ファイバレーザ溶接における最近の進歩
新しい技術によって切り拓かれる革新的な接合手法
ファイバレーザ溶接は、さまざまな材料や用途へとその適用範囲を拡大し続けている。レーザ技術とビームデリバリ部品におけるイノベーションは、銅、異質材料、薄い金属箔、フィットアップ不良がある部品の溶接など、レーザ溶接の適用がこれまで困難だった分野の課題を克服しつつある。
ファイバレーザは、ますます幅広いビーム特性、波長、レーザ出力、パルス持続時間で提供されるようになった。高度なウォブル溶接手法と組み合わせれば、高反射率材料への結合や、溶融プールの凝固動作を改善したり、欠陥を抑えたり、部品のフィットアップ不良を補いつつ溶け込み深さの制御を改善したりすることにより、そうした問題が解消できる可能性があることが示されている。
さらに、インラインコヒーレントイメージング(ICI:Inline Coherent Imaging)などの統合されたプロセス監視技術によって、豊富な情報を溶接時にリアルタイムに収集することが可能となり、メーカーは品質を厳しく管理して生産性を高められるようになっている。こうした実現技術は総合的に、さまざまな業界の高度な応用分野における、欠陥のないレーザ溶接の急速な普及促進に貢献している。
標準的な溶接ヘッドは、コリメートされたレーザビームを、必要なスポット径に集束するように設計されており、焦点面上の固定スポットに対するビームデリバリによって、ビーム経路が固定される。この標準構成を採用する場合、各設定は特定の用途にしか適用できない。一方、ウォブルヘッドは、標準的な溶接ヘッド内に走査ミラー技術が搭載されている。内部ミラーでビームを変向することにより、焦点はもはや固定ではなく、形状(図1a)、振幅、周波数をさまざまなパターンで変化させることによって動的に調整可能となる。ビーム速度vcは、ウォブル周波数fとウォブル径Dによって、vc= π Dfの関係で制御することができる。
最良の結果が得られる周波数設定は、スポット径、ウォブル径(つまり円形速度vc)、直線溶接速度によって異なる。効果的なビーム速度も直線溶接速度vwに依存するが、ほとんどの場合においてビーム速度vcは、溶接の動きを決定付ける溶接速度vwよりもはるかに高い(図1b)。また、この溶接手法は標準的な同軸ノズルやアシストガスポートと互換性があるので、プルームが抑制できるほか、リモート溶接に用いられる走査ヘッドにそのままでは適用できないスパッタ手法を制御するうえでも好都合である。
このウォブル手法のメリットは、スポット径が小さい場合ほど高まる。スポット径が小さいほど、莫大な出力密度が達成されるので、近赤外(NIR:near infrared)波長を使用する場合に、銅やアルミニウムなどの材料の高反射率の問題を解消して、広いプロセスウィンドウで安定したキーホールが作成される。また、最適なウォブルパラメータを適用すれば、ポロシティや溶接割れを防ぐことができる。これによって、1μmのファイバレーザによるE モビリティやバッテリ製造という新たな応用分野が開拓され、周波数を二倍化した緑色レーザは不要となる。
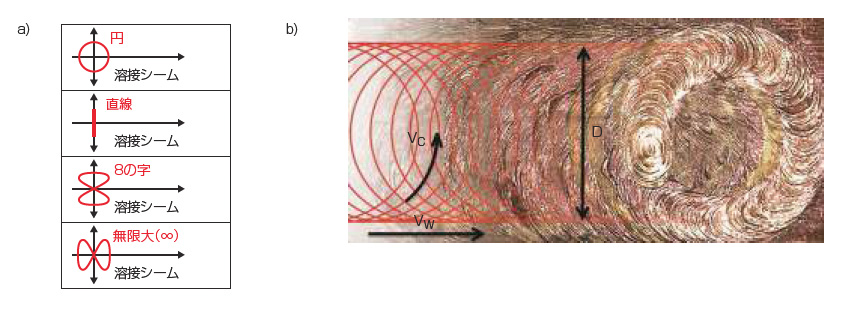
図1 ウォブルパターンの概念図(a)と、円状ウォブル動作の様子(b)。
連続波溶接
新しいバッテリー技術が開発されて大容量化が進んだことにより、接合技術の需要は高まっている。Eモビリティ部門は特にこのトレンドを促進しており、自動車業界とその供給メーカーは、電気自動車(EV:Electric Vehicle)のバッテリーや電力ストレージ製品で大量に必要となる銅やアルミニウム製の接合部を量産するための堅牢で効率的な溶接プロセスを求めている。
銅や銅合金のレーザ溶接が難しいのは、材料の2つの主要な物理的性質に起因する。つまり、ほとんどの種類の産業用高出力レーザに対して吸収率が低いことと、加工時の熱伝導性が高いことである。加工開始時の近赤外レーザの固体銅への吸収率はわずか4%ときわめて低く、そのために材料への結合は難しい。緑色レーザの532nmのような、短い波長でのレーザエネルギーの吸収率は高いが、深溶け込み溶接に必要な高いレーザ出力や、その波長において産業向けに実証されたレーザは、まだ提供されていない。
シングルモードまたは低モードの1μmの近赤外ファイバレーザは、1kWのシングルモードレーザで20μmという小さなスポット径に集束可能で、1MW/cm2を超える出力密度が得られるため、そうした問題に対する解決策となる。出力密度がこれだけ高ければ、吸収率の低さを簡単に克服し、溶融または蒸発した銅の吸収率を最大で60%以上にまで高めて、安定したキーホールを形成することができる。
