応用が拡大するレーザ焼入れ技術
高出力ダイレクト半導体レーザはCO2レーザ以上の利点がある。
レーザは30 年以上も熱処理の用途に使われているが、実用性やコストに関連する制約のために、その応用はニッチな用途に限られてきた。現在、高出力ダイレクト半導体レーザは、従来技術の欠点を克服できる解決策となり、その用途が大幅に広がると期待されている。
従来の熱処理法
熱処理法もしくは表面焼入れは、数多くの産業において、切断工具や軸受表面のような鋼鉄部品の耐摩擦性の改善や使用寿命の延長に応用されている。熱処理には部品の加熱と急冷(焼入れ)が含まれる。熱処理された鋼鉄の結晶構造には炭素が導入され、結晶格子は室温の標準状態よりも硬い状態に変換される。産業分野の表面焼入れは薄い表層だけの硬化が目標になる。母体材料は元の状態、つまり表層よりも柔軟で壊れやすく、延性の大きい状態に保たれる。表面焼入れは部品の幾何学形状の形成後に行なわれるため、理想的な加工の場合は、部品形状に物理的変形が生じることはない(編集注記: www.industrial-lasers.comの特集記事「Laser Heat Treatment Sim plified」を参照)。
一般に、各種の伝統的な(レーザではない)技術は、拡散硬化法と部分焼入れ法の二つに大別される。浸炭、窒化、炭窒化などの拡散技術は、低炭素鋼の母体を加熱し、外部から供給する炭素やその他の元素と接触させる。これらの元素は表面層内に拡散する。次に液体を使って部品の急速焼入れを行う。
一般的な部分焼入れ法では、もともと十分な炭素を含有する鋼鉄を使用し、炭素を鉄結晶格子に導入して所望の硬度を実現する。この場合、所望の領域の温度を上げるために火炎または電気誘導を用いて部品の表面を局所的に加熱し、その後に焼入れを行なう。
レーザ技術
レーザ熱処理はもう一つの部分焼入れ技術になる。そこでは空間的に成形されたレーザ光が部品の表面近傍で吸収され、急速な焼入れが起きる。この加熱は照射領域に限定され、母体材料への侵入は限られる。母体材料は熱を表面から放熱するヒートシンクとしても作用するため、自己焼入れが可能になる。
照射領域を精密に決定できるレーザビームの能力と母体材料への短い時間スケールでのエネルギー移動との組合せは、レーザ熱処理に対して大きな利点をもたらす。とくに、その利点には高速加工、表面焼入れの深さと位置の精密制御および最小の部品変形が含まれる。
レーザ焼入れは従来技術のいくつかの欠点を排除できる。例えば、炎焼入れは再現性と焼入れ特性が悪く、環境問題の制約を受ける。その結果、炎焼入れは中~大型サイズの部品に最も適している。高周波焼入れは一般的に深い熱浸透をもたらすため、能動水冷方式の焼入れが必要になり、両者はいずれも、好ましくない制御不能の変形を引き起こす。レーザ熱処理加工はビームの照射領域と機械的にアクセスできない領域だけを加熱するため、高周波焼入れに比べると、その設計と保守は著しく容易になる。このことはレーザ焼入れがさまざまな形状とサイズの部品に対して、それぞれの部品の形状に合せた誘導コイルを特注で設計しなくても、容易に適用できることを意味している。
このような利点をもつにもかかわらず、何故レーザは熱処理の市場により深く浸透しなかったのだろうか?レーザ焼入れのほとんどはCO2 レーザを用いて行われてきた。CO2 レーザは切断、溶接、穴あけなどの著しい高強度と極端な局在エネルギーを必要とする用途の場合は応用範囲の広い優れた手段だが、熱処理の要件を十分に満たすことができない場合が多い。その一つは10.6μmの出力波長が問題になる。実質的に鋼鉄などの金属は、10.6μmの光を十分に吸収しないため、 CO 2 レーザで熱処理する表面は吸収性被覆による事前「塗装」が必要になる。また、赤外線のCO2 レーザ出力は光ファイバによる伝送が難しく、加工場所への接近も限定される。
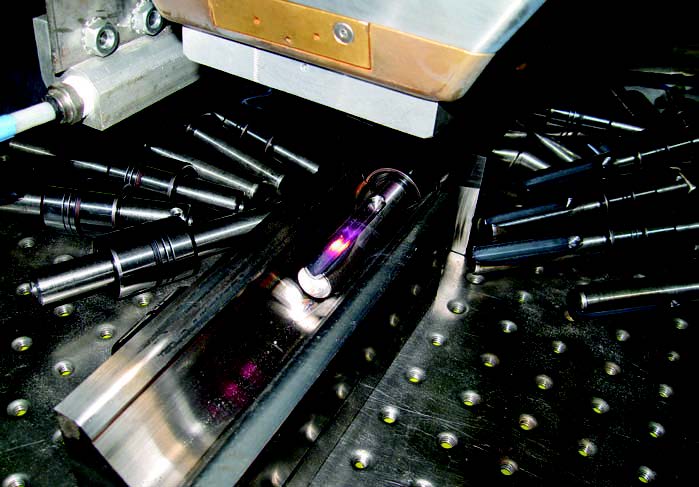
図1 シャフトのキー溝の表面焼入れ。
(もっと読む場合は出典元PDFへ)
出典元
http://ex-press.jp/wp-content/uploads/2011/04/069682394fc66bc089accf06a187e0dc.pdf