高度な材料加工のための青色レーザ、日本で開発
高出力青色半導体レーザによる次世代レーザ加工システムという目標に向けて進められている、プロジェクトを紹介する。
1960年から、最新光源技術は常にレーザ加工に採用されてきた。レーザ加工技術の進歩は、国家プロジェクトと密接に関連している。日本では、1977年からレーザ加工技術の開発が行われており、CO2レーザ加工では世界最高の地位を達成するに至った。しかし2001年以降、著しい進展は見られず、その結果、現在の世界レーザ技術において、日本は、ドイツや米国に後れをとる状態にある。
ドイツでは、国家戦略に基づく政府投資が今でも盛んである。このような状況の下、日本でも複数の研究開発プロジェクトが活気を取り戻しつつある。その1つが、「高輝度・高効率次世代レーザ技術開発2016~2020年度」というプロジェクトである。このプロジェクトの1つとして、短波長・短パルスレーザとともに、青色半導体レーザによる加工技術の開発が採択されている。最終的な目標は、キロワットクラスの青色半導体レーザによる次世代加工システムを開発することにある(1)。
半導体レーザは、卓越した光強度を備え、波形が遠隔制御可能である他、将来的に製造分野で一般的に利用されるであろう、モノのインターネット(IoT:Internet of Things)や人工知能(AI:Artificial Intelligence)を活用した、オートメーションや無人工作機械に適しているというメリットを備える。これに加えて、卓越した出力を持つ青色レーザ加工システムの処理性能を迅速に実現することができれば、現状に変化がもたらされ、日本は再び、今よりも高い地位に返り咲く可能性がある。ドイツでは2016年から、「EffiLAS」という国家プロジェクトの下で、直接加工用のキロワットクラスの青色半導体レーザの開発が、国策として進められている(2)。したがって、日本の地位は予測不能であり、過去のように保証されたものではないと言えるかもしれない。
光源の分野でも、パラダイムシフトが否応なく生じている。近年の環境意識の高まりと、2014年のノーベル物理学賞から、特に照明分野で、窒化ガリウム(GaN)発光素子が多大な関心を集めている。とどまることなく高まる青色半導体素子の輝度と出力に支えられて、青色半導体レーザは、主にプロジェクター光源向けに量産段階に達している。また、高出力青色レーザは、現行光源と比べて多数のメリットがあり、産業界におけるレーザ加工の構図を書き換える可能性を秘めているとさえ言える。
青色半導体レーザ素子
ピックアップなどの用途向けの低出力光源として使用されている青色半導体レーザの性能は、著しく向上している。最近では、素子あたり3W以上の出力が、商用提供されるようになっている。
図1は、日亜化学工業の青色半導体レーザの素子あたりの出力と電力変換効率(WPE:Wall Plug Efficiency)の推移を示したものである(同社のデータに基づき、著者らがグラフ化した)。この10 年間の著しい進歩によって、出力は約10倍、効率は約2倍になっているのがはっきりと見てとれる。主な用途はプロジェクター内のランプ交換で、緑色または赤色光を生成する蛍光体とともに使用されている。青色半導体レーザは、ランプよりも寿命が長く、サイズが小さいので、このような照明やディスプレイの分野で、近年急速に利用が拡大している(3)。
その一方で、さまざまな加工目的に青色半導体レーザを適用するには、現時点ではもう少し時間が必要である。加工における重要なパラメータである光源の輝度に関しては、青色半導体レーザはすでに、赤外線(IR:infrared)半導体レーザを上回っている。商用製品を基に、素子の端面の出力密度を比較すると、近赤外線半導体レーザの高出力製品(11W / エミッタ)で、約6×106W/cm2であるのに対し、青色半導体レーザ(3.5W /エミッタ)は、約12×106W/cm2である。
レーザ加工では、材料の光吸収効率も重要な項目である。一般的に反射率は、青色よりも短い短波長域で低下するため(4)、青色半導体レーザを使用すれば、近赤外線半導体レーザよりもはるかに低い出力で、同等の加工が行えると予測される。その結果、消費電力の大幅な低下と効率の向上が期待できる。
表は、近赤外線半導体レーザや第2次高調波発生(SHG:Second Har monicGeneration)レーザ(短波長レーザの一種)と比較した場合の青色半導体レーザの卓越性を示している。上述の高い輝度と低い反射率以外にも、青色半導体レーザには、後方反射耐性が高い、故障率が低い、直接変調が可能などのメリットがある。
一般的に、可視光半導体レーザの素子は、TOパッケージ上に個別に搭載されるため、素子あたりの出力レベルは制限される(5)、(6)。今後の出力増加に伴い、複数の半導体素子を1 つの大きなパッケージに搭載するマルチエミッタパッケージに加えて、レーザバーの開発動向にも、十分に注視する必要がある。
