航空機製造に向けて前進する積層造形技術
エコロジカル・フットプリント(環境フットプリント)の高い削減効果が期待される。
独エアバス社(Airbus)が積層造形(AM:Additive Manufacturing、付加製造)プロセスを検討し始めたのは20年以上前のことである。まずは、プラスチックとラピッド・プロトタイピングを導入し、その数年後には、レーザ積層造形(LBM:Laser Beam Melting)と電子ビーム積層造形(EBM:ElectronBeam Melting)を金属に適用した。同社にいまだやや残る問題は、確かなビジネスケースをともなう積層造形ソリューションを確立することで、ほぼすべての産業的意思決定がビジネスケースに関する議論を中心に進められる中で、いかにしてそれに踏み切るかということである。今後の選択肢を慎重に検討することによって基本的な数値を絶えず改善していくことを試みるよりも、積層造形を導入すれば95%の確率で、プロジェクトを簡単に、安価に、迅速に開始することができる。
迅速な製品開発
積層造形の能力を示す1つの例が、装置そのものである。同社は2012年に、250W(250×250×280mm)のLBM装置をまずは1台導入したが、現在では400W/1kWのレーザ(800×400×500mm)が2~4台稼働している。今後10 年間で、まったく新しい種類のマルチレーザシステムが登場し、この動きをますます後押しすることになるだろう。低コスト製品に対するビジネスケースも、中期的に(2020年以降まで)は同社にとって実行可能性を示すものになる見込みである。250を超える金属積層造形プロジェクトを手掛けてきたこの7年間で学んだ最大の教訓は、積層造形が、統合性に優れた多機能製品の製造を可能とし、将来的にはエコロジカル・フットプリント(環境フットプリント)の面で、大きな可能性をもたらすということである。
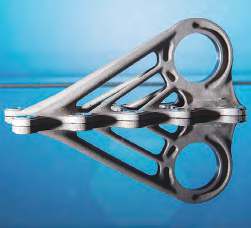
図1 レーザ積層造形( LBM )によってチタンで製造されたバイオニックデザインのキャビンブラケット。
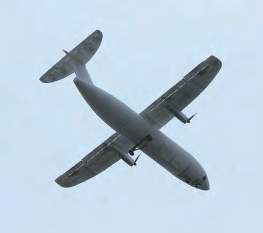
図2 完全に積層造形によって製造されたTHORの航空機が飛行する様子。
材料、プロセス、装置
材料:将来のビジネスケースに基づき、エアバス社は最初にチタン(Ti6-4)、続いてイノックス(Inox)を採用し、2018年末までにアルミニウムの適用を計画している。Ti6-4を用いたLBM/EBMに基づく積層造形は、2015年末以降、技術成熟度レベル(TRL:Technology Readiness Level)6で行われており、2015年末には、独プレミアム・エアロテック社(Premium AE RO TEC、エアバス子会社)から初となる少数生産のシリアル部品が供給された。
2018年以降のシリアル生産に向けて、可能性を秘めたもう1つの材料がScalmalloyである。Scalmalloy とは、エアバス社子会社の独AP ワークス社(AP-Works)が管理する高性能アルミニウム合金である。エアバス社は2018年以降、実質的なシリアル生産の開始に利用可能な、初となる一連の積層造形材料を入手する予定になっている。将来の積層造形シリアル生産における最大の課題の1 つが、墘コストの金属粉末の入手可能性なので、その将来のニーズに向けて、あらゆる取り組みが世界中で進行しているのは喜ばしいことである。
プロセス:熱溶解積層法(FDM:Fused Deposition Modeling、米ストラタシス社[Stratasys]のFortus装置に採用されている)は、2年前から「AirbusA350 」の部品に対してシリアル・モードで適用されている。ポリアミド(PA)を用いた粉末焼結積層造形法(SLS:Selective Laser Sintering)は、デモ用部品に使用されているほか、同社の新しい貨物輸送機「Beluga」用のヘリコプターやブラケットの最初のシリアル生産に適用されている。耐火性が高くないことから、今のところ旅客機にはまだ適用されていない。
(もっと読む場合は出典元PDFへ)
出典元
http://ex-press.jp/wp-content/uploads/2018/04/ilsj_arp18-1.pdf