パワートレイン溶接におけるファイバレーザとディスクレーザ
固体レーザがもたらす効率改善とコスト節減の可能性
ほんの数年前まで、トランスミッションメーカーにとって「レーザの世界」は、極めてシンプルなものだった。ドリブンギア、オートマチックトランスミッション(AT)やダブルクラッチトランスミッション(DCT)用のクラッチ部品、全輪駆動(AWD)や車軸用部品といったトランスミッション部品の溶接には、CO2
レーザが使用されていた(図1)。独トルンプ社(TRUMPF)の「TruFlow」シリーズや米ロフィンシナール社(ROFIN-SINAR)のスラブレーザ「DC0xx」といった最先端レーザが多く採用されている(1)。これらのレーザは高機能で、1日に数百万件もの接合が可能である。溶接ヘッドや、ビーム伝送ユニット、監視デバイスといったシステムコンポーネントも提供されており、成熟した状態にある。
しかし、この5年間の間に、トルンプ社の「TruDisk」ディスクレーザや米IPG フォトニクス社(IPG Photonics)のファイバレーザといった輝度の高い固体レーザの使用が急速に増加している傾向が見てとれる。独EMAG 社は2008年、パワートレイン溶接機「EMAGELC 160」の発売とともに、パワートレイン部品に対してファイバ/ディスクレーザを使用し始めた(2)。それ以来、CO2レーザからファイバ/ディスクレーザへの劇的な技術移行を、われわれは目の当たりにしている。本稿ではその理由を探っていこう。
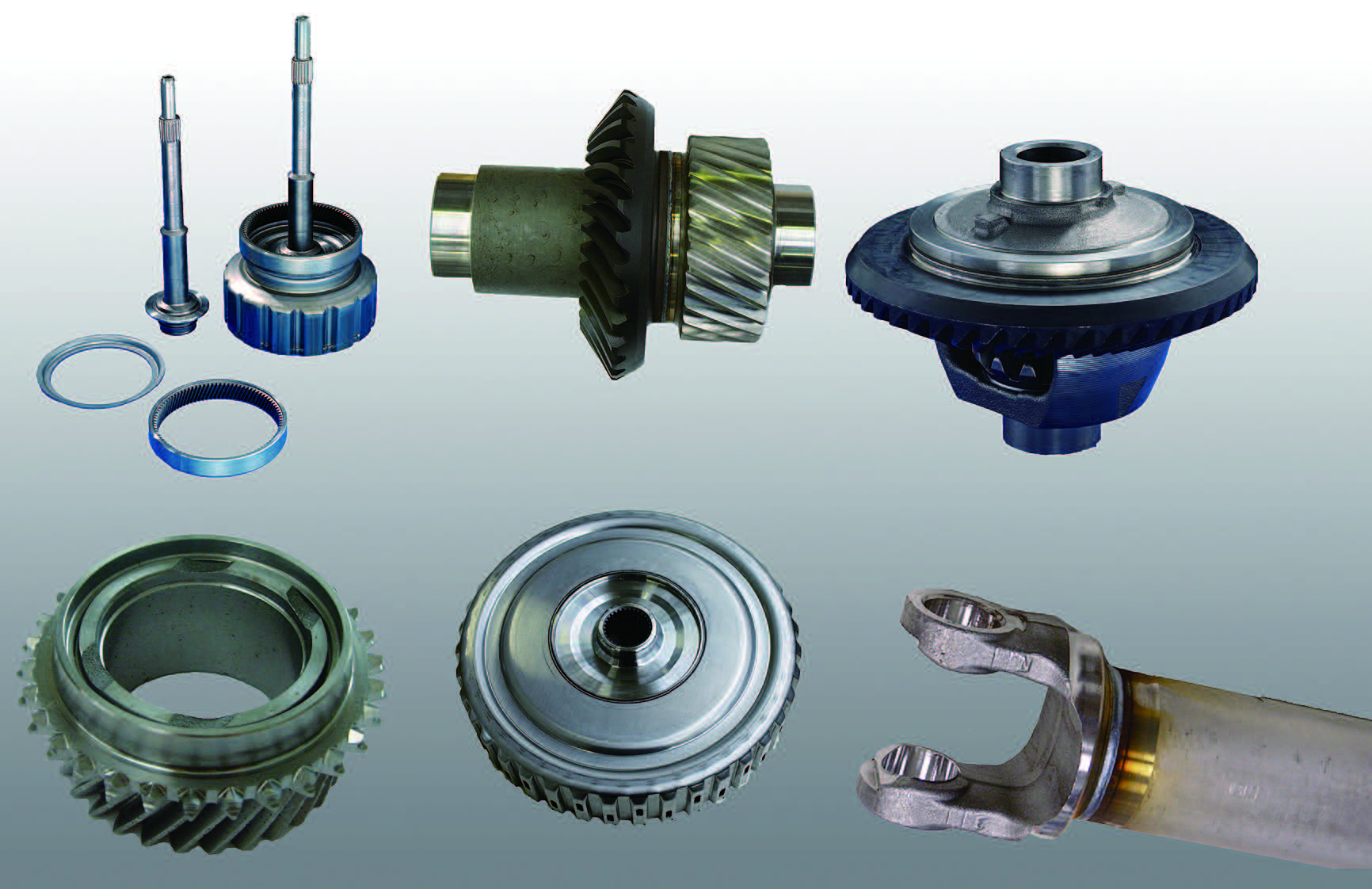
図1 一般的なパワートレイン部品
稼働コストの比較
レーザ溶接機の稼働コストを押し上げる最大の要素は、電気代とガス代である。
電力消費量: CO2レーザはエネルギー効率が低く、一般的な4kWのCO2レーザを最大出力(4kW)で動作させた場合、最大で56kWもの電力を消費する。また、大きな冷却装置の稼働にさらに電力を消費し、冷却機能に少なくとも52kWが必要になる。4kW出力のディスク/ファイバレーザの消費電力は約17kW で、冷却装置もコンパクトである。
