2011/09/1109feature02.pdf