高出力ダイオードレーザシステムによる高効率ホットワイヤークラッディング
クラッディング(肉盛り)は、金属基材表面の特性(耐摩耗性、耐腐食性、耐熱性)を改善するために表面を新しい素材の層で覆ったり、使用によって摩耗した材料表面の修復をする目的で使われる。高出力ダイオードレーザを用いたシステムは、従来のクラッディング技術による方式や他のレーザ方式と比較して著しい利点があるため、この分野での応用が広まり始めている。本稿ではダイオードレーザ技術の概要と共に、ホットワイヤークラッディングシステムにおいて、これらのレーザをどのように構成することができるかについて述べる。パウダー供給方式のクラッディングに比べ、ワイヤー供給方式のクラッディングは、独特の利点を備えているために価値が高い。
従来のクラッディング方式
クラッディングで、母材とは異なる構成を持つ新たな表面層が形成される。従来のクラッディング技術は、アーク溶接法と溶射法の大きく2つの方式に分類される。それぞれの方式には、使用する材質、クラッド層の品質、加工速度、プロセスの互換性、コスト等の様々な問題点において独自の特長がある。
アーク溶接技術( PTA と呼ばれるプラズマ粉体肉盛など)では、母材表面を融解するのに電気アークが使用され、通常、シールドガス中で作業が行われる。クラッド素材は、ワイヤーまたはパウダー方式にて供給され、それらもアークによって融解され、それによってクラッド層が形成される。溶接技術により、非常に強度の高く、衝撃特性に優れ、ピンホール(気泡のようなもの)の少ない完全溶接された金属結合が得られる。この方法では、材料付着速度が高く(これは加工処理速度が高いことを意味する)、投資コストも比較的低く抑えられる。
アーク溶接クラッディングの1つの大きなマイナス点は、材料に及ぼす高温で、それにより機械的な歪みを生じさせるので、クラッディング後に後処理が必要になることも多い。その他にも、母材が高温になるため、クラッド材料と混ざってクラッド層が希釈されること(従って、純粋にクラッド材料だけで構成されない)も大きなマイナス点である。これにより、クラッド層に本来求めていた特性が減じられることになる(耐腐食性、耐摩耗性など)。この対処法として、複数のクラッド層で覆ったり(これによって連続する層ごとに希釈分が少なくなる)、1つの層自体を厚くする事があるが、これを行うと、その分時間がかかることになり、材料のサイズが変わるという問題が発生する。
溶射法は、クラッド材料を炎または電気により融解し母材に噴霧する。母材は熱せられないため、部品の歪みの可能性は最小限に抑えられる。溶射法の最大の欠点は、クラッド層と母材との結合が本質的に冶金的な結合ではなく機械的な結合であることである。この事はクラッド層の付着力を弱め、耐摩耗性が低くなる。その一方、一部のプラスチックも含め高熱に耐えることのできない材料でも被覆が可能となる。
レーザクラッディングの長所
レーザクラッディングは、パウダー状あるいはワイヤー状で供給されるクラッド材料をレーザによって溶解し、そのクラッド材を母材基板の一番外側の表面として形成する。レーザクラッディングは従来の方法と比較して、いくつもの独自の長所がある。アーク溶接技術と比較した場合、レーザクラッディングは熱による歪みが少なく、母材金属によるクラッド材料の希釈が少なく、またピンホールが少なく、そして表面の均一性に優れる。これらの特性は後処理の必要性を無くし、つまり、そのための時間やコストを大幅に削減する。そしてレーザ工法が生み出す高い冷却効率により、被覆の粒子がより細かくなり耐腐食性が高まる。さらに概してどの出力レベルにも適用されることで材料付着速度の利点がある。それに対して、多くのアーク溶接工法では、クラッド品質は出力および材料付着速度の増大とともに低下する。
