自動車産業におけるレーザ応用
自動車産業は環境にやさしい、運転していて楽しい、スタイリングが美しい、そしてコストパフォーマンスの高いといったお客様のニーズに応える自動車を提供しつづける必要がある。レーザ加工はこれらのニーズを満足させるための一方策として有効である。図1にこれまでのレーザ機器の進化と自動車車体組み立てにおけるレーザ加工の関係を示す。車体組み立てのレーザ加工はレーザ発振器の進化とともに適用形態を変化させてきたことがわかる。1980年代のkW級CO2レーザ発振器の出現により2 次元の鋼板溶接が可能となりテーラードブランク溶接が適用された。また90年代後半に出現したkW級YAGレーザ発振器は光ファイバでのレーザ伝送可能という特徴を持つためロボットを活用した3次元溶接、ブレージングを可能にした。2000年代になると高輝度レーザであるディスクレーザ、ファイバレーザ発振器の出現により高効率なリモートレーザ溶接が可能となった。本稿ではこれら車体組み立てにおけるレーザ加工の適用事例について紹介する。
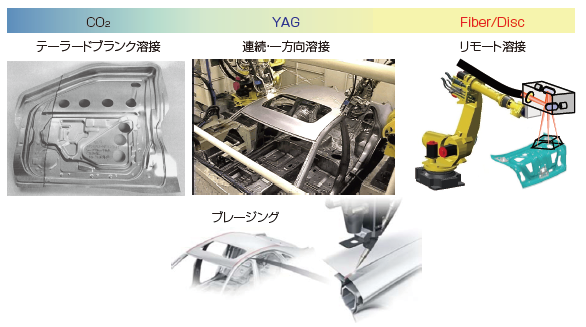
図1 レーザ機器の進化と車体レーザ加工
軽量化テーラードブランク溶接
テーラードブランク溶接とはプレス加工のトリム工程で発生する端材やコイルから切り出したブランク材といった、2次元の平板同士を突合せ溶接し、一体でプレス成形する工法を表わしている。図2にテーラードブランク工法の概念図を示す。通常、鋼板の溶接部は固く伸びにくい組織になるがレーザ溶接は溶接線が細く周囲の母材が塑性変形を助けるため絞り成形や張り出し成形が必要な部品への適用も可能である。
本技術のメリットとして適材適所に材料配置による軽量化があげられる。一つの部品の中で強度剛性が必要な部分を厚板にして、それ以外の部品を薄板にするという最適な重量設計が可能となる。
車体部品への適用事例としては図2にあるドアインナ—やセンターピラーリーンフォースなどがあげられる。ドアインナ—の場合、ヒンジの取り付く前方部分の板厚を厚くしている。
技術課題は隙間の制御である。継手隙間を板厚の10%程度以下に制御する必要があるため、被溶接材の継手部の直線性の確保および溶接中の熱ひずみに耐えうる隙間制御治具が必要である。直線性の確保についてはトリム型の精度、クリアランスの維持管理を、溶接中の隙間制御は高剛性な治具により対応している。また継手部の傷などにより局所的な溶接欠陥が発生するリスクがあるため品質保証技術も必要となるが、溶接中のプルーム、反射光観察や溶接後の溶接ビード観察により対応している。
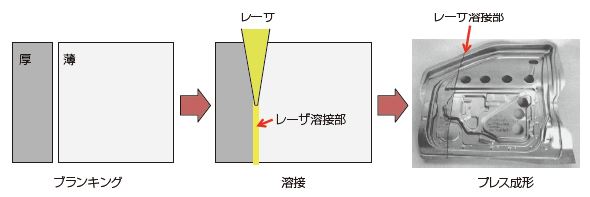
図2 テーラードブランク溶接工法
剛性向上連続溶接
車体組み立てにおける接合工法としては抵抗スポット溶接(以下、スポット溶接)が最もポピュラーである。現在でも70%以上の接合部がスポット溶接で接合されている。ただしスポット溶接は不連続接合なので部品同士の力の伝達効率が低い。これを連続で接合することにより剛性を向上させ乗り心地を向上させることができる。
レーザ溶接は連続溶接が可能な技術であり光ファイバでレーザを伝送できるkW級YAGレーザが3次元形状部品へのレーザ溶接を可能にした。
適用部位としてはドア開口部やシル部、フロアまわりがあげられる。図3にシル部への適用事例を示す。
本適用における技術課題はテーラードブランクと同様、隙間制御と品質保証である。
レーザ溶接は溶融金属量が少ないため隙間に対する溶接品質感度が高く、概ね隙間0.3mmを超えると溶接品質が著しく低下する。また車体は防錆性能を確保するためにZnめっき鋼板が多用されている。そのため隙間が50μm以下になると溶接時に蒸気化したZnによりポロシティ欠陥が発生する(図4)。
隙間制御は加工ヘッド先端のフィンガーやローラーにより加工ヘッド自身が部品を加圧することにより行っている。固定光学系を用いた加工ヘッドではこのフィンガーやローラーが隙間を制御するだけではなく焦点位置も制御することができる。
Zn蒸気対策のための微小隙間確保の方策としてはプレス加工でのエンボス成形などがあげられる。これはプレス加工時にレーザ溶接部付近に断続的に高さ0.2mm程度のエンボスを作ることで微小隙間を確保している。
品質保証についてはテーラードブランクと同様、溶接中のプルーム、反射光観察などで対応している。
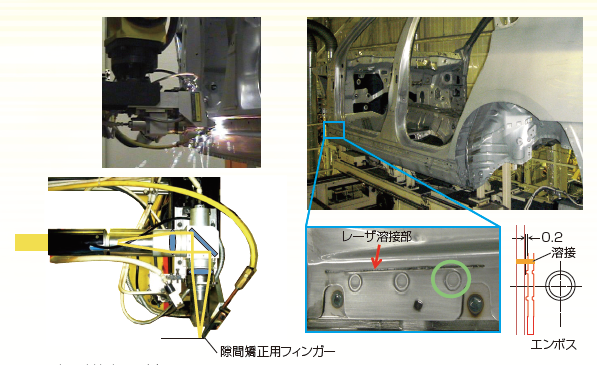
図3 連続溶接適用事例
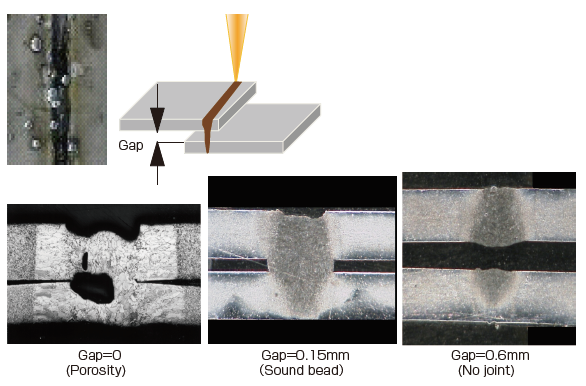
図4 Zn めっき鋼板の隙間と溶接品質との関係
(もっと読む場合は出典元PDFへ)
出典元
http://ex-press.jp/wp-content/uploads/2015/10/ILSJ15098-10-1.pdf