生産コストを削減する3次元コンポーネント
LDS(レーザダイレクトストラクチャリング)の技術は依然幅広い可能性を持ち続ける。MID(成形回路部品)アプリケーションが車で使用されるすべての配線ハーネスを代替することは困難だが、新しい機能を付加しながらワイヤリングハーネスの複雑さ、重さ、コストを劇的に削減することができる。10年以上にわたる開発とマーケティング活動に支えられ、MID技術は従来のコンポーネントを置き換えるだけではなく、独特な機能とレイアウトのまったく新しい世界の扉を開いていくはずだ。LPKF社のフュージョン3Dレーザストラクチャーは量産市場へのブレークスルーを可能にする新しい装置である。
これまでのレーザダイレクトストラクチャリング( LDS)は主に生産性とコスト効率の高い3D-MID(3次元配線レーザ加工機)の中小規模の生産、あるいは一回限りの製品に使用されていた。LPKF社の新フュージョン3Dレーザシステムは造形時間とコストを約3分の1 に削減して、MID の量産をぐっと身近なものとした。
エレクトロニクスやメカトロニクス製品ではサイズの小型化と多機能化に向かう傾向は年々強まっており、特に自動車用においてはドライバー支援システムで必要とされるセンサーやモジュール(ワイヤリングを含む)の要求が増えている。しかし、これらの部品やケーブルの使用は車重の増加につながり、実際にBMW 3 シリーズのワイヤーハーネスの重量は約30kg にもなる。また重量だけでなく、生産コストや取付コストも増加してしまい、その結果OEM ビジネスと潜在顧客から敬遠されてしまうことにもなる。
通信技術分野のメーカーは自社の地位を維持するために、継続的に短期で新製品を開発しそれをマーケットに投入しなくてはいけないという大きなプレッシャーがある。新製品はユニークなセールスポイントを多く持ち、他の多くの競合製品の中で際立たなくてはいけない。これは当然、前例のない機能を持つ新製品を製造できるMIDのような技術(成形相互接続デバイス)に注目が集まる。そこがLPKF 社のLDSテクノロジーであり、顧客の受ける恩恵の一つは信頼性の高い効率的で生産的な技術であり、二つ目は開発から量産までの大幅な時間の短縮である。
MIDによる機能性の向上
MID は非常に小さいスペース内に3次元プラスチック部品上で直接電子回路や電子部品を統合する。部品が見事に実装されるのでスマートフォンやノートブックにおいては狭いハウジング内にアンテナを直接取付けることができ多くのスペースが削減可能となった。このようにいくつかの機能を統合することによりコンポーネント数を少なくし、自動的に生産工程も減少する。これにより追加コストが削減でき、より高い品質の部品を作り出せることになる。
直接プラスチック部品上に電子回路を実装する方法はたくさんある。ホットスタンピングは部品上に薄くて柔軟性のあるフィルムを押し付ける様にダイを使用し、余計なフィルムはその後取り除かれる。この方法はシンプルで、広範囲な材料で利用されている。しかし問題はこの方法では高品質トラック、実際の3次元構造、および複雑な回路を作ることができない。2 つの部品の射出成形法の動作だが、最初のポリマーは回路のキャリアを製造するために使用。2番目の金属化ポリマーは導電性トラックが配置されている領域だけに適用。この方法は3 次元設計に大きな自由度をもたらすが、2 つの射出成形用金型が必要とされるためにより高価な方法になってしまう。そのほかトラックの精度にも限界があり、製品化には比較的長い時間が必要となる。そして射出成形金型の開発だけでも、2カ月程度の期間が必要とされる点が課題である。
多くの領域で利用されるレーザはMIDにおいてもその柔軟性の高さを武器に、斬新なオプションや発想をもたらす。サブストラクティブ法は必要のなくなったメタル層をレーザで取り除き、そしてそれに続きエッチング工程用のレジストを取り除く。この方法ではレーザの長時間露光と大きな金属化表面が必要とされることがむずかしい点だ。
LDS
LPKF社が特許を取得したレーザダイレクトストラクチャリング(LDS)の手法は技術的、経済的に多くの利点がある。
LDS 法ではレーザ照射により化学反応を起こす金属重合体添加物と共にドーピングされた熱可塑性ポリマーを使用する。このポリマーにレーザを照射すると金属核が形成されるが、この金属核表面は凸凹があり強固なめっき結合が実現する。次に無電解めっきによる配線化が行われ精密な配線が作られる。その後必要に応じ、銅めっき、ニッケルめっき、金めっきなどが行われる(図1)。
