自動車製造、CO2レーザを選択
CO2 レーザで加工された部品が、標準的な自動車のほぼすべての領域で使われている。
現代の自動車製造には、プラスチック、金属、布地、ガラス、ゴムなど、幅広い種類の材料が用いられる。ハイエンドの高級自動車には、木材やレザーといった従来の材料とともに、最先端のカーボンファイバが使用されている場合がある。このような多岐にわたる材料を加工するには、多用途に対応する工具が必要だ。そこで登場するのが炭酸ガス(CO2)レーザである。1964年に発明されたCO2レーザは、最も古いレーザ技術の1つだが、今でも現代製造になくてはならない存在であり、自動車業界において多くの用途に用いられている。
CO2レーザは、出力が数十WのものからkWレベルのものまで提供されており、多種多様な加工に有効である。低い出力レベルは、主にマーキングやエングレービングに利用され、出力を上げれば、切断や溶接を簡単かつ正確に行うことができる。そのため、レーザ加工部品は、標準車両の内装と外装の両方において、ほぼすべての領域で使用されている(図1)。
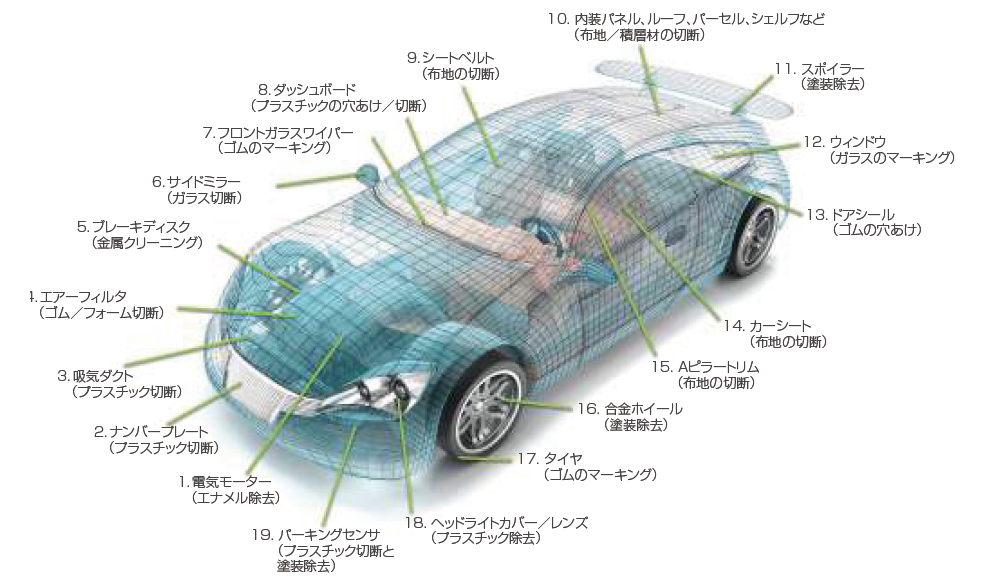
図1 ルクシナー社のCO2レーザが適用可能な、19の車載用途。
プラスチックの切断
CO2レーザは、プラスチック部品の加工に広く用いられている。これには、内装やダッシュボードパネル、ピラー、バンパー、スポイラー、トリム、ナンバープレート、照明カバーなどが含まれる。プラスチックの種類も幅広く、アクリロニトリル・ブタジエン・スチレン(ABS)樹脂、熱可塑性ポリオレフィン(TPO)、ポリプロピレン、ポリカーボネート、高密度ポリエチレン(HDPE)、アクリルなどに加えて、さまざまな複合材や積層材が用いられている。プラスチックは、そのままの場合もあれば塗装されている場合もあり、他の材料と組み合わされる場合もある。例えば、布地で覆われた内装ピラー、複合材でできていたり化粧板が張られていたりするトリムパネル、カーボンファイバやガラスファイバを充填して補強した支持構造などである。
レーザは、固定点、照明、スイッチ、パーキングセンサなどの部品の切断または穴あけや、射出成形処理で残った余分なプラスチックの除去やトリミングに使用できる。透明なプラスチックでできたヘッドライトカバーやレンズは、成形後に残った余分なプラスチックを除去するために、レーザによるトリミングが必要になる場合が多い。照明部品は通常、ポリカーボネートでできている。光学的透明度が高く、耐衝撃性と耐破砕性に優れ、天候や紫外線に対する耐性が高いために、この材料が選択される。ポリカーボネートをレーザで加工すると、仕上がりは粗くなるが、ヘッドライトを完全に組み立ててしまえば、レーザで切断されたエッジは見えない。それ以外の多くのプラスチックは、高品質な仕上がりで切断可能で、後処理のクリーニングやさらなる修正が不要な、滑らかなエッジが得られる。
プラスチック切断は一般的に、作業完了までの時間に応じて、125W以上のレーザ出力で行われる。英ルクシナー社(Luxinar)の「SR」「SCX」「OEM」シリーズはすべて、これらの用途に適している。ほとんどのプラスチックに対し、レーザ出力と加工速度は線形の関係にあり、レーザ出力を2倍にすれば切断速度を2倍にすることができる。適切なレーザ出力を選択できるように、一連の処理に対する合計サイクル時間を評価する際には、手作業の時間も考慮に入れる必要がある。当然ながら、手作業に対する要件は複雑となる場合があり、レーザビームまたは部品を3次元に動かしながら切断作業を行わなければならない場合も多い。そこで真価を発揮するのが、ロボット技術である。
ロボット
現代の自動車製造はかなり自動化されており、業界全体で長年にわたってロボットが当たり前のように導入されている。レーザは現在、ロボット技術と併用する形で使用されており、従来の工具に代わって、多数の新しいメリットを製造工程にもたらしている。
ロボットとレーザの統合には、固有の一連の課題が存在する。レーザは、次の3つの方法でロボット装置に組み込むことができる。
1. レーザをロボットアームに直接搭載し、洗練された連結式のビームデリバリによって、ビームを加工物に供給する。ロボットは、ビームの集光を常に維持しつつ、比較的複雑な形状を切断するように、プログラムされる(図2)。
![図2 自動車製造用にロボットを組み込んだルクシナー社のSRレーザ。(写真提供:独ロボットテクノロジー社[Robot Technology GmbH])](https://optipedia.info/wp-content/uploads/20_105fig2.jpg)
図2 自動車製造用にロボットを組み込んだルクシナー社のSRレーザ。(写真提供:独ロボットテクノロジー社[Robot Technology GmbH])
(もっと読む場合は出典元PDFへ)
出典元
http://ex-press.jp/wp-content/uploads/2021/08/024-027_ar_automotive_manufacturing.pdf