精密レーザ切断
医療器具に必要な手術精度が得られる技術
精密レーザ切断は医療用のチューブや部品の生産に必要となる特殊切断の理想的な技術になる。ここでは、この新しく生まれた分野の医療器具や装置を使用したときに得られる鋭い端部、輪郭および形態に対して、「手術精度」という用語を適用する。
切断や生検に使われる手術機器から特殊な切片や側壁の開口、さらにはフレキシブル内視鏡用のパズルのような連鎖にいたるまで、レーザ切断は従来の切断技術よりも高い精度、品質および加工速度を可能にしている。また、現在の市場に登場した5 軸駆動パッケージなどの新しい切断技術は、設計の自由度が増強され、より難しい幾何学形状のワンパスによる切断を可能にしている。
このような技術をうまく利用するには、システム部品と作業工程を適切に組み合わせることが鍵になる。精密レーザ切断は、動作、レーザ、ソフトウエア、段取りのすべてを統合しなければ、所望の最終製品への加工が行えない。
レーザ切断の利点
高い寸法精度での切断が必要となる小さいチューブの加工はレーザ切断が最良の選択肢になる。使用するレーザ光は物理的な存在だけではなく、材料を非接触で加工することができる。部品を曲げてしまう恐れのある押し込み、引張り、衝撃などの力が働くことはない。また、プロセス制御にマイナスの影響を与える収縮を引き起こすこともない。
レーザ切断は熱入力が最小になり、加工領域は温度を精密に制御できる。小さい部品は温度が急激に上昇し、過熱や変形を引き起こすこともあるので、温度の精密制御は非常に重要だ。
レーザ切断は約25 ミクロンの小さい直径に集光できるが、これは人の毛髪の直径に比べると、約4分の1でしかない。その結果、材料の切断は最小質量の除去で可能となり、非常に高い正確さと精度を得ることができる。
レーザ切断技術はレーザのパルス幅とパワーおよび焦点のスポットサイズを精密に制御できる。レーザ切断装置は部品と接触しないので、ビームをすべての形状に対した方向に向けることができる。また、切断形状は物理的に制約されないので、レーザ切断はどのような形状にも適用できる。表1 は技術の重要な利点を示している。
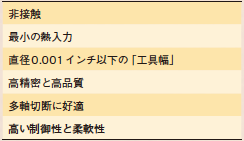
表1 レーザ切断の利点
医療器具用のレーザ切断システム
医療用のチューブや部品の切断はアシストガスファイバレーザ技術を使用することが多い。この場合のレーザは同軸配置のガス、標準的には酸素ガス(O2)の「アシスト」により加工する。O2は一般的な選択だが、チューブの厚みが0.0001 インチ以下しかなく、また、非常に高品質の切断を必要としない場合は、オイルでフィルタリングした高純度空気が使われることもある。この技術はステンレス鋼(300および400シリーズ、17‐4、17‐7)、MP35N(コバルト‐クロム合金)およびニチノールに使われる。この方法は軸上(表面に対して90°)と軸外(表面に対して傾斜)の両方の切断に適用できる。