銅溶接のもう1つの問題は、溶融物の粘度と表面張力が低いことによる不安定性で、それは、低速での溶接時にスパッタやブローホールにつながる恐れがある(1)。速度を毎分10m以上にまで上げれば、そうした不安定性が軽減され、プロセスは安定する。しかしそうすると、最良の溶接パラメータが、ロボットなどの従来型のモーションシステムが限界に達する範囲に入ってしまう。加えて、速度の増加とともに溶け込み深さは浅くなり、溶接部は非常に細くなる。これを補うには、レーザ出力を上げなければならないが、それにはシステム技術に対するさらなる設備投資が必要になる。
新しいプロセスを調査した結果、そのような事態を回避できることが明らかになった。溶接方向の速度を上げるだけでなく、ウォブルヘッドなどによって動的に位置決めを行うことにより、プロセスを安定化することができる(2)。このウォブル手法は、低い直線溶接速度で、溶け込み深さに対する影響を最小限に抑えつつ、安定した溶接部を生成することができる。たとえば、深さが1.5mmまでの高品質な銅溶接を、出力がわずか1kWのシングルモードファイバレーザによって達成することが可能である(図2)。
同じ手法が高輝度マルチモードレーザにも適用可能で、溶接可能なあらゆるグレードのアルミニウムの溶接の品質と一貫性を向上させるために使用されている(図3a)。温度上昇と冷却速度が従来のレーザ溶接よりも緩やかなので、欠陥をなくしてスパッタを管理するうえで都合がよい。標準的な手法とウォブル手法で同じ3.5kWの出力で5000シリーズのアルミニウム筐体(図3b)を溶接した結果を比較すると、ウォブル溶接のほうが、外観が美しく、ポロシティがなく、安定した溶接部が得られた。溶接の溶け込み深さはどちらも2mmで、溶接速度はウォブル手法のほうがやや低速だったが、全般的な品質の差から、ウォブル手法のほうが優れていると判断できた。
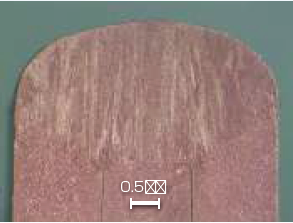
図2 3本のフラットなC1100銅ワイヤーをシングルモードのファイバレーザで溶接した例。
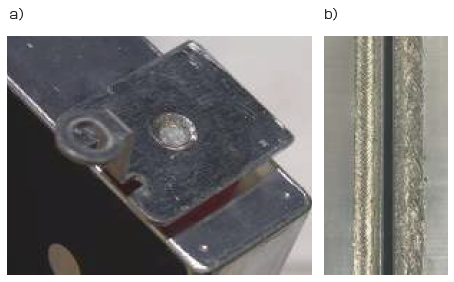
図3 (a)は、1100と3003のアルミニウム製バッテリー筐体の溶接。(b)は、5000シリーズのアルミニウムをウォブルあり(左)とウォブルなし(右)で溶接した場合の溶接品質の比較。
溶接形状の調整
ジョブショップ(受注生産工場)やメーカーは一般的に、さまざまな種類の部品を扱っており、それぞれの部品に固有の溶接要件に対応するための柔軟性を必要とする。ウォブル径が可変であることには、光学部品を変えたり、ビームの焦点を変えたりすることなく、溶接の幅と深さが変更できるというメリットがある。エネルギー入力が一定である場合、発振振幅の増加にともなって、溶接形状は従来のネイルヘッド状から矩形プロファイルへと変化する(図4)。この制御によって、溶接断面の調整が可能で、たとえば、高電力バッテリーパックのセルコネクタに適用して、大きな溶接接触部を生成することができる。接触部が大きければ、溶接接合部の抵抗が低くなり、機械的に安定した接合部となる。
図5は、SS304の材料に対して、出力400W、スポット径200μmでウォブル振幅を変化させた場合の影響を示したもので、溶接のスタイルを、キーホールモードから伝導モードへと移行できることが示されている。円状のウォブル動作を適用するパターンが、溶接方向を変えながら複雑なパスを溶接する場合に最良の結果を示した。銅とアルミニウムなどの異質材料を重ね合わせて接合する場合は、溶接深さを制御することによって、材料の希釈を制御することができる。下側のシートを浅く溶融することにより、溶融材料の量を最小限に抑えることができ、希釈を制御して金属間相を抑制することができる。
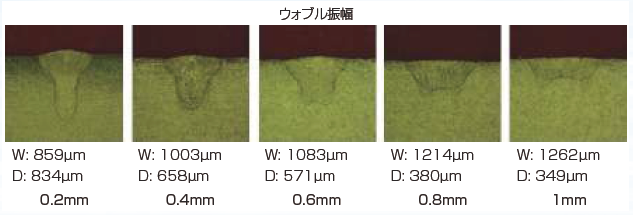
図4 ウォブル溶接ヘッド「IPGD30」を使用して、ウォブル振幅(直線パターン)の調整によって溶接形状を調整した様子を示している。
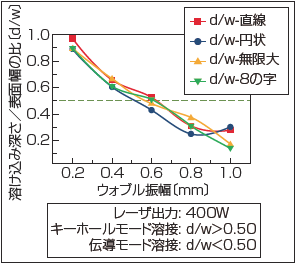
図5 溶接プロセスに対するウォブル振幅の影響。
(もっと読む場合は出典元PDFへ)
出典元
http://ex-press.jp/wp-content/uploads/2018/09/p14_technology_report_fiber_laser_welding.pdf