レーザ溶接におけるダイレクト半導体レーザ発振器でのプロセス品質と効率の改善-テーラードブランク溶接での事例
われわれの身近にあるレーザと言えば、まず第一に半導体レーザ(LD)があげられる。一家に一台と言って過言ではないレーザプリンターを始め、CDプレイヤーやDVD、Blu-rayレコーダー、レーザポインター、そして我々が日常使っているインターネットのための光通信など、日常生活には無くてはならないのがLD光源である。LDはご存知の通り消費者が安心して使える長寿命かつ安定したレーザ光源であり、いわゆる従来の共振器を使ったレーザ発振器とはまったく異なるカテゴリーに属し、”レーザ発振”が誰にでも簡単に手に入る理想的な光源である。このLDを大出力化したダイレクトLD発振器が市場に投入されて20 年、LDの利点を活かし産業界でもすでに多くのレーザ加工用途で使用され、われわれの社会に大きく貢献している。レーザ加工に使われるLDはその光を直接集光して加工に使用するもので、シンプルな構造のダイレクトLD発振器によるレーザ溶接はそのベースになるLD素子の高出力化に伴い高輝度化を実現、現在では金属接合のキーホール溶接が可能となっている。これにより従来のレーザ光源から、このシンプルで安定したダイレクトLD発振器への置き換えが可能となっている。本稿では自動車産業でなくてはならないテーラードブランク溶接を例に取り、ダイレクトLD発振器の利点について述べていく。
キーホール溶接用レーザとしてダイレクトLDを選定
テーラードブランク工法は自動車車体において重要な役割を持っている。複数の異種鋼板(板厚や材質)を、プレス成形前に目的に合わせてつなぎ合わせることにより一枚の素材の特性を部分的に変えることが可能となる(図1)。自動車車体においてテーラードブランク材を用いることで、車体の軽量化、高い剛性、耐久性、防錆、衝突時エネルギーの吸収などの安全性に対する要求を満たすことができ、デザイン性そして生産性が向上する。一般的には色々な種類のレーザがテーラードブランク溶接に使用できることが知られているが、溶接パフォーマンスとエネルギー効率の見地から各レーザ発振器の選定により無視できない差異が生じる。世界最大の鉄鋼企業、オランダのアルセロールミタル社の子会社、アルセロールミタルテーラードブランクス社(AMTB社)では、高品質な溶接結果と装置の実績により証明された堅牢性、経済性を考慮し、その結果、既存のCO2レーザ発振器をレーザーライン社製のダイレクトLD発振器に置き換えた。テーラードブランク材を製造する場合、異種のブランク材は主にレーザ突合せ溶接で接合される。これはレーザ出力を最大限効果的に伝達するためと最適な成形特徴を得るためである。このために、最も古くから知られるCO2レーザ、最近ではファイバレーザやLD励起ディスクレーザ(ディスクレーザ)などの固体レーザ、そしてLDが使用される。しかしながら当初の頃より使用されているCO2レーザはその低い電気-光変換効率による経済性の低さからだんだんと再検討が進んでいる。
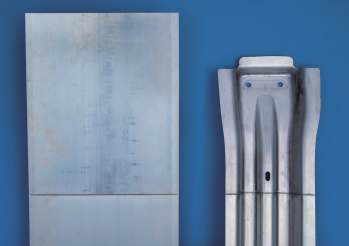
図1 ダイレクトLD発振器によるテーラードブランク溶接例(左:成形前 右:成形後)。(写真提供:レーザーライン社)
(もっと読む場合は出典元PDFへ)
出典元
http://ex-press.jp/wp-content/uploads/2018/09/p20_technology_report_laserline.pdf