アルミニウムや銅のレーザ溶接最適化テクニック
スパッタレスの新常識 モード可変技術ARM。
はじめに
E-モビリティというワードは、日々のニュースで頻繁に流れ、世界中で成長産業分野の一つとされているのは周知のとおりだ。低炭素社会を目指して既存自動車メーカや新興電気自動車メーカなどでは、電動化技術に向けて多くの技術やプロセスが検討されている。100年に一度の大変革時代といわれる自動車業界では、電動化技術に携わるサプライチェーンで競争が激化しており、コストパフォーマンスに優れ、高品質の製品や技術を安定的に供給できるサプライヤが世界中で必要とされている。加速度的に需要と供給が膨らむこの分野にて、発展的な技術や革新的なプロセスが求められており、レーザ溶接技術もその一つである。生産性向上、性能差別化、軽量化とコスト低減を目的としてレーザ溶接適用が増加するものと見込まれ、それらの対象物はアルミニウム合金、ダイキャスト材、銅や鋼などの多様な材料となる。アルミニウム溶接においては、合金のタイプによっては溶接割れが発生しやすく、溶接部の強度や品質の欠陥となる。銅材料においては、基本波である1μm帯波長の吸収率が固体状態ではとても低いため、安定した溶接が難しいとされてきた。各メーカから多様なソリューションが提案されているが、本稿では先進的なレーザ溶接技術の新常識であるモード可変技術(ARM技術)を搭載したARMファイバレーザの応用例を紹介する。
モード可変技術ARM
1μm 帯波長のファイバレーザは、その高い発振効率と優れたメンテナンス性によるコストメリットや、発振器の低価格化による装置導入のハードルが下がったこともあり、レーザ溶接における主流となっている。ただ、ファイバレーザはその優れたビーム品質により、溶接時のスパッタが問題となることがこれまでに多々あった。そこで、ビーム品質つまりはエネルギー分布を最適化するモード可変型ファイバレーザが生まれた。コヒレント社では、2018年よりARM(Adjustable RingMode)ファイバレーザとして市場投入した。伝送ファイバが円形コアとその同心円にリング状コアをもつ2 層構造を持つ(図1)。各コアにファイバレーザモジュールを接続するというコヒレント社製品の構造は、センタービームとリングビームの出力と変調を個別に制御可能とし、レーザ出力の配分を定格出力の1%から100%までを数十マイクロ秒毎に高精度高速制御することができる。材料、板厚、継手形状など多種多様な条件に合わせてエネルギー分布を最適化し、キーホール溶接や熱伝導溶接を使い分け、材料への入熱を自由かつ瞬時に電気制御できる。一般的に高速かつ深い溶け込みを得る溶接をするには、高エネルギー密度のレーザが用いられる。その高エネルギー密度により溶接対象物にキーホールが形成され、溶融金属の対流や金属蒸気の突沸などによりキーホール後端からスパッタが発生する。そこでARM ファイバレーザを用いることで、センタービームの高エネルギー密度に加え、その周囲のリングビームが予熱・後熱効果をもたらし加工品質を改善する。結果として、高速での溶接を可能にしながら、リングビームが溶融池の対流を安定させ、キーホールの開口を促すことで金属蒸気の排出を促すことができ、スパッタを低減させた高品位な溶接が可能となっている。また、搭載されるファイバレーザモジュールはアンプ構造を持たないシングルオシレータであり、クローズドループの出力モニタによって加工点でのレーザ出力を安定させ、反射光に対して堅牢なデザインである。ファイバコネクタやビームコンバイナーなど各モジュールに配備された反射光除去機能とセンサにより、銅などの高反射材料に対しても面直照射することで加工効率の向上に貢献している。
電動化技術とその加工要求に応えるサブシステムを市場に投入すべく、ARMファイバレーザとツーシックス社の高機能スキャナー溶接ヘッドを組み合わせることで、研究開発での多様性とプロセス最適化を可能にし、ユーザのニーズに合致した製造システムを提案できる。販売・サービスを一元的に対応できる体制を整えたことで、製造現場での強力なツールとなっている。そのツールを用いて難加工材料とされているアルミニウムや銅を溶接したテクニックを紹介する。