すべてに高い柔軟性、速度、解像度、精度といったレーザの特徴が、プロセス中で全て発揮される。もし回路を再構成しなくてはいけない場合、必要なのはレーザユニットに供給する新しい制御データだけである。これで一つの基本的なコンポーネントで異なった機能を持つ様々な部品を作成することが可能になる。つまりレーザにより描画される回路の設計を変えるだけでいいのである。
そして、これらの制御データは生産時に変更できるため、企業は非常にコスト効率の高い方法で中小規模の生産が可能になる。小ロットの製品を生産する事でさえ経済的、技術的にまったく問題はない。試作から量産への過程が短く安価で市場の需要変化に迅速に対応できるのである(図2 )。
LDS 法はすでに多岐にわたるアプリケーションで利用されている。もっともよく知られているのは高機能携帯電話、PDA、ラップトップPCなどで使用される複雑な構造のアンテナである。他にも微小サイズの医療技術製品、圧力センサー、さらにデジタルの鉄道模型レイアウト用カップリングシステムでもLDS法はその強みを見せている。
LDS 技術は、自動ボリューム認識、BMW Z4 用ステアリングホイールスイッチ、BMW K1300 バイク用ハンドルバーグリップ、シートアジャスター、スイッチングキャビネットモジュール、自動車空調調節用太陽センサーなどと一緒にピペットシステムの製造に使用されている。そして現在は、多層LDSコンポーネント製造の研究が熱心に行われている。
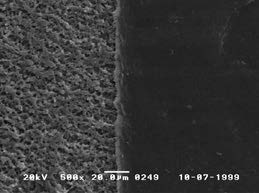
図1 レーザビームが粗
面化し後に無電解槽内で金属化され活性化する構造(左)。
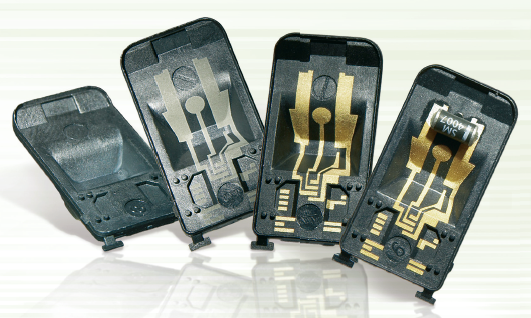
図2 シンプルな射出成形部品から3次元回路キャリアの組み立てまでの3つのステップ。
より小さく、よりスマートに
小さなスペースにより多くの機能を集約することが今、通信業界で常に望まれている。LDS 法のおかげで現在一つの携帯電話に最大12 個までアンテナを実装できるようになった。小ロットまたは中型の生産規模と比較して、大量生産をする携帯電話の製造はより高いスループットが要求されている。フュージョン3Dレーザシステムは精巧に作られた花崗岩のベースプレート上に配置された4 本のレーザヘッドが同時に7 つの位置で動作する。これにより従来システムに比較してスループットを4 倍向上させ、加工時間を最大75% 減らすことができる。さらに最高品質の部品製造において描画時に部品を回転させる必要がなくなったことで部品加工の精度が高まった(図3)。
このレーザストラクチャーは手動で供給されるコンポーネントには動作が速過ぎるため、必要なスループットレートで正確に動作させるためには2 つのロボットが必要となる。そのシステムは多くの問題もなくコンポーネントを毎年数百万製造する事ができる。また同時に単位当たりのコストを大幅に削減することができる。
フュージョン3Dシステムのレーザは65μmのビーム径を持っており、150μm幅、200μm 間隔のトラックを製造するのに適している。そのシステムは焦点を最適化する事と異なるレーザ光源を使用する事により細かな構造を生成する事ができ、他のMID製造システムの限界を超えることが可能となった。
すべての生産パラメータは、いつでも使用できる様にシステムによって保存されている。レーザストラクチャーに付属の標準ソフトウェアは、サイクルタイムを最適化するため、それぞれのレーザヘッドに制御データを分配する。ロボットフィーディングシステムと組み合わせる事で、速度と精度、及び高い水準の再現性が保証され、同時に人件費とアイドル時間を最小限におさえることができる。フュージョン3D レーザシステムは24 時間、週7日の連続稼動用として設計されている。これは大量生産能力を持つ高い柔軟性、効率性と短期間での市場投入時間を融合し、他の多くのアプリケーションにとって有益な特徴を持っている。そして基本的なコンポーネントは熱可塑性樹脂で作られているため、このレーザはレーザプラスチック溶接用としても使用する事ができる。もちろんLPKF 社はレーザプラスチック溶接専用機も持っている。
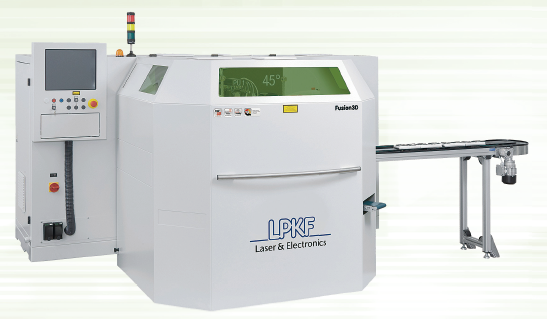
図3 MID 成型回路部品レーザ加工装置( LPKF Fusion 3D laser structuring unit )。
(もっと読む場合は出典元PDFへ)
出典元
http://ex-press.jp/wp-content/uploads/2011/09/eb195c3b220b814ac5c318acb3f36c9d.pdf