レーザ技術による、自動車効率の改善
レーザ加工、柔軟な軽量車体製造を支援
レーザ技術は、乗用車のCO2排出量削減における重要な鍵を握る。レーザに基づく多数の自動車製造用のイノベーションがこの目標の達成に貢献しており、本稿ではその概要を紹介する。
未来の自動車は、これまでのモデルよりも格段に軽量になる見込みで、レーザに基づく製造プロセスがその進歩において重要な役割を演じる。その例としては、フランジのないパーツ、アルミニウムや炭素繊維強化プラスチック( CFRP:Carbon Fiber ReinforcedPlastic)といった高機能プラスチックの利用の増加、熱成形やプラスチックと金属の結合などが挙げられる。このようなイノベーションは車体の軽量化を促し、ひいては航続距離の延長やCO2排出量の削減につながる。
レーザを利用した軽量車の構築
従来式のスポット溶接によって金属シートを結合する場合、端同士を重ね合わせることが必要になる。一方、レーザビームで溶接すれば、フランジレスの設計が可能である。この場合、個々のシートをまず、さねはぎ結合によって組み立ててから、レーザで溶接する。これには複数の利点がある。つまり、スポット溶接と比べて加工時間が短い、結合する部分は材料や厚さがそれぞれ異なっていてもよい、最終的な構造には冗長な材料が含まれないため軽量化が図れるといった利点である(図1)。また、クランピング技術を適用するには通常、かなりの労力が必要となるが、結合する2 つのパーツを事前に配置することによって、シンプルで低コストのクランピング補助で済ますことができる。
負荷が高く、さらなる安定性が求められる部分には、必要に応じて補強構造を付加する場合がある。これに対応する構造(自動車のアンダーボディなど)を、従来のよりも少ない工具で実現することができる。また、この目的のために、生産準備段階において入念な作業によって製造しなければならないような特殊な工具は必要ない。それどころか、処理に必要な作業はすべて、標準のレーザ溶接ロボットによって実行することができる。
