先進的なレーザビーム制御による異種金属溶接
自動車やエレクトロニクス分野の製造要件に応える技術。
銅とアルミニウムや銅とステンレス鋼といった異種金属のレーザ溶接には、常に課題が伴う。しかし、特にeモビリティやエレクトロニクスの分野において、そのような溶接に対するニーズは高まっている。その典型的な例が、銅製のバスバーをステンレス鋼またはアルミニウム製のバッテリー部品にレーザ溶接する処理である。本稿では、米コヒレント社(Coherent)のSmartWeld+技術に基づく取り組みを紹介する。この技術は、自動車やエレクトロニクス製造の要件を満たす、高い品質とスループットレートで、そのようなレーザ溶接を行う能力が実証されている。
異材溶接の課題
eモビリティ分野のバスバー溶接には、複数の必須要件が存在する。まず、レーザ溶接部は、優れた導電性と熱伝導性を有する必要がある。これらの特性(特に導電性)が低いと、航続距離が短くなったり、必要な充電頻度が増えたり、所有者のランニングコストが高くなったりといった、望ましくない結果につながる。また、バスバー溶接部は高い機械的強度を備える必要がある。車載部品は継続的に振動にさらされ、時に衝撃を受ける場合もあるためである。
同一材料または類似材料をレーザ溶接する場合は、溶接シームには真の金属結合が形成される。つまり、溶融領域の組成や、理想的な場合は、機械的性質(引張強度や延性など)が基材と同一になる。異種材料によって、望ましい性質を持つ安定した合金が形成される場合もある。例えば、銅と亜鉛が結合すると黄銅が形成される。しかし、それ以外の多くの材料は、結合して金属的に安定した合金や許容できる性質を備えた合金を形成することはない。
使用する金属の間に真の金属結合が形成されない場合、1つの解決策は、機械的な「エンタングルメント」(もつれあい)を生成することである。つまり、異種合金を空間的に混合し、接合部に十分な機械的強度を持たせる形でそれらを物理的につなぎ合わせる。ねじれた「突出部」の列を材料の中に生成して、それらを互いに貫通させることによって接合部をつなぎ合わせる、と考えることができる。
このような機械的結合を実現するための1つの方法は、2つのパーツを物理的に圧着させ、一連のレーザパルスによって、局所的かつ空間的に定義された方法で溶融することである。しかし、この方法では溶融池の挙動がまったく制御されないため、満足のいく表面品質は得られない場合が多い。良好な機械的結合を得るには、このパルス照射をかなりの回数繰り返さなければならない。そのため、この処理はあまり一貫性が高いとは言えない。基本的に、レーザ溶接でなくても超音波接合によって、同じ結果を達成することができる。
従来のはんだ付けは、eモビリティ分野においては特に不都合である。はんだ接合部は融点が低く、機械的強度と安定性に欠けるためである。また、はんだには鉛が含まれている場合が多く、環境上の懸念がある。
レーザビーム制御
多くのファイバレーザ溶接は、大きめのマルチモードの集光レーザスポットで行われる。生成された溶接シームが細すぎるために、機械的強度が不十分になるといった問題が生じないようにするためだ。しかし、マルチモードのレーザスポットであっても、パーツ間の物理的なすき間(ギャップ)は比較的小さくする必要があり、そのためには、パーツのエッジ処理とフィットアップを適切に行うことが、メーカーに求められる。このような要件は、製造コストの増加につながる。
ビームウォブルは、(所望の溶接シームに沿ってビームを単に直線的に動かすのではなく)シングルモードまたはマルチモードの小さな集光レーザビームを、溶接シームに垂直に高速に走査する処理で、上述の制約を克服するための手段として既に確立されている。ビームウォブルは、ビームの有効サイズを拡大しつつ、キーホール溶接に必要なレーザ出力強度を効率的に供給する。そのため、比較的大きな隙間を埋められるだけでなく、シーム幅や浸透深さといった溶接パラメータをより確定的に制御することができる。ビームウォブルをシングルモードまたはマルチモードのスポットで使用することにより、複数の用途に対して従来のマルチモードのスポット溶接よりも優れた結果が得られることが実証されている。
コヒレント社独自のビーム制御技術であるSmartWeld+は、この手法の他のバージョンよりもいくつかの点で技術的に優れている。特に優れているのは、エネルギー入力が予測可能であることだ。スポット径30μmの赤外波長(1070nm)の集光シングルモードビームに対応し、振動パターンの数と種類も拡大されていて、楕円形やらせん形、さらにはそれ以上に複雑なパターンにも対応する(図1)。これらのパターンは、サイズの拡大縮小が可能で、溶接パスや輪郭に沿って自動的に回転させることができる。スポットまたはシーム内のエネルギー分布は、微細パターン内の軌跡に沿った走査速度を調整し、場合によっては、レーザの出力変調と組み合わせることにより、正確に制御される。これにより、パターンまたは材料の異なる部分のエネルギー入力を個別に調整することが可能であるため、あらかじめ加熱する領域、加工する領域、冷却する領域を定義して、溶接池の挙動を正確に操作することができる。その結果として、溶接の精度と再現可能性が向上するとともに、熱影響部(Heat Affected Zone:HAZ)が最小限に抑えられ、ポロシティが低減する。以下では、この手法のメリットを具体的に示す加工例を紹介する。
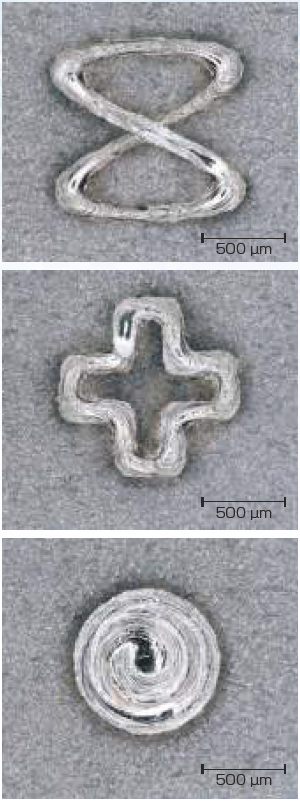
図1 SmartWeld+のパターンは、従来のビームウォブルよりはるかに洗練された動きで、楕円形やらせん形などの複雑な形状を作り出すことができる。これによって、レーザエネルギーの空間的供給を、非常にきめ細かく制御することができる。
(もっと読む場合は出典元PDFへ)
出典元
http://ex-press.jp/wp-content/uploads/2021/08/013-015_tr_dissimilar_metal_welding.pdf