自動車パワートレイン製造のための高度なソリューション
ポストプロセス検査で、100%のトレーサビリティを実現
自動車メーカーとそのサプライヤーは、大きな課題に直面している。何十年もの間に徐々に進化して確立された自動車パワートレインの分野に、自動車の電動化によって、巨大な破壊的変化がもたらされようとしている。
一見したところ、従来のトランスミッションなどの部品のレーザ溶接に、将来性はないと思うかもしれない(図1)。内燃機関やトランスミッションなど、ほとんどのパワートレイン部品がこの世から消えて、電力装置、バッテリー、パワーエレクトロニクスで置き換えられるためである。
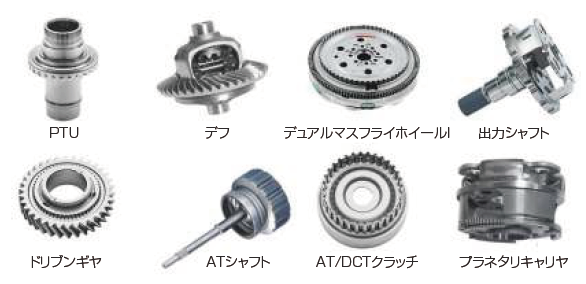
図1 標準的なレーザ溶接のパワートレイン部品。
本当にそうなのか?
さまざまな利害関係者が、異なるパワートレイン原理の市場シェアの予測を試みている。 例えば、ドイツの大手自動車部品の1 つであるシェフラー社(Schaeffler)は、30/40/30 のシナリオを予測している。つまり、2030 年までに純粋な電気自動車(EV)の市場シェアが30%、ハイブリッド車( HEV )が40%、1 つの内燃機関を搭載する従来型のパワートレインが 30% になると考えている(1)。
これは、新たな課題を生み出す。電気パワートレイン部品の搭載によって、自動車の重量は大きく増加し、自動車が内燃機関を使用している場合も加速が必要になることから、二酸化炭素( CO2 )排出量と燃費が高くなるためである。電気自動車の環境保全のメリットと相反するこうした問題を回避するために、車両重量の削減に全力を挙げて取り組むことが求められる。しかも、多大なコスト圧力の下で、それを行わなければならない。顧客にとってバッテリーが高額になることが、すでに明らかになっているためである。 接合加工全般、特にレーザ溶接は、パワートレイン部品の重量とコストの削減を可能にする実現技術である。図2は、その完璧な例である。ここでは、大きなギヤをデフケースにボルトで固定する代わりに溶接している。この加工技術は、10年前に高級車を対象に導入されたものであるため、重量とコストの削減を簡単に達成することができる。現在、この技術は、コンパクトカーや大型トラックから高性能スポーツカーに至るまでのあらゆるカテゴリの車両に適用されている。この加工は、最先端製造システムの要件を示すものとしても、好例である。
図3は、個々の部品(ギヤと[ アセンブリ前の] デフケース)から、アセンブリ可能なデフ(ディファレンシャル、差動装置)を製造するための、接合処理を構成する工程を示している。この一連の工程によって、レーザ溶接のデフを、非常に短いサイクル時間( 30 秒未満)で製造できる場合もある。
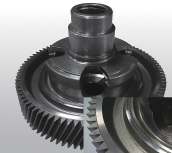
図2 レーザ溶接されたデフ。
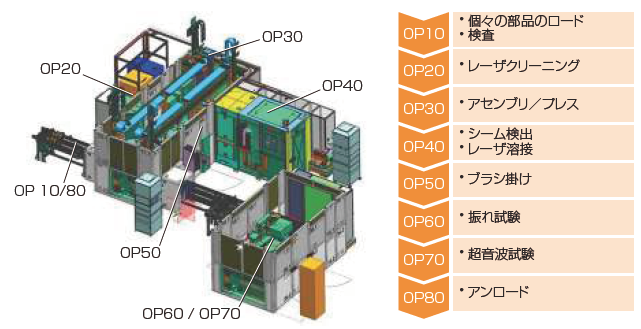
図3 EMAG オートメーション社のデフ用レーザ溶接システムの構成図。
(もっと読む場合は出典元PDFへ)
出典元
http://ex-press.jp/wp-content/uploads/2019/09/D_020-021_ar_advanced-manufacturing.pdf