ナノ秒パルスファイバレーザの強みを生かしたレーザエングレービング
品質と生産性を高めるためにパルス特性を最適化する技術
レーザエングレービングは、マーキングと一括りにされることの多い用途の1つだが、実際には全く異なる。エングレービングは、材料を物理的に除去して、加工対象基板に改変された形状を作成する処理であるというのが、最も適切な定義である。
エングレービングの応用分野は非常に多岐にわたり、鋼鉄から石材に至るまで、日常生活のさまざまな側面に関連している。次に自動車に乗るときには、ダッシュボードや内装トリムに手を滑らせてみてほしい。そのレザーレットの手触りは、動物の皮とはまったく異なるはずだ。それは、デジタル処理によって作成され、それらのプラスチック部品の製造に使われるスチール金型に複雑に彫り込まれている。その処理には通常、ナノ秒パルスファイバレーザが用いられる。硬貨や金属金型の製造もレーザエングレービングの領域で、宝石業界では、貴金属のレーザ加工がますます広く採用されている。職人がパンチやハンマーを使って商品に刻印を入れるというイメージがあるかもしれないが、今ではそれはまれなケースで、そうした処理はすべて、レーザによって行われている。
超高速レーザや連続波(ContinuousWave:CW)レーザでさえも、他の種類のレーザをエングレービングに使用できる用途も存在するが、大多数の用途で使われているのは、ナノ秒パルスファイバレーザである。その短いパルス幅と高いピーク出力が、この用途に非常に適している。実際、ユーザーがパルス幅を選択可能で、最大4MHzの繰り返し周波数を備える主発振器出力増幅器(Master Oscillator Power Amplifier:MOPA)は、品質と生産性を高めるためにパルス特性を最適化する手段をユーザーに提供するため、この用途に最適である。英SPIレーザーズ社(現トルンプ社傘下)の「PulseTune」技術はその一例で、3ns〜2μsという3ケタにわたる範囲でパルス幅を制御することができる。
品質の達成
そのプロセスは、原理的には比較的単純明快である。レーザ光の入射パルスによって基板の一部が溶融し、溶融プールが生成される。続いて、表面の一部が蒸発して、溶融部分に反跳圧がかかり、溶融射出が生じる。これが、材料除去の主なメカニズムである。ここで、パルスエネルギーが高いほど多くの材料が除去され、ピーク出力が高くパルス幅が短いほど品質は高くなるという、よくある誤解を否定しておきたいと思う。このプロセスは非常に複雑で、効果的に適用できる厳格な規則は存在しない。パルス特性、光学配置、処理/走査パラメータの間には、微妙なバランスがあり、エンドユーザーの要件に基づいて最適化する必要がある。エンドユーザーの要件は、品質か除去率かだが、両者は互いに相反するためである。
エングレービングは、レイヤベースの材料除去処理であり、1回のパスで除去される材料は、わずか数十ミクロンである。この除去処理は比較的低速で、除去率は、立方ミリメートル毎分(mm3/分)の単位で表され、利用できる平均出力によって左右される。高い表面品質と高い除去率の両方を達成するためのカギとなるのは、採用する加工手法である。基本的なラスター走査では、溝が形成される可能性があるため、一般的に不適切である。その浅さと粗さが許容できる場合以外は、使用しないほうがよい。レーザウォブリングは、ラインや単純なテキストのエングレービングのみが必要という場合に、適用可能である。この手法は、車両識別番号( Vehicle Identification Number:VIN)マーキングなどの用途に、非常に適している。VINマーキングでは、塗装後もマークが見えるように、また、セキュリティの観点からも、マークを削り取ることを難しくするために、かなりの深さが必要である。このような種類の用途では、レーザ源の多用途性が非常に役に立つ。パラメータの簡単な変更によって、パルス幅を短くして、パルス周波数を上げることにより、同じレーザを使用して、エングレービング処理による酸化物と表面スパッタを、効果的に除去することができる(図1)。
しかし、より広い面積やより複雑な形状に対しては、レイヤベースの方向的な手法を適用して、方向的な処理の効果を平均化またはランダム化する必要がある。後続のパスを数度ずつインクリメントさせるだけの処理により、結果は確実に向上する。干渉縞(モアレ)の最小化に基づく一連の固定角度を使用することが、最良のソリューションである。これは、印刷業界において均質で一貫した印刷品質を得るために、長年にわたって広く使用されている手法で、レーザエングレービングにおいて卓越した効果を発揮することが示されている(図2)。
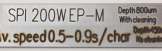
図1 200Wの「EP-M」レーザによるVINマーキングの例。

図2 (a) は、アンチモワレ(干渉縞防止)用のハッチング角度。(b) は、それらによるエングレービング例。
カギはパルスにあり
上述のとおり、プロセスの最適化は、時間はかかるがそれだけの価値がある作業であり、除去率が2倍になるか、粗さが半減する場合もある。パルスパラメータだけでなく、パルス間(P-P)のオーバーラップやライン間(L-L)の間隔という幾何学的なパラメータも検討する必要がある。選択したパラメータの相互依存性を示す材料見本を使用することにより、この最適化の大部分を構造化及び半自動化することができる。例えば、真ちゅうのエングレービングにおいて、平均出力を一定にしてパルス幅とパルス周波数を変化させると(P-PとL-Lは固定)、パルスエネルギーが最大(ピーク出力が最大でパルス幅が最短)のときに、材料の除去率が非常に低いことがわかる。材料見本からは、繰り返し周波数を上げることによってパルスエネルギーとピーク出力の両方を下げる場合と、パルス幅を長くする場合に、材料除去率が大幅に向上し、最大で40%向上する場合もあることがわかる。もう1つ興味深いのは、同じ試験を異なる材料に対して行うと、結果は異なるということである。それは、意外なことではないかもしれない。導電率、熱容量、融点、流体粘性など、主要な材料属性は多数存在するが、そのすべてが材料によって大きく異なり、プロセスに関係するためである。従って、アルミニウムと鋼鉄では、最適なパラメータは全く異なるため、試行錯誤による調整が必要である(図3)。
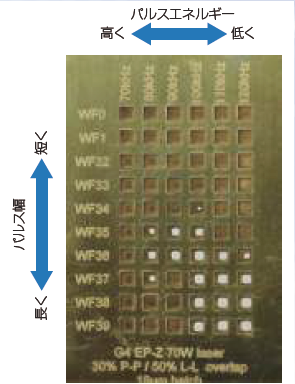
図3 パルスパラメータの効果を示す、真ちゅうのエングレービング見本。
(もっと読む場合は出典元PDFへ)
出典元
http://ex-press.jp/wp-content/uploads/2021/10/020-022_ar_laser_engravng.pdf