ガス消費量: CO2レーザには、レーザガスと加工ガスが必要である。最新のCO2 レーザはガス消費量が低く、分離されたヘリウム、窒素、二酸化炭素の代わりに混合済みガスが使用できる。ヘリウム、アルゴン、またはその混合ガスなどのシールドガスは、溶接処理を安定化させ、溶接面を保護するために必要である。ヘリウムの供給不足は以前から問題になっているが、多くの用途において、アルゴンを代用することができる。ディスク/ファイバレーザには、シールドガスはまったく不要である。EMAG社は、すべてのパワートレイン用途に対し、加工ガスとして空気を推奨している。これによって、ガスを調達して個別に保管する必要がなくなる。溶接面には薄い酸化皮膜が生じるが、溶接品質は概ね完璧である。
稼働コスト総括
製造環境では、実際のデューティ比を考慮に入れてコストを計算する必要がある。図2は、概算コストを示したものである。CO2レーザ溶接機をディスク/ファイバレーザのものに変えると、稼働コストは約50%低下する可能性があることが示されている。
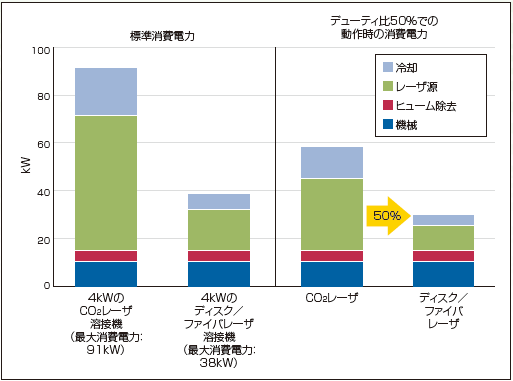
図2 CO2レーザとディスク/ファイバレーザの概算消費電力の比較
システム配置
CO2 レーザ溶接機は長年にわたり、工場見学に訪れる人にとって「必見」の装置だった。設置面積が巨大であることから、通常の作業現場とは別の部屋に配置されることもあり、レーザ溶接機に個々の部品を運び入れたり溶接済み部品を運び出したりするための物流管理もかなりの規模になる。特に1 つの装置で複数の溶接ステーションとして機能する必要がある場合は、ビーム伝送にも高度な技術を要する。
ディスク/ファイバレーザを採用する溶接機ならば、状況は一変する。これらのシステムでは、レーザまで部品を持ってくるのではなく、レーザを部品まで持っていくのである。コンパクトな溶接ステーションは、製造ラインの部品フローに完璧に統合可能で、材料を取り扱うための装置(コンベア、バスケットスタッカー、ガントリー、ロボット)が少なくて済み、全体的な設置面積も縮小される。最大で50mの長さの伝送ファイバが簡単に使用できるので、レーザ源そのものは別の場所に配置することができる。ディスク/ファイバレーザは標準で複数の出射端を装備するため、ビームの伝送と制御の両方が最小限にまで簡素化される。
(もっと読む場合は出典元PDFへ)
出典元
http://ex-press.jp/wp-content/uploads/2015/10/ILSJ150926-28-1.pdf