自動車と航空業界におけるディスクレーザ
調節可能なナノ秒パルス長によって実現される連続生産
モビリティのグローバルな高まりに加えて、新興工業国の経済成長やますます進むグローバル化が、自動車と航空業界の継続的な成長を支える推進力となっている。それに伴うCO2汚染や気候温暖化といった環境への影響と、使用可能な化石資源の減少を受けて、エレクトロモビリティ(Eモビリティ)や軽量構造の分野の開発が進められている。車体の軽量化においては、この傾向が特に顕著に見られ、この10年間で多くの新素材が開発されて工業生産に実用化されている(アルミニウムとチタンの合金や、炭素繊維強化プラスチックなど)。
このような材料を、従来の製造プロセスを適用して加工すると、通常はかなりの労力とコストがかかる。レーザは非接触で摩耗とは無縁のツールであるため、優れた代替手段である。上述の材料に対する典型的なレーザ加工といえば、インコネル(Inconel)やチタン合金などの耐熱性金属でできたタービンブレードに冷却孔をあける処理や、電池膜に微細孔をあける処理がある。炭素繊維強化プラスチックの切断に加えて、そのような材料の修復もますます重要性を高めている。この補修処理では、修復パッチを当てられるように破損部分をレーザで少しずつ除去することが行われる。
材料の溶融温度と熱伝導率は非常に高い場合が多いため、それらをレーザで加工するには、数10 〜数100 キロワット程度のパルスピーク出力と、0.1mm範囲への集光が必要である。独イエナオプティック社(Jenoptik)が提供する「JenLas disk IR70」や「JenLas diskIR70E 」(図1)などのダイオード励起ディスクレーザは、ピーク出力が高く、このような用途に最適である(表1)。パルス長がナノ秒レベルで柔軟に調節可能で、パルス繰り返し周波数が数百kHz と高いことから、これらのレーザは、プロセスの開発および最適化と、連続生産における工業用途の両方に理想的なツールである。また、統合と制御が容易で、堅牢性に優れ、24時間年中無休稼働に耐える高い信頼性を備えることで、他とは一線を画す製品となっている。
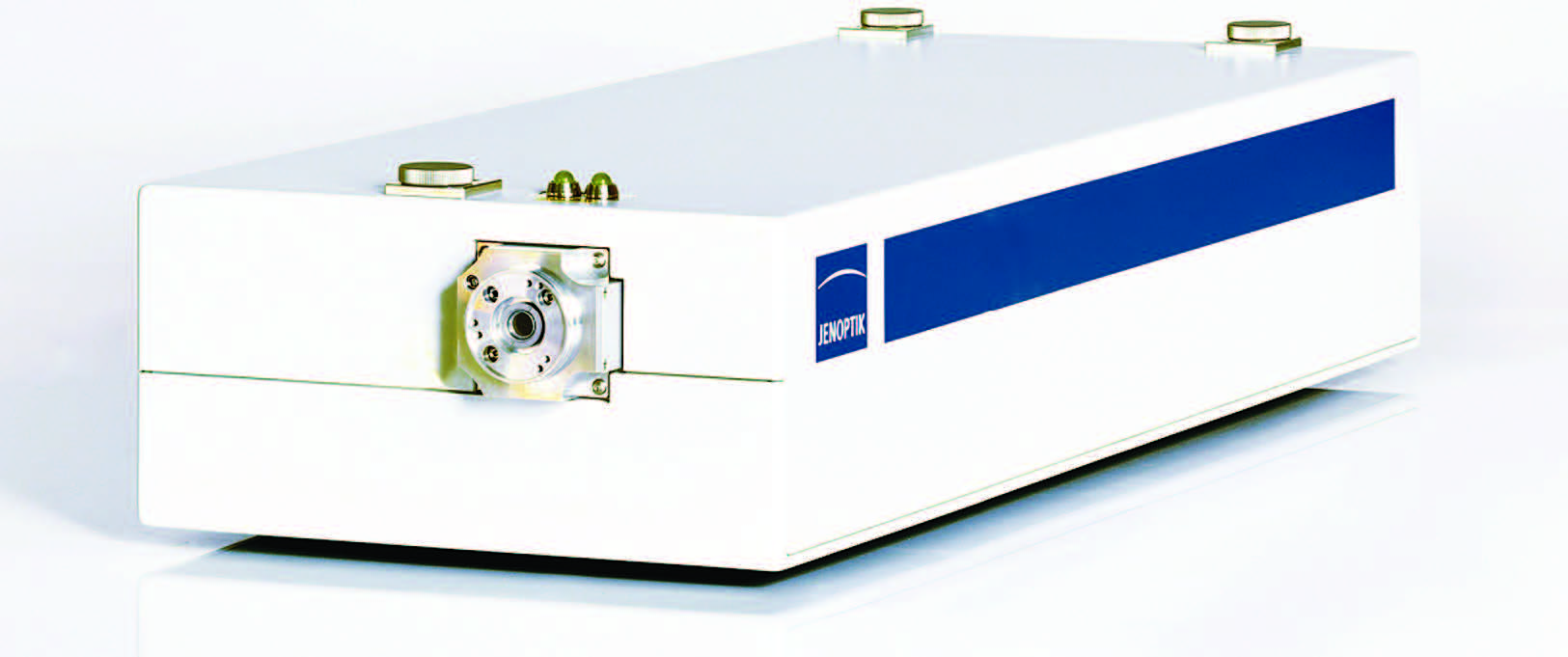
図1 「JenLas IR70/IR70E 」ディスクレーザ
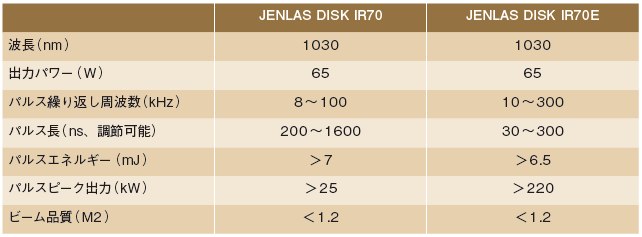
表1 「JenLas disk IR70 」と「JenLas disk IR70E 」のレーザ仕様
加工結果に対する影響
