リモートレーザ溶接で、新型フォードマスタングの製造を促進
時間、空間、生産性の効率を向上するテクノロジー
レーザ材料加工は、生産性が鍵を握る自動車業界における現代的な自動製造手法として確立されている。特にリモートレーザ溶接は、この要件に合致している。オンザフライ溶接(Weldingon-Fly)モードでレーザビームを照射すれば、最高水準の生産性が達成できる。このモードでは、スキャナをベースとするリモートレーザ溶接ヘッドがロボットと連動した連続的な動作によって、3次元ビームポジショニングを非常に高速に実行する(図1)。溶接シーム間の時間を最小限にすることで、レーザの稼働率が、従来のレーザ溶接をはるかに超えるレベルにまで引き上げられている。
本稿では、米フォード社(Ford)の新型マスタング(図2)の製造という、量産製造環境におけるリモートレーザ溶接のメリットを紹介する。
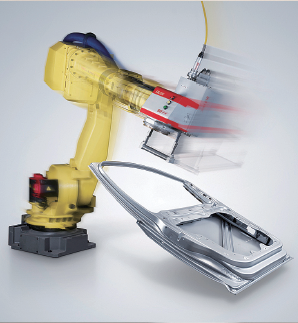
図1 オンザフライ溶接モードにおいて、溶接ヘッドはロボットと連動した連続的な動作によって、3次元ビームポジショニングを非常に高速に実行する。
目的
フォード社の目標は、新型マスタングのデザインに対応する大規模な片側接合方法を開発することだった。耐衝撃性能を継続的に向上させたいという要求と、各種安全規格の強化に伴い、強度の高い高度な鋼鉄を車体構造に使用するケースが増加している。多くの先進的な車体構造設計において、ルーフレールやA ピラーといった部分にハイドロフォームチューブが使用される。このような設計を適用するには、そのメリットを最大限に活かすために先進的な片側接合技術を開発する必要がある。従来の抵抗スポット溶接では、接合部の両側へのアクセスが必要だが、この種の溶接を可能にするためにハイドロフォームチューブを切断してアクセスホールを設けると、構造的な脆弱性が生じてしまい、ハイドロフォームチューブの設計意図に反する。片側接合は、最大限の構造的完全性を実現する手法で、顧客の健康と安全にメリットがある。 そこでフォード社は、スポット溶接ではなくリモートレーザ溶接を採用することにした。独II-VI ハイヤグ社(II-VI HIGHYAG)のリモートレーザ溶接ヘッド「RLSK」(図3)を使用した新しい片側リモートレーザ溶接手法によって、構造的脆弱性をなくし、生産性を向上させることができる。
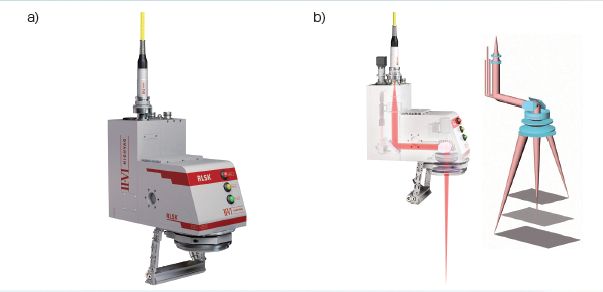
図3 (a)は独II-VI ハイヤグ社のスキャナベースのリモートレーザ溶接ヘッド「RLSK」。(b) は、同製品を真横から見た様子と機能原理を示した図。
実装
このプロジェクトは2012 年に始動し、2015 年にはフォードマスタング用のリモートレーザ溶接プロセスが連続量産製造工程に組み込まれた。4 基のリモートレーザ溶接セルがミシガン州デトロイトにあるマスタング製造工場に導入された。そのうちの2基では、4台のRLSK溶接ヘッドによって車体側面の内側アセンブリ部品の前処理が行われ、溶接が行われる箇所にくぼみが付けられる。残る2 基のレーザセルでは、8台の溶接ヘッドによって、車体側面の内側および外側アセンブリ部品の溶接が行われる。
RLSK 溶接ヘッドによって、車体側面の内側アセンブリ上にある34 カ所のリモートレーザ溶接構造が接合される。積層部の厚みは最大で2mm にものぼる(図4a)。ステッチ溶接およびC 溶接が行われ、ウィービング振動によって厚みのある積層部で適切なS 値が得られるようにする。また、車体側面の外側アセンブリがリモートレーザ溶接される。クーぺモデルで79 カ所、コンバーチブルモデルで61 カ所の溶接部が存在する(図4b)。軟性の溶融亜鉛めっき鉄( HDGI:Hot Dipped GalvanizedIron)でできた0.7mmの車体側面外側アセンブリを、多様な材料や厚みの車体側面内側アセンブリに、G型の溶接デザインで溶接することで、品質の堅牢性が強化されている。
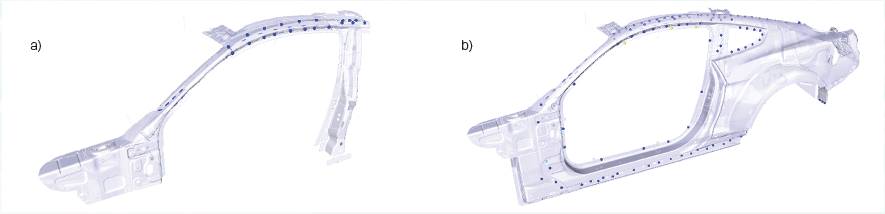
図4 フォードマスタング車体側面の内側アセンブリ(a)と外側アセンブリ(b)上の溶接構造。
(もっと読む場合は出典元PDFへ)
出典元
http://ex-press.jp/wp-content/uploads/2017/04/ILSJ1704_Application_Report1.pdf