レーザ技術や溶射技術はいずれも、材料への過熱を避け、希釈を最小限にとどめることができる。しかし、溶射とは異なり、レーザクラッディングは、母材との真の冶金的な結合を形成するため、付着性と耐摩耗性に優れている。さらにレーザで得られた冶金的な結合被覆は、機械的なコーティングによくあるひび割れや層間剥離を抑止する。
高出力ダイオードレーザ技術
レーザクラッディングが本来持つ利点にもかかわらず、従来のレーザタイプは、必ずしもこれらの利点がすべて発揮されているとは言えず、出力特性、運転コスト、運用のしやすさの点で大きな問題も抱えていた。この用途に対するより最適な手段へのニーズに対応するため、高出力ダイオードレーザ技術を用いたクラッディングシステムがここ数年導入されてきている。
高出力ダイオードレーザシステムは、ダイオードレーザバーで構成されている。ダイオードレーザバーは、シングルモノリシック半導体基板上に実装された多数の個々のレーザエミッターで構成されており、総出力は100W を超える。これらの直線上のバーを順番にさらに水平あるいは垂直方向に積み重ね、高出力ダイレクトダイオードレーザシステムとして数キロワットレンジの総出力を得る。光学系は、これらの個々のバーをすべて1つのビームとして出力をまとめるために使用される。
現在の高出力ダイオードレーザシステムは、クラッディングのニーズに十分対応した出力とビーム特性を備えており、その運用面においても、高い柔軟性を持っている。たとえば、コヒレント社製HighLight Dシリーズは、最大10kW(波長は、975nm)の出力が可能なので高い生産性のクラッディングに十分対応できる(図1)。さらにこのレーザは、そのライン・シェープ・ビーム(エネルギー密度が均一な線形状ビーム)のサイズを簡単にカスタマイズでき、被覆の幅と厚さに応じて高精度で大面積の高速加工が可能である。それに対して、他の多くのレーザは小型の丸いビームであるために、高速、大面積のクラッディングには十分な対応ができない。
またダイオードレーザシステムは他のレーザタイプに比べて、より理想的な波長特性を持ち、いくつかの実用的な利点がある。特に固体レーザ(DPSS)、ファイバレーザや遠赤外CO2 レーザよりも短いダイオードレーザの波長出力は、下部の母材やクラッド合金に吸収されやすい。このことは、ダイオードレーザは、CO2 レーザよりもはるかに少ない出力でクラッド材料を被覆させることができることを意味する。
さらにダイオードレーザは、他のレーザタイプに比べてコスト面で大きな利点があり、特に、CO2レーザやダイオード励起Nd:YAG レーザまたはファイバレーザに比べて、大幅に運転コストが低く、電気的効率が高い特徴がある。材料への波長吸収率の良さを加えて考えると、さらに運転コストを下げ、二酸化炭素排出を低く抑え、さらに材料付着効率が上がる利点が見える。
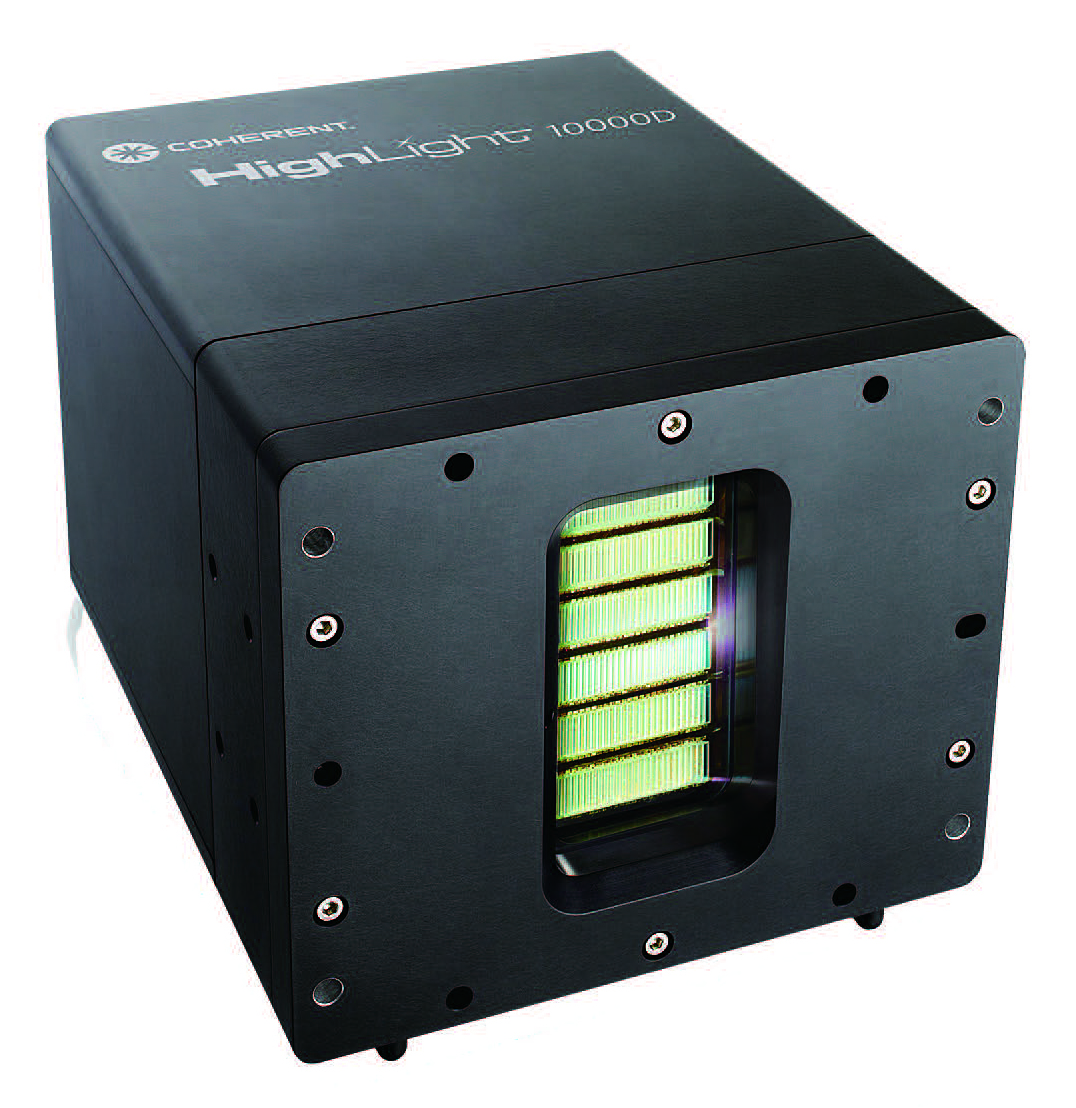
図1 コヒレント社製HighLight 10,000D はコンパクトな高出力( 10kW )ダイオードレーザシステムであり、幅広い範囲のビーム形状(1 〜12mm のビーム幅 ×6 〜36mm のビーム長さの組合せ)にて、具体的なクラッディング加工の要望に最適な対応が可能である。
(もっと読む場合は出典元PDFへ)
出典元
http://ex-press.jp/wp-content/uploads/2015/10/ILSJ150912-14-1.pdf