アルミニウム溶接における入熱量制御
アルミニウム合金材料は、自動車ボディ、リチウムイオン二次電池の筐体ケース、バッテリートレイ、バスバーなど適用部位が多岐に渡る。融点が約660℃と低く、溶接部が溶け落ちやすく熱伝導率も良いため、溶接部と母材の温度差勾配などを起因とする溶接割れが起こる。一般的なファイバレーザでは、熱影響層(HAZ)の制御が難しく、割れの感受性を低くさせるフィラーワイヤを供給したり、レーザ光を振幅走査(ウォブリング)したりする必要があった。そこで、ランニングコスト増も懸念となるフィラーワイヤや煩雑なウォブリングも無く、溶接割れを回避するのにARMファイバレーザでのモード可変による入熱量制御が効果的となる。センタービームは高輝度エネルギーにより溶け込み深さに寄与し、リングビーム先端による予熱効果と後端による後熱効果が加工対象物の急熱・急冷による溶接割れを回避することが分かっている。アルミニウム合金5000系と6000系の車体部品溶接や、今後需要が増えると予想されるバッテリートレイ向けのアルミ押出材の溶接への応用実績もある。溶接に気密性が求められるトレイに関しては、既存プロセスであった摩擦攪拌溶接(FSW)と比較して、レーザ溶接は6倍以上の加工速度を達成できている。また、十分な高エネルギー密度をセンタービームに持つことで、融点の高い酸化被膜を残留させることなく溶接し、溶接凝固時に残留物の応力が起因となる溶接ビード内部で発生する微小クラックに対しても効果が得られている。例えば、二次電池は充放電を繰り返すことによって、溶接部に物理的なストレスが負荷されるため、溶接時に微小なクラックでも発生していると、ストレス負荷がそれを拡大させ電池の故障原因となる。また、先述したように、アルミニウムは溶接中に溶け落ちやすい材料であるため、溶接が貫通してしまうと電池内部を損傷してしまうため、モード可変ファイバレーザによる溶け込み深さの制御が有効的である。加えて、リングビームにより熱伝導溶接を施し、一定のビード幅を持った溶接を形成し、安定した密封溶接を可能とする。スキャナーを用いて毎秒300mm以上の高速溶接によって生産性向上が図られるなか、更に高品質な溶接を実現できる応用例を挙げる。熱伝導性の高いアルミニウムの場合、角型電池ケースを例にとると、その長辺、短辺及びコーナー部といった熱の蓄積度合いが異なる部位において溶接条件を変える必要が出てくる。高速溶接であることは、オンザフライで溶接条件の変更を高速できなければならない。センタービームとリングビームがそれぞれ独立したモジュールで構成しているARMファイバレーザの強みが大いに発揮されるところである。更にリチウムイオン二次電池の製造プロセスでの応用例として、封かん溶接、バスバー溶接または電池搭載部品の溶接において、溶接点の近傍に熱影響の受けやすい樹脂部品などが搭載されていることがある。その場合、熱影響層を最小限に抑えることを求められるが、一方で強度の高い溶接をするために、ある条件以上のビード幅や溶け込み深さを求められる。それらは一般的にはトレードオフの関係であるが、ARMファイバレーザによって、高エネルギー密度によるキーホール溶接型とリングビームの熱伝導溶接型のハイブリッドを施すことで、バランスの取れた入熱制御が出来る。あるケースでは、加工近傍観測点にて許容上限温度の80%未満まで温度上昇を抑えつつ、ビード幅及び溶け込み深さともにターゲット数値の10%以上を達成することができた。
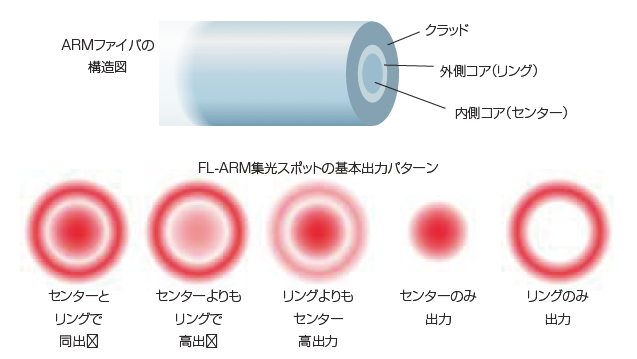
図1 ARMファイバレーザの概念図。
(もっと読む場合は出典元PDFへ)
出典元
http://ex-press.jp/wp-content/uploads/2021/10/016-019_tr_Coherent.pdf