ビア穴あけとウエハ剥離にメリットをもたらすCOレーザ
COレーザは、マイクロエレクトロニクス製造の未来の用途において重要な役割を果たす
一酸化炭素(CO)レーザは、広く利用されている二酸化炭素(CO2)レーザとほぼ同じくらい昔から知られているが、産業分野で大きな関心を集めるようになったのは、つい最近のことである。本稿では、COレーザがマイクロエレクトロニクス製造、特にPCB材料における40μm以下のマイクロビアの穴あけと、シリコン剥離(デボンディング)という成長中の分野において、重要な役割を果たす可能性について説明する。
COレーザの背景
5~6μmのスペクトル範囲で照射するCOレーザには、CO2レーザの遠赤外出力(10.6μm)と比べた場合に、一部の用途に対して2つの重要なメリットがある。多くの金属、薄膜、ポリマー、PCB誘電体、セラミック、複合材料は、短い波長に対して全く異なる吸収特性を示す。波長が短いほど材料の吸収率が高くなる場合は、低いレーザ出力でより効率的に加工が可能になり、熱影響部(Heat Affected Zone:HAZ)も小さくなる。一方、波長が短いほど透過率が高くなる場合は、材料のより奥深くまで光が浸透するため、それもまたメリットとなる可能性がある。
短い波長のもう1 つのメリットは、波長に比例して大きくなる回折が抑えられ、より小さなスポット径に集光できることである。例えば、標準的な構成で、産業用CO2レーザの実用的な最小スポット径は70~80μmであるのに対し、COレーザは30~40μmの範囲のスポット径を実質的に達成可能である。これは、一定の出力に対して、COレーザの照射スポットのエネルギー密度(フルーエンス)がCO2レーザの4倍であることを意味する。5μm の波長における吸収率が高いという一部の材料の性質と組み合わせると、それらの材料はCOレーザによってかなり低い出力で加工できるということになる。
ただし、そうしたメリットにもかかわらず、2つの主要な動作上の問題によって、COレーザ技術の広範な商用化は妨げられてきた。1つめは、初期のCOレーザは、極低温でしか高い動作効率を発揮できなかったこと、2つめは、シールドデバイスは急速に出力が減衰するという問題があったことである。米コヒレント社(Coherent)のエンジニアらは2015年にこの問題を解決し、同社は、室温で効率的に動作し、CO2レーザに匹敵する動作寿命を達成する、一連の産業用シールドCOレーザを発表した。
COレーザの最も有望な初期の応用分野は、ガラスのスクライブ(切断)加工と、ガラスのフィラメント切断(「SmartCleave」など)の後に行われる場合があるガラス分離である。COレーザは、セラミックのスクライブ、切断、穴あけで有効性が既に実証されている。
PCBの穴あけ
ビア穴あけは、COレーザが現時点で顕著なメリットを発揮する、重要なレーザ応用分野である。ビアとは、電子プリント回路基板(Printed CircuitBoard:PCB)にあけられる小さな穴のことで、(ビアを金属でめっきすることにより)層間の電気接続に用いられる。集積回路そのものと同様に、PCB上の回路についても密度の増加が絶えず求められる状況にあり、それによってさらに小さなビアに対するニーズが高まっている。
従来は、機械的な穴あけ加工によってビアが生成され、回路密度の低いPCBでは今でもこの方法が広く採用されている。しかし、1990年代半ばにCO2レーザによるビア穴あけシステムが登場し、機械的な穴あけシステムでは難しい100μm 以下のビア径を持つPCBの量産が可能になった。CO2レーザを採用するビア穴あけシステムは現在、50~100μmのビア径の生成に一般的に利用されている。
現在では、ますます高いパッケージ密度を達成するために、20~40μmのビア径が求められるようになっている。上述のとおり、COレーザはより小さなスポットに集光可能であるとともに、出力が比較的高いことから、この用途に対する有効な選択肢である。
コヒレント社は、この用途に対するCOレーザの実行可能性と実用性を調査するために、ビアの穴あけ試験を行っている。図1は、PCB材料として一般的に用いられるFR4に対する最新のビア穴あけ結果の断面図である。FR4誘電体層は、厚さ25μm のガラス繊維/エポキシ複合材料と直径4μmの織繊維で構成されている。外側の銅層には、レーザの吸収率を高めるためのブラウンオキサイドの表面処理が施されており、それによって銅層に穴をあけるのに必要な出力が低減されている。これは、CO2レーザによるビア穴あけシステムで用いられる標準的な表面処理である。外側の銅層が9μmと3μmのサンプル材料に対して、レーザによる穴あけを行った。ビアの穴あけに用いられた詳しいパルス特性については、図のキャプションを参照してほしい。図に示されているように、どちらの材料においても直径30μm以下のクリーンなビアを、内側の銅層に損傷を与えることなく、最小限のテーパーであけることができた。
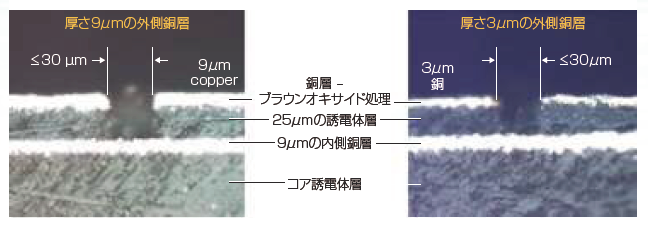
図1 COレーザによってFR4にあけられたビアの断面図。厚さ9μmの銅層に対しては、ピーク出力が1kW、FWHM(半値全幅)が3μsのパルス1個に続いて、ピーク出力が550W、FWHMが0.5μsのパルス4個を照射した。厚さ3μmの銅層に対しては、ピーク出力が 950kW、FWHMが2μsのパルス1個に続いて、ピーク出力が400W、FWHM が0.4μsのパルス2個を照射した。
(もっと読む場合は出典元PDFへ)
出典元
http://ex-press.jp/wp-content/uploads/2020/07/024_ar_CO_lasers.pdf