このプロセスによる優れた例の1 つが、ドイツの郵便局(Deutsche Post)に導入された「StreetScooter」である。ドイツのアーヘン工科大(Rhenish-Westphalian Technical University )発のスピンオフ企業によって開発され、フランジなしで作成されたアンダーボディの上に構築されている。現時点で、約40 台のこのようなマイクロバンが試用されており、これまでのところ、何の問題もなく適切に稼働している。
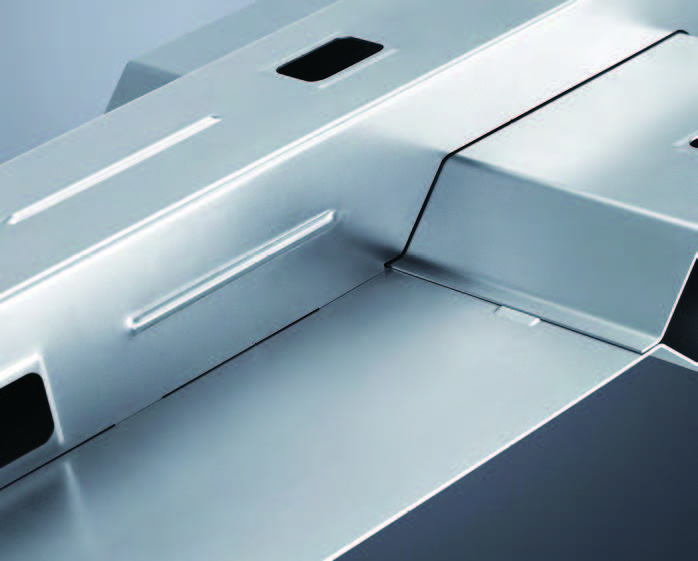
図1 フランジレス構造は、従来式のスポット溶接と比べて加工時間、材料使用量、重量の面で多数の利点がある。
レーザによって、異種材料の革新的な組み合わせが可能に
炭素繊維強化プラスチックも、軽量車設計によく使用されている。特に、電気のみで走行する自動車である。レーザ技術は、このような材料の切断や加工において明らかに利点がある。レーザを使用すれば、材料に触れることなく、また、何の圧力も加えることなく、切断が可能で、材料の形状と構造が変化しないことが保証される。これによって、非強化材料の場合でも、ゆがみが生じるリスクが軽減される。使用される製造プロセスによって、切断や加工は、CFRP部品の成形の前または後に行われる場合がある(図2)。炭素繊維材料からブランクを切り取る処理に対し、独トルンプ社(TRUMPF)は、3D部品を切断するための空間成形ビーム熱源「TruDisk」を装備した「TruFiber」レーザシステムを提供している。切断対象が、(バインダーに既に埋め込まれた)CFRP、ガラス、または炭素繊維マットであるならば、このレーザシステムが優れた選択肢である(図3)。このシステムを使用すれば、レーザが繊維をきれいに溶かして除去する(図4)。
製造プロセスの改善につながる、レーザ技術を用いたもう1 つの方法は、接着剤を使用せずにプラスチックを金属材料に熱接合することである。金属とプラスチックは融解点の差が大きいため、従来の溶接技術ではこれは不可能だった。しかし、短パルスのレーザを使用すれば、金属上にアンダーカットの定義済みパターンを作成し、そこに加熱された結合対象のプラスチック部品を圧接することができる。その後、プラスチックが冷めて凝固すると、2つの材料はフォームフィット接続によって結合される(図5)。このような接続に対する引張強度の検査からは、結合部が基本材と同等の強度を持つことが示されている。この方法による接続部は、耐圧性と防水性を備え、動的負荷をかけても安定性を維持する。
