高精度スキャニングシステムにおける熱影響の管理方法
ガルボスキャナで、全体的なスループットを大幅に改善
どのようなモーション制御でも確実に成功させるには、多数の重要な設計細部に気を配らなければならないというのが、高精度エンジニアリングの一般原則である。たとえば、機械加工や組み立てにベストプラクティスを適用すれば、高性能システムが構築される可能性は最大限に高まるし、安定した動作環境を維持するには特別な注意を払う必要がある。特に熱影響の管理と緩和は、何よりも重要なことである。
ガルバノメータ(ガルボ)スキャナは、レーザ微細加工や積層造形(AM:Addi tive Manufacturing、付加製造)において利用が増加している(図1)。帯域幅が非常に広いことから、従来のサーボステージ構成(「固定ポイント」のレーザシステムなど)よりも高速な処理が可能で、全体的なスループットを大幅に向上させることができる。システムの加熱とそれによるひずみを管理することの重要性は、サーボ駆動のステージ、アクチュエータ、システムにおいて昔から十分に理解されているが、それと同程度の対策では、最新の高速スキャニングにおける類似の影響に対処できるとは限らないのが実情である。しかし、ガルバノメータ・システムの加熱の根本原因を調査すれば、この問題を管理して、全体的なシステム性能を高めるための最良の設計方法に関する直接的な洞察を得ることができる。
ステージベースのシステムにおける熱ひずみは通常、ステージそのものの膨張にともなって生じる。熱源となるのは一般的にステージモーターで、その影響は、非線形である場合が多いものの、測定可能で、緩和できる可能性もある。たとえば、温度センサを適切に配置すれば、モーション・コントローラによって温度変化を直接測定し、命令で指示したモーション・プロファイルを変更することによって、ステージの膨張や収縮を補償できる場合がある。一方、スキャニングシステムにおける熱ひずみへの対処は、それほど単純明快ではない。熱源(とその緩和対策)は、必ずしもそれと同じではないからである。具体的な熱源と、それに対して提案される対策を紹介する前に、まずは、スキャニングシステムにおいて熱影響を最も受けやすい構成要素について説明する。
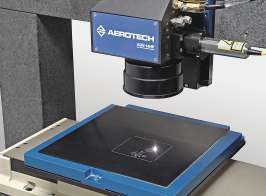
図1 ガルボスキャナは、帯域幅が非常に広いことから、より高速な処理が可能で、レーザ微細加工や積層造形における全体的なスループットを向上させることができる。
スキャニングシステムの構成要素
スキャニングシステムが加熱することによる最も明白な悪影響はおそらく、ガルボモーター/ミラーを収容してそれらを互いに適切な位置に固定する、アルミニウム製ブロック/筐体(以下、固定ブロック)のひずみだろう。しかし、後ほど説明するが、熱源は必ずしも明白ではないので、それを緩和するには、多数の設計手法を適用しなければならない場合がある。固定ブロ ック上に温度差が生じると、ミラーの相対的な位置がずれ、多数の非線形の「ドリフト」誤差が生じて、確立した性能や校正結果からのずれが生じる。
モーターの加熱は、明らかな問題である。モーターの巻線は、温度が一定以上上昇すると、完全に破損してしまう。また、過熱によってミラー固定部が緩んで破損すると、少なくともシステムの剛性と応答が変わり、ミラーが完全に外れた場合は、壊滅的破損につながる恐れさえある。
ガルボモーター内の位置センサ(光学式エンコーダやそのほかの種類のアナログ光学デバイスである場合が多い)も、温度変化にともなって一般的に非線形の動作を示す。その性能低下は、熱または時間に起因するドリフトにともなって現れ、全体的なシステム誤差の主要要因である場合が多い。
最後に、ミラーコーティングの反射率そのものも、温度に依存する。室温において、あるレーザ波長に対して最適化されたコーティングは、温度が高くなると効率が低下する場合がある。反射率のピーク位置は、λの値が高くなるとずれる傾向にあるためである。
もう察しがついただろうと思うが、上述の問題に対する解決策は、熱影響そのものと同様にまちまちなのである。
スキャナのミラーは、レーザエネルギーによる過熱の影響を直接的に受ける。ミラーコーティングは効率が非常に高くなるように作成されているが(一般的に、対象波長における反射率は99.5%以上)、入射レーザエネルギ ーの一部は、ミラーによって熱として吸収される。この加熱によって生じえるシステム全体の熱ひずみに加え、あまりに多くのエネルギーを吸収すると、ミラー固定部が破損し、モーターから外れてしまう可能性がある。
この熱源に対する対策としては、より大きなミラーを使用すること(そうすれば、一定のエネルギー吸収による加熱効果が抑えられる)か、ミラー背面に空気冷却機構を設けて熱を排出することなどが挙げられる。このような冷却機構により、レーザエネルギーに対するミラーの処理能力は3倍以上高まるが、空気がミラーに当たることによって、ミラー位置に少しぶれが生じる可能性がある。さらに高い反射率(99.8%以上)を達成するカスタムコーティングも利用できるが、そうすると、高額な経常外費用がかかり、リードタイムも長くなってしまう場合が多い。
ガルボ固定ブロックそのものに入射するレーザエネルギーも、スキャニングシステムの主要な熱源である。自由空間を伝搬するほとんどのレーザビームが、ガウス分布に従ってエネルギーを放射する。ビーム径は、光強度が最大値の「1/e2」になるときの幅と定義される。この値(ガウス分布における最大値の約13.6%に相当)から、ビームエネルギーの約4.4%は、公称ビーム径の範囲内に含まれていないことがわかる(また実際、ガウス分布の裾部分は無限に減衰していく)。たとえば、公称ビーム径14mmのビームを開口部が14mmのガルボ筐体に照射すると、ビームエネルギーの4.4%は、アルミニウム製ブロックの加熱に使われることになる。また、ビームの位置がずれていると、さらに多くのレーザエネルギーが、ブロックの入力開口部を通って照射する代わりに、筐体そのものに入射してしまう。
(もっと読む場合は出典元PDFへ)
出典元
http://ex-press.jp/wp-content/uploads/2018/04/ilsj_trp14-1.pdf