青色半導体レーザは、近赤外線半導体レーザと比べて、単位面積あたりの生成熱が2倍以上になるため、効率的な冷却が必要である。また、青色半導体レーザに特有の高い光子エネルギーに起因する、浮遊粒子の集塵効果を防ぐために、封止性を厳密に管理できる、信頼性の高いパッケージ技術の開発が不可欠である。
より高い出力要件を満たす、高出力青色レーザを開発するには、多数のパッケージを使用してレーザモジュールを形成する必要がある。モジュール形式としては、空間ビーム出力、シングルファイバ出力、バンドルファイバ出力など、これを実現するためのさまざまな方法が存在する。シングルファイバ出力形式のモジュールを採用すれば、青色半導体レーザの高輝度特性を損なわず、取り扱いに高い自由度が生まれ、近赤外線でも使用される汎用コネクタが使用でき、高い多用途性も得られる。また、ファイバ結合モジュールにはそれ以外にも、光源部分と発光部分が分離しているので熱設計が容易、最適な部品配置が可能、出力を簡単に上げられるなど、さまざまなメリットがある。
我々のチームは、レーザ加工をターゲットに、青色半導体レーザを結合することによって高出力を達成した、高輝度のファイバ結合型青色ダイレクトダイオードレーザ(BDDL:Blue DirectDiode Laser)を開発した。半導体レーザの高輝度特性を損なうことなく、コア径100μm の光ファイバから青色レーザビームを自由に供給可能な、多用途レーザモジュールである。以下では、BDDLの基本技術、結合技術、いくつかの特性を紹介する。
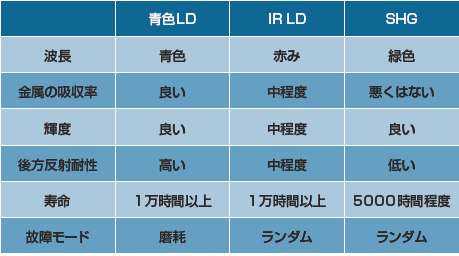
表 青色半導体レーザ(LD)のレーザ加工用光源としてのメリット。
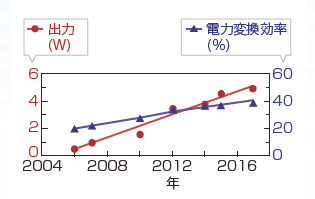
図1 青色半導体レーザの出力と電力変換効率の推移。
ビーム結合
可視光半導体レーザ素子の実用的なエミッタあたり出力はこれまでのところ、商用提供されている製品で、単一波長で約3.5Wである。それよりも高い出力を得るには、多数の素子の出力を結合するためのビーム結合器が欠かせない。ビーム結合方法は、コヒーレントな方法とインコヒーレントな方法に分類される(図2)。両者のうち、インコヒーレントな方法は、レーザ間の繊細な位相制御を必要としない、実用的な方法とみなすことができる。
インコヒーレントな方法には、多数のビームを空間的に結合する空間結合方法、偏光ビームスプリッタによって直交する偏光を結合する偏光結合方法、異なる波長を同軸上で結合する波長結合方法がある(7)。図3は、各方法を示す概念図である。各方法にはそれぞれメリットとデメリットがあり、各方法を組み合わせて使用することも可能である。
上記の方法のうち、空間結合は、同一波長の多数の半導体レーザ素子を結合して、高出力を得る目的に適している。レーザの輝度B は、レーザ出力P 、照射スポット表面面積S 、レーザビームの立体角Ωを用いて、式(1)のように表される。
ここで、λは波長、M2はビーム品質を示すパラメータである。M2は、ビームスポット半径w0 とビーム発散半角θ0を用いて、式(2)のように表され、その値は、理想的なガウシアンビームの場合に最小値の1となる(8)。
図4に示すように、多数の半導体レーザ(モードフィールド径w1、発散角θ1)を一列に整列させて、焦点距離がf1とf2のレンズによって、マルチモードファイバ(モードフィールド径w2、発散角θ2)に結合する場合、結合可能な最大数Nは、以下の式(3)で近似される。
ここで、Ffはビームの空間充填率、M12とM22はそれぞれ、半導体レーザとファイバのビーム品質である。空間充填率Ff=1で、f2w1/f1w2=1という最適な結合条件が成立する場合、結合可能なビーム数は、最大値NMAX=M22/M12となる。Mx2=11.7でMy2=5.0の波長450nmの半導体レーザ素子を使用し、コア径100μm のマルチモードファイバ(NA=0.2)をファイバとして使用する場合、空間結合可能な最大ビーム数は、約80となる。
図5は、空間結合を採用する、「BLUEIMPACTTM」シリーズの20Wタイプのファイバ結合型高出力レーザモジュールの外観を示したものである。かつてないほどの高輝度を達成する同製品は、すでに銅のレーザ加工やレーザハンダなどの用途に広く利用されている(9)。
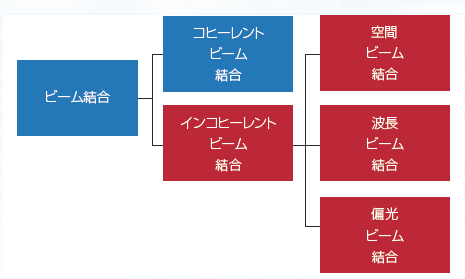
図2 レーザビーム結合方法。
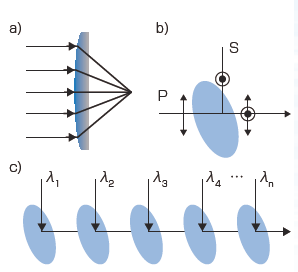
図3 (a)は空間ビーム結合、(b)は偏光ビーム結合、(c)は波長ビーム結合を示す概念図。
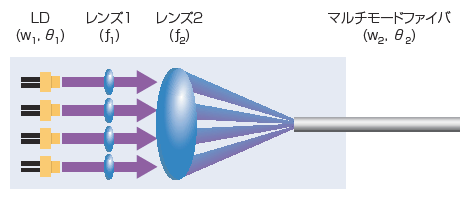
図4 マルチモードファイバへの結合例を示す図。
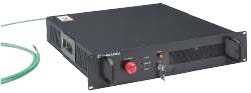
図5 20W のBLUE IMPACTTM青色ダイレクトダイオードレーザ(DDL)モジュール。
(もっと読む場合は出典元PDFへ)
出典元
http://ex-press.jp/wp-content/uploads/2019/04/tr_18-22.pdf