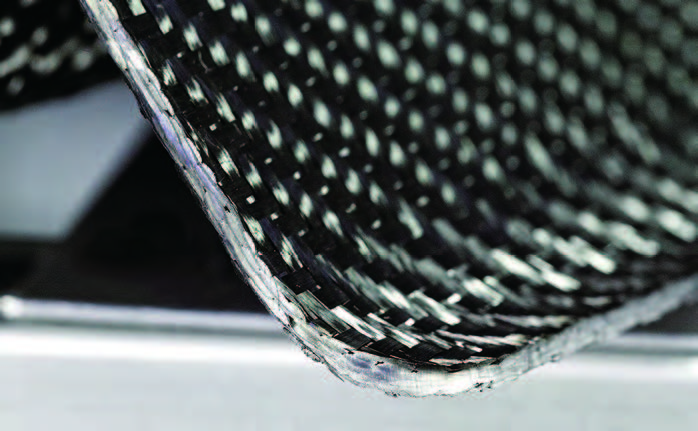
図2 炭素繊維強化プラスチックは、成形前でも後でもレーザで切断可能である。必要ならば、純粋な炭素繊維マットを、接着ポリマーを充填する前または後に切断することができる。
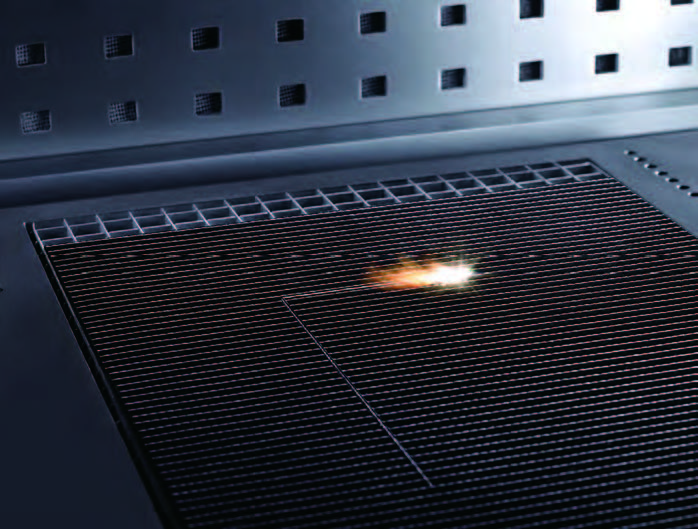
図3 硬化したCFRP部品の切断。材料の厚さが4mm未満の場合は、レーザの方がウォータージェットやフライスよりも2〜3倍速く、品質の高い切断部が得られる。
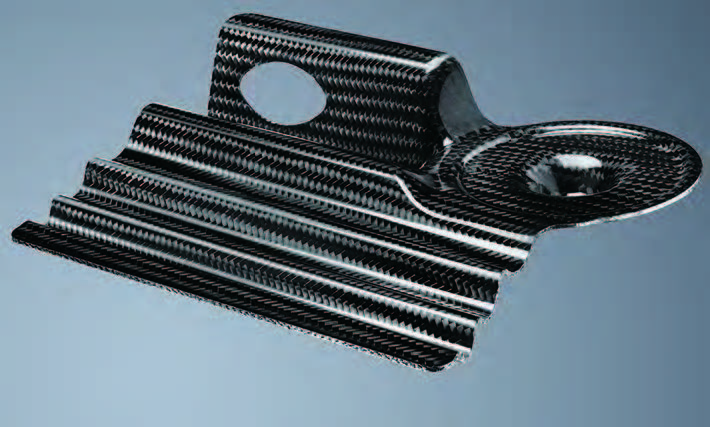
図4 レーザ光は、編み込み状の部品をニアネットシェイプに滑らかに切断することができる。切断部に対する仕上げ加工は不要である。
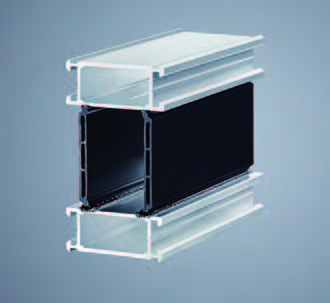
図5 金属と繊維からなる複合材がしっかりと結合されている。超高速レーザによって、金属部分にアンダーカットを作成することで、ポリマーと加熱された金属を一緒に適切に融解させる。
熱成形におけるレーザの利用
ホットスタンプ加工は、車体パーツの大幅な軽量化を可能にする。しかし、焼入鋼は硬度が高く、プレス機では切断できない。レーザ技術は、この問題も見事に解決する。3Dレーザ切断によって、部品を摩耗させることなく、また、圧力を加えることなく切断する(図6)。
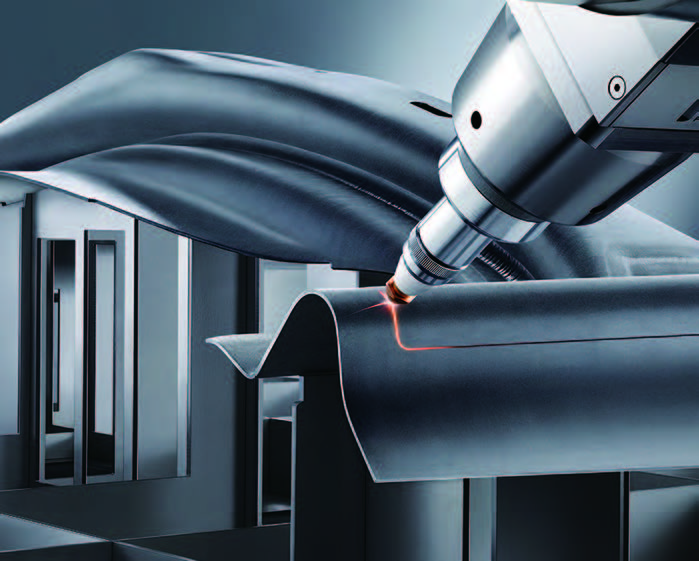
図6 3Dレーザ切断は、部品を摩耗させることなく、また、圧力を加えることなく切断し、しかも高い生産性を発揮する。
(もっと読む場合は出典元PDFへ)
出典元
http://ex-press.jp/wp-content/uploads/2016/11/ILSJ_Sep16_ar3.pdf