ビーム診断によるレーザ積層造形製造の改善
プロセスコストとスピードの改善が、優れたパーツの品質を達成するために必要とされている。
レーザ積層造形製造(LAM:LaserAdditive Manufacturing)が、金属部品の試作及び製造の両方において、瞬く間に重要な製造手法になり始めている。しかしながら、この技術はまだその緒についたばかりであり、新しい材料の開発と様々なプロセスパラメータが結果に及ぼす影響を理解することは、未だ重要な仕事となっている。特に、LAM手法は、一般的にレーザの性能に対するプロセスウィンドウ(製造条件の最適範囲)が小さい。そのため、ビームや走査のパラメータの極僅かな位置的変化が、著しく加工品質に影響する。本稿では、最適な結果を得るためのレーザビーム特性の必要性を検証し、新しいビームモニタリングの技術が、レーザをベースにした3D製造システムで、どの様に高速測定を可能にするかを示す。この技術は、最終的に、LAM を利用して製造された部品の品質に重大な影響を与える前にビームの問題を特定、修正することが可能になる。
LAMの基礎
殆どの伝統的な加工技術は、切削を利用したもので、すなわち、要求された形状を作成するために、基板から材料を選択的に除去することである。積層造形(付加的製造)法は、全く逆で、何もない状態から、層を積み重ねていくものである。粉末溶融結合(PBF:Powder Bed Fusion)は、完成品を製造する主要なLAM 技術(”LAM手法”を参照)であるが、金属粉末を用いて、レーザで溶融する3 次元プリンターの基本的な形態である。PBFでは、まず、約20 〜60μm の厚さの金属粉末層が、リコーターブレードを用いて、ビルドプレート(垂直に移動可能なプラットフォーム)上に均一に広げられる。次に、レーザを粉末上に走査して、その層に求められるパターンで、選択的に溶融し、再凝固させる。層が完成した後、粉末床を層の厚さに相当する量だけ下ろし、新しい粉末層をその上に広げる。
レーザはその層を書き込み、プロセスは完了するまで反復される。最後に、残った溶融されなかった粉末を除去して、完成した部品を露出させる(図1)。
PBFでは、一般的に200〜500W相応な出力クラスの近赤外(NIR)発振のイッテルビウム(Yb)ファイバレーザが使用される。これらは2 次元(x とy)でスキャンされ、高品質のf-θ走査レンズで集光され、100μm 程度のスポットサイズを実現する。出力とスポットサイズの組み合わせは、金属粉末を迅速に溶融するのに充分なフルエンスを容易に生成する。実際には、パワー密度は、ビルドプレートを切断ないしは穴を開けたり、金属粉末内に浸透するほど高くならないことが重要である。レーザは、新しい層の粉末および前の層の少量を完全に溶融して、最適に双方を完全に結合し、部品全体にわたって均一な材料特性を引き出す必要がある。
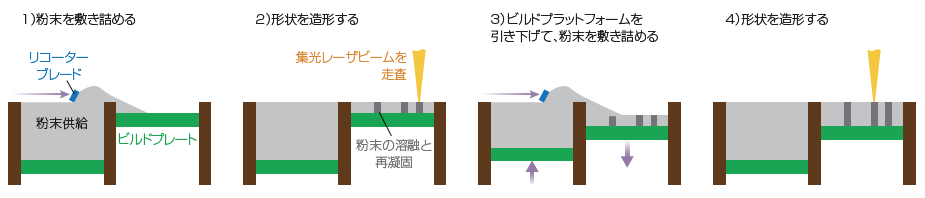
図1 PBFの基本ステップ。
最近のLAM応用
ポリマー材料による3D プリンターの柔軟性とスピードは、エンジニアリングやプロトタイピングの目的で広く使用されている。金属で作業し、堅牢な機械的特性を有する完成部品を提供する能力は、航空宇宙、歯科、自動車レース、さらには宝石加工を含む様々な産業において、実際の生産部品を製造するための有用な技術となっている。 具体的には、PBF は、機械的に複雑で、他の方法を用いて製造するのに費用がかかる高価で重要な部品を製造するのに最も効果的に利用されている。例としては、複雑な曲線や内部に穴や溝がある形状のものである(図2)。
