レーザー加工に用いられるレーザーは、年々高出力化が進んでいる。現在でこそ、炭酸ガスレーザーやファイバーレーザーがシングルモードで数kWの出力を達成しているが、1980年以前は数100Wの炭酸ガスレーザーが主流であった。レーザー溶接においてはYAGレーザーが用いられているが、YAGレーザーはTIGやMIGなどのアーク熱源とレーザーを合わせた加工(ハイブリッド加工)も行われている。
レーザー加工技術の進歩は、レーザー出力の増加とレーザーの短波長化・短パルス化とともに進化している。最も高出力なレーザーは炭酸ガスレーザーやファイバーレーザーであり、数10kWの出力のものが市販されている。
レーザーによる微細加工
ここ十数年で、レーザーの安定化と高出力化が達成されたため、短波長・短パルスレーザーによるミクロンオーダーのスケールを下回る微細加工が可能になった。
短波長レーザーによる加工
1990年代に高出力化が進んだエキシマレーザーや、高調波発生技術と高繰返し技術の産物による短波長固体レーザーにより、レーザーによるプリント基板の穴あけ加工や微細穴加工が可能になった。
短波長の固体レーザーとして、当初はランプ励起のNd:YAGレーザーが用いられていた。しかし、ランプに繰返しの制限があり、また出力もLDと比べて低いことから、今では多くがLD励起のレーザーに置き換わっている。
短パルスレーザーによる加工
1990年代後半に産業用のフェムト秒レーザーの出現により、微細加工が可能になってきた。780〜800nmで発振するTi:Sapphireレーザーがレーザーによる微細加工用途に用いられてきたが、近年では超短パルスErファイバーレーザーの2倍波やYbファイバーレーザーが用いられるようになってきている。
下表は、代表的なレーザー発振器の特長をまとめたものである(平成22年度 特許出願技術動向調査報告書(概要)レーザー加工技術,特許庁,平成23年4月より引用)。
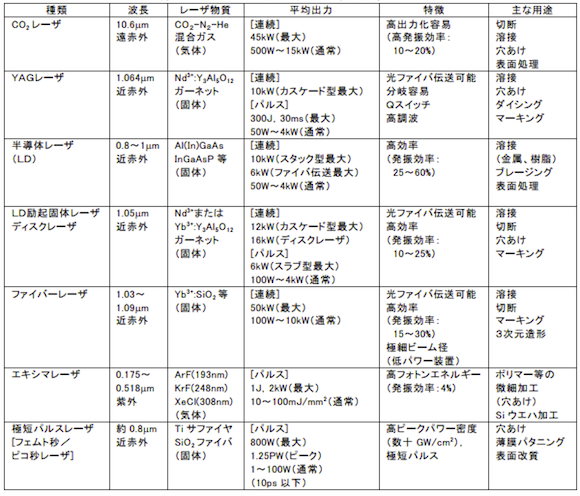
表1.レーザー発振器の特徴