ナノ秒レーザによって得られる加工品質は、材料に加えられる熱に依存する。この点においても前出のレーザは非常に優れており、パルスピーク出力が高いことから、インコネル、アルミニウム、チタン合金といった耐熱性材料への熱の印加が抑えられるため、熱影響部(HAZ:heat-affected zone)は最小限にとどまる。一般的には、レーザ照射時間が長いほど、熱影響部は大きくなる。このことから、加熱、溶融、蒸発という温度に基づく中間段階で構成されるアブレーション工程における、熱拡散長とアブレーション速度の間の相関関係を導き出すことができる。
表2 は、AlMg3 アルミニウム合金に対するディスクレーザを用いたシングルパルスアブレーションの例を基に、パルス長がアブレーション速度に与える影響を示したものである。
複数のパルスまたはパスを適用することによってアブレーション処理を行う場合は、より多くのレーザパラメータ(出力、繰り返し周波数、パルスオーバーラップなど)を考慮に入れる必要がある。パルス間隔は通常、印加した熱が完全に放散するほど長くはない。その場合、材料の基本温度が上昇して、溶融温度や蒸発温度に早く達する。しかし、熱影響部も大きくなるため、材料に与える損傷も大きくなる。
図2 は、パルス長と溶融温度/ 蒸発温度に達するまでの時間の関係を示している。パルスエネルギーが同一の場合、パルス長が長いほど、材料温度の上昇と低下は緩やかになる。そのため、表面を傷つけることなく、より多くのエネルギーを材料に加えることができる。この動作は、例えば、厚さが数ミリ程度の金属を溶融切断する場合や、プラスチックを溶接する場合に望ましい。
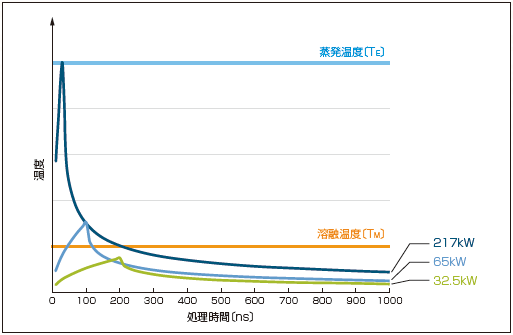
図2 シングルパルス照射における、パルス長と溶融/ 蒸発温度の関係を簡素化したモデル
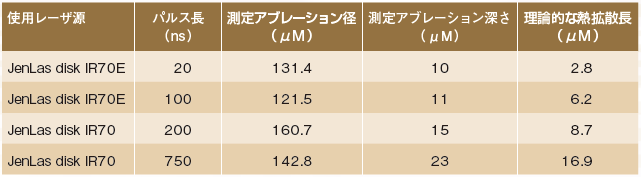
表2 パルス長がアブレーション結果に与える影響
レーザ穴あけ
レーザ穴あけでは、材料を取り除くために加工面が蒸発温度に達する必要がある。穴が底面に達するまで上面から材料が除去される。この過程において、溶融粒子が表面や穴の壁面に付着し、極端な場合は穴が再びふさがれるという最悪の事態に陥る可能性がある。この処理が改良され、材料は上面と底面の両方から除去されるようになった。材料の厚さと穴の大きさによって、2 種類の穴あけ方法を適用することができる。原則としては、直径が集光範囲以下(一般的には100μm未満)の小さな穴には、パーカッション穴あけ(図3)が適用され、中〜大の大きさの直径(一般的には100μm以上)には、トレパニング穴あけ(図4)が望ましい。
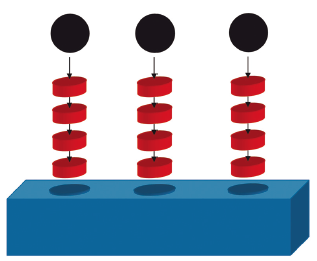
図3 パーカッション穴あけ
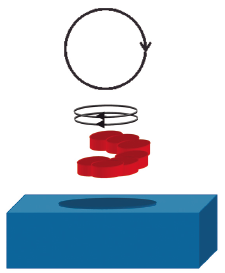
図4 トレパニング穴あけ
(もっと読む場合は出典元PDFへ)
出典元
http://ex-press.jp/wp-content/uploads/2015/10/ILSJ150922-25-1.pdf