PBFの優れた例は、GEアビエーション社(GE Aviation)の高バイパスターボファン(LEAP)ジェットエンジン用燃料ノズルの製造である(1)。同社によれば、内部支持構造と冷却経路で作られたこの単一の部品は、18個の別個の部品からなる機械加工されたアセンブリに置き換わっている。LAM で製造された部品は、機械加工された同等品よりも25%軽く、約5倍の耐久性がある。各々のLEAP エンジンには19個のノズルが組み込まれているため、この軽量化の結果、燃費が大幅に向上している。
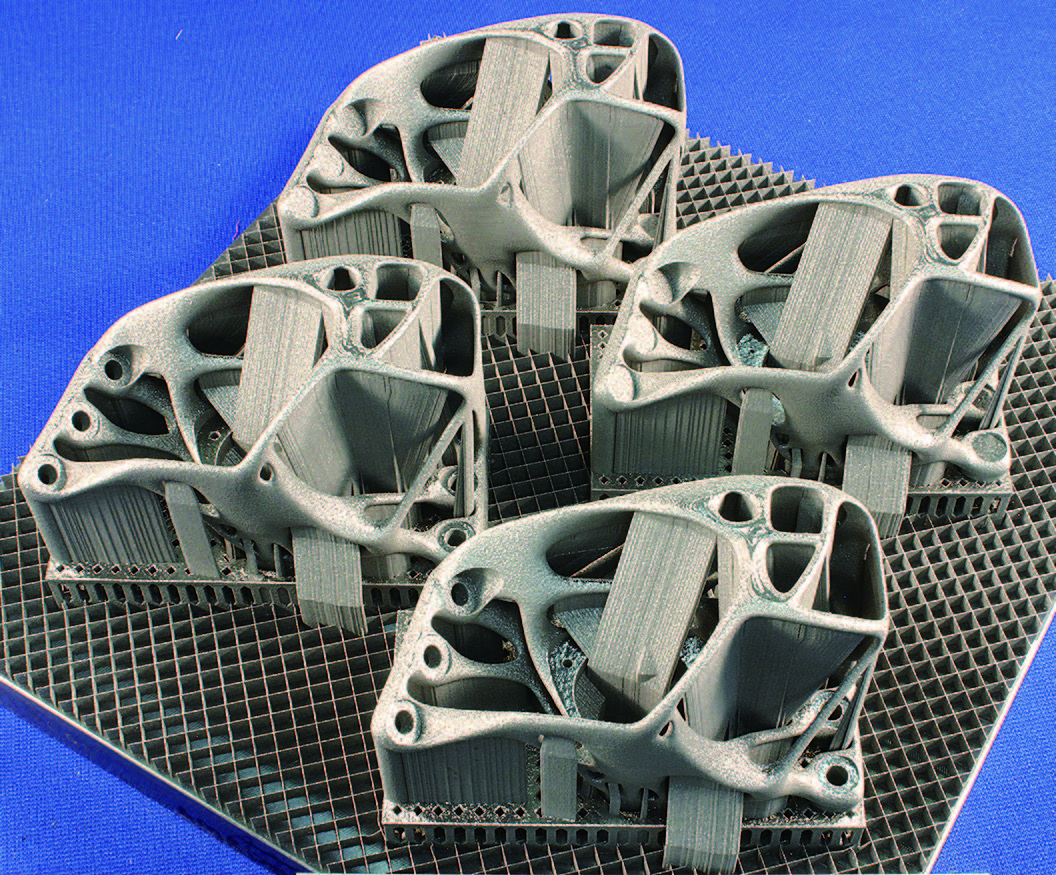
図2 PBF製センサブラケットは機械的安定性を最適化する複雑な形状をしているため、従来の製造方法では実現が困難である。(写真提供:ペンシルバニア州立大マテリアルサイエンス社 CIMP-3D )
技術的なチャレンジ
市販されている洗練されたターンキーPBFシステムは既に数多く存在するが、これらは一部の用途で適切な結果を得るために必要なきめ細かなレベルのプロセス制御を提供するものではない。例えば、堆積プロセスに困難を生じさせる可能性がある製造中の部品の配置に関する様々な考慮事項が存在する、または完成品に望ましくない応力特性をもたらす。これらは、現在の商用システムでは、常に完璧に適応することはできない。
また、商用LAM システムでは、材料に関連したコスト課題がある。例えば、これらのシステムは、アルミニウム、コバルト、チタン、ステンレス鋼、およびニッケル合金を含む様々な粉末に対応するが、粉末の種類により異なる堆積パラメータセットが必要となる。多くの場合、それは装置供給メーカーの専有技術であり、通常は1万〜2 万ドルの価格で個別に購入する必要がある。また、それらは装置に直接ダウンロードされるため、ユーザーは特定のニーズに合わせてプロセスを最適化または変更するために必要なすべてのパラメータにアクセスできるとは限らない。
材料に関しては、現在使用している粉末は、伝統的な鍛錬金属製造技術(通常、溶融、成形、およびその後の熱処理の複数の工程で構成)用に開発されたすべての合金であることも重要である。それらはまた、LAMの間に急速に溶融し、再凝固した際に、同じ望ましいバルクの物理的性質(例えば、引張強度)は得られない。したがって、LAMで利用された場合に特に改善された物理的特性をもたらす新しい材料の開発が、重要な研究分野となっている。
実際、このことは技術の実用性を拡大する上で不可欠である。このような背景から、既存のシステムを改良し、各プロセスパラメータを完全に調査して制御することができる独自のLAMシステムを構築したいと望む研究グループやエンドユーザーが多数存在する。これにより、結果を改善させ、より明確で決定論的なプロセスの開発が可能となる。
(もっと読む場合は出典元PDFへ)
出典元
http://ex-press.jp/wp-content/uploads/2017/04/ILSJ1704_Technology_Report2.pdf