薄い材料のごく一部を熔融する場合は強く集束したレーザを使用する。材料が熔けると、レーザと同軸の直径0.02 インチのガスジェットノズルが熔けた材料を吹き飛ばす。この熔融サイクルを継続し、熔けた材料を取り除くことで、所望の形状が得られる。レーザと材料との距離は精密に維持する必要がある。
加熱された材料は酸素と反応し、さらに加熱されるので、実際のところ、O2には二つの目的、つまり熔けた材料の吹き飛ばしと、加熱要素としての役割がある。O2の存在による発熱反応によって、切断領域の発熱エネルギーは約30 から50% の追加になる。このアシストガスは切断速度と切断品質を増強するための重要な手段になる。図1はアシストガスによるファイバレーザ切断機の基本構造を示している。図2は実際のレーザ切断機を加工中の製品と一緒に拡大して示している。
アシストガスによるレーザ切断は医療用チューブや器具のメーカーが重視する最高の切断品質と高解像の切断経路が得られる。切断品質を評価するには、つまり部品が仕様を満足しているかを判定するには寸法精度が重要になる。また、表面粗さの数値(12 マイクロインチより良好)や熱損傷のないことなども考慮しなければならない。
レーザによる切断幅は0.001 インチ以下の極端に小さい値となり、寸法精度も極端に精密な±0.0005インチほどになる。この精度はいくつかの切削工具のギザギザ歯の製作に役立つ。切断した内面に残留するドロスやバリ(付着や再固化が起こる)の発生は最小となり、まったく発生しない場合もある。その結果、後加工の必要性は大幅に減少する。改変層(加工時に噴出せずに残留した小量の材料の層)は0.0005 インチになる。
図3 は後加工不要の特徴をもつ0.01インチ厚ステンレス鋼(304SS )チューブの切断品質を例にして、レーザ切断した表面の優れた品質を示している。
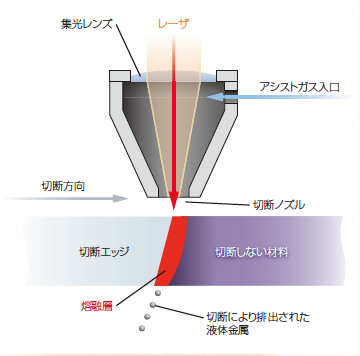
図1 アシストガスによるファイバレーザ切断機の基本構造。
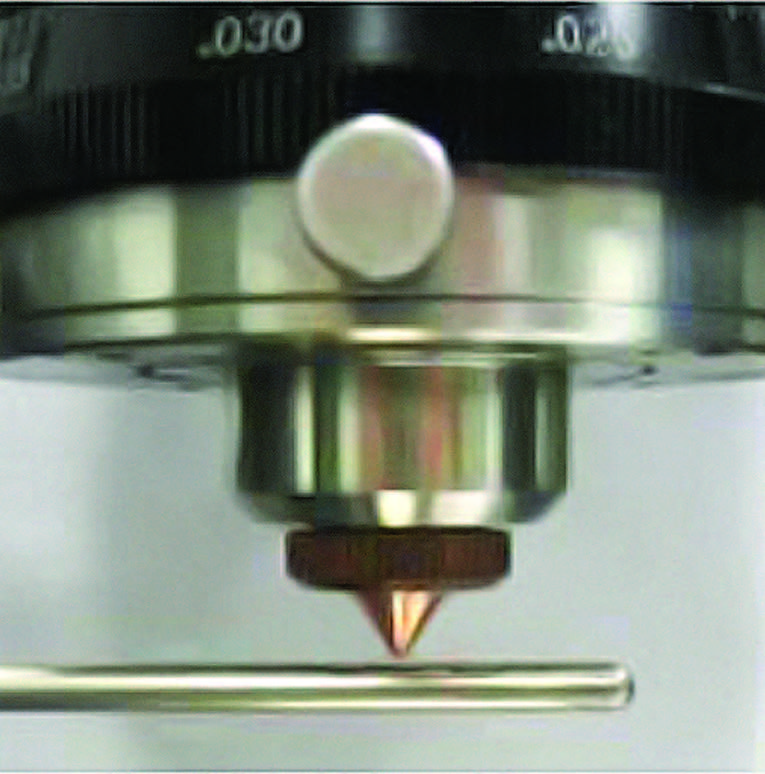
図2 拡大した実際のレーザ切断機と加工中の製品。
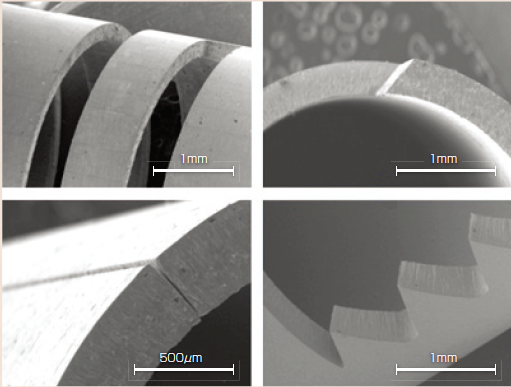
図3 典型的な0.01インチ厚のステンレス鋼( 304SS )チューブを切断したときの後処理不要の形状と端部の切断品質。
(もっと読む場合は出典元PDFへ)
出典元
http://ex-press.jp/wp-content/uploads/2011/09/035f4e620e08561ce49eab80f3e227c8.pdf