将来にわたって有効な医療機器製造用レーザシステム
プロセスを支えるハードウエア、プロセスデータ、アナリティクスにより、さらに費用対効果の高いレーザソリューションが実現される。
医療機器製造とレーザ技術には、品質や精密さを含む、多くの点で適合性がある。このことから両者の間には、長年にわたる双方に有益な関係があり、レーザ技術は、医療製品のイノベーションと医療機器業界の成長を可能とし、ベンダーに利益をもたらしている。
システム購入の投資利益率(ReturnOn Investment:ROI)を検討する際には、プロセスの付加価値と生産率が、システムの価格に対して評価される。将来的にはこれが、ユーザーソフトウエア、設定の標準化、生産データ、自動パーツハンドリングを含む形に移行していくと思われる。そのすべてが、生産の付加価値の最大化につながる。
「ユーザーフレンドリー」なインタフェース
ユーザーフレンドリーなGUI(グラフィカルユーザーインタフェース)とは、どのようなものだろうか。あるいは、素晴らしいユーザーエクスペリエンスといったほうが正確かもしれない。基準となる使用事例は、スマートフォンである。年齢や言語にかかわらずほぼすべての人が、スマートフォンを所有して使用することができる。製造現場に置き換えると、作業者に対するトレーニングがほとんどあるいは全く不要で、複数のシステムの間で作業者をローテーションさせることができることを意味する。さまざまなベンダー製の多数のシステムを扱うエンジニアにとっては、別の新たな操作ソフトウエアを学習する必要なく、それらを直ちに使いこなして管理者レベルの機能にアクセスできることを意味する。そして問題が発生した際にも、学習し直す必要はなく、これらの非常に貴重な人材の時間を節約することができる。
ここで鍵を握るのは、GUIという頭字語に含まれる「グラフィカル」という単語である。グラフィックスは、システムの全体図を画面に表示し、対象箇所を直ちに特定して選択することにより、調整可能な各パラメータへと表示を絞り込むことを可能にする。しかし、それよりも重要なのは、パラメータ機能の説明が視覚的に示されることである。図1は、強化されたウォブル機能を搭載するフォーカスヘッドに対する、そのようなインタフェースのスクリーンショットである。まず、システム内のどの部分を交換するかが明確に示されている。次に、各パラメータの説明が示されている。そして最後に、選択した値が調整範囲内のどの辺に位置するかが示されている。大まかな調整も微調整もタッチスクリーン上で行われ、タッチスクリーンは、システムに固定するか、取り外し可能なタブレットとすることができる。
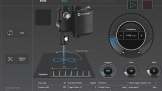
図1 交換する備品が図示され、具体的にどのパラメータが変更されるのかを理解することができる。
システム設定の標準化
ポイントオブユース(POU)の単一パーツであるか、多数の異なるパーツからなるフレキシブルセルであるかにかかわらず、どのようなシステムであっても、シフトや作業の開始時に、機器が正しく設定されていることの確認に費やす時間は、積み重なれば膨大な量になる。誤った設定処理が行われている場合は、さらに多くの時間がかかってしまう。レーザ加工の場合、最も時間がかかるのは、焦点位置の設定である。焦点位置を確認して、最適な位置を維持しなければならない。試験片に対する定性的な試験に頼るよりも、カメラでビームプロファイルを撮影して正確な焦点位置を取得する定量的な方法のほうが、1回で完了し、非常に正確である。図2は、測定システムと、得られたビームプロファイルから焦点位置を特定する様子を示したものである。
フレキシブルセルの場合、特に溶接用のものは、さまざまなパーツのスポット径を変更することが日常的に行われる。必要となる最小のスポット径に対応する光学系を購入し、デフォーカスによってスポット径を大きくするというのが、これに対する簡単な対処法である。この方法の問題は、図2 のビーム断面からわかるように、焦点位置からずれると、焦点深度(Z 許容範囲)がゼロになることである。プログラマブルなエクスパンダー/コリメーターを使用することにより、適切な分解能で、最小スポット径の約2 〜3 倍の範囲でスポット径を調整し、同じZ位置で焦点位置を維持することができる。ここでも定量的なデバイスによって、集光スポット径を正確に制御し、確認し、プログラムすることができる。
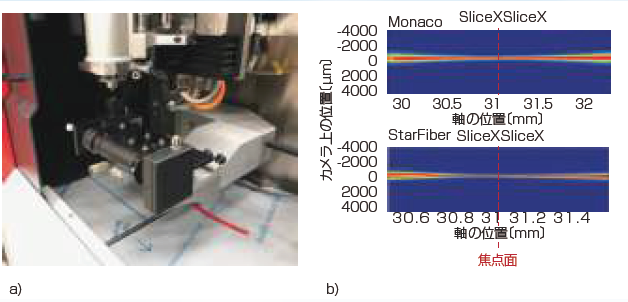
図2 (a)設定標準化ツールにより、正確な焦点位置が確立される。(b)定量化可能な他のビーム特性としては、焦点におけるビームの丸みや、集光スポット径がある。
生産データ
最近では、生産データの生成と解釈が「インダストリー4.0」という概念の下でとらえられている。インダストリー4.0とは、ドイツのハイテク戦略組織によって10年近く前に生み出された造語で、安価なコンピューティング能力を活用して、機械学習に基づく最適な製造を実現することを目指すものである。インダストリー4.0の実装に向けた取り組みはまだ、試行錯誤が続く状態にあるが、進歩は得られており、その最初のステップがデータ収集である。
レーザ、ビームデリバリ、集光光学系、ステージ、工具、ガスデリバリなど、システムの多くの部分をすべて監視することができる。最初のレベルは、はい/いいえで回答する、プロセス開始時の確認作業である。例えば、シールドガスはあるか、工具にパーツが正しく配置されているか、などの質問に回答していく。時間の経過とともにこのデータを、レーザ出力やカバースライドの清浄度(汚れの付き具合)など、システムの対応する部分の動作範囲の設定や、例えば3 つのパラメータが動作ウィンドウの範囲内にあるが、総合するとプロセスが仕様の範囲外になるといった、積み重ねロジックの設定に使用することができるようになる。これを手作業や、扱いにくい統計的制御ソフトウエアで行うのは難しいため、機械学習を適用すれば、このプロセスを加速化し、同じデータセットからより多くの洞察を導き出すことができる。障害予測、計画的なダウンタイム、保守スケジュールを自律的に設定するシステムのすべてが、実現可能である。しかしこれは、全体像の半分にしかすぎない。残り半分は、実際のプロセスそのものの測定である。
(もっと読む場合は出典元PDFへ)
出典元
http://ex-press.jp/wp-content/uploads/2021/10/028-030_tr_future-proofing.pdf