3Dプリントによるひずみゲージセンサ製造の改善
デジタルプリントとレーザ処理で、手作業の処理工程からなる従来の接着方法を置き換える。
変形量を測定するための検出素子として80年以上にわたって使用されてきたひずみゲージは、今や当たり前の存在となっている。しかし、測定値とそのデジタル処理を、自動化可能なプロセスによってはるかに高いレベルで再現可能とすることを求める声が、業界でますます高まるにつれて、従来の接着剤とセンサで構成されるひずみゲージは、新しい課題に直面している。そうした要求に応えて、新しい用途を開拓するために、積層造形技術を適用して、より柔軟な設計、自動化、再現性を、ひずみゲージの接着にもたらすことができる。積層造形によるひずみゲージのメリットが理解できるように、まずは従来の問題について簡単に振り返りたいと思う。
従来のひずみゲージとその取り付け方法
ひずみゲージは、部品表面の形状の変化(ひずみ/圧縮)に伴う力やモーメントなどの部品負荷を記録するために使用することができる(図 1)。この目的に対し、測定の不確かさを低減するために、ひずみゲージはこの数十年間、絶えず改良されてきた。しかし、ひずみゲージの基本的な動作原理は変わっていない。導電体は力を加えると変形する。導電体の長さと断面の両方が変化するため、測定可能なそのオーム抵抗が直接変化する。
ひずみゲージと聞いてまず思い浮かぶのが、それを取り付けるために必要な骨の折れる作業である。接着作業は、多くの処理工程からなり、ノウハウが必要というだけでなく、キャリア箔が付いた状態で供給されるひずみゲージを、部品に貼り付けて正確な測定値を提示する測定点として設定するまでの作業の手の感触と経験が求められる。原則として、異物を混入させることなく薄い接着層を貼り付けるために、作業環境を清潔に保つ必要がある。家庭用製品に使われるような小さな力トランスデューサの場合は、ホットメルト接着方法が適用される。接着剤がコーティングされたひずみゲージを、圧力をかけて測定点に押し付け、部品を加熱装置で硬化させるという方法である。
サイズ、重量、温度感度が原因で、部品を加熱装置に入れることができない場合は、低温接着方法が適用される。接着領域にサンドペーパーをかけて油分を除去した後、ひずみゲージを貼り付ける位置に印を入れる。ひずみゲージ位置のマーキングと、その後の接着剤を均等に塗布する処理は、一般的に手作業で行われるため、ひずみゲージの水平方向の位置決めには大きな不確かさが生じる。接着剤が硬化する間に、約1分間圧力をかけてひずみゲージを接着させる。硬化した接着膜の厚みにはかなりのばらつきが生じる可能性があり、それはセンサの応答性に大きな影響を与える。
つまり、ひずみゲージの接着には2つの問題がある。1つめは、手作業の工程によって人的ミスが生じるために、一貫した品質が得られないことである。この作業を補助するための手段が多数提供されており、それによって高い品質要件を満たすことができるが、労力と設定時間は増大する。測定点の品質が不十分である場合は、ひずみゲージを剥がし、剥がしたものはもう使用できないので、新しいものを貼り付けなければならない。2つめは、適格な人材を用意することが、ひずみゲージの取り付けにかかるコストの最も大きな割合を占めることである。数量が増えてもスケールメリットはほとんどなく、ほぼ数量に比例してコストは増大する。従って、自動プロセスによるひずみゲージの接着が必要である。
これに加えて、その後の測定とデータ送信に必要な作業があり、特に回転部品の場合は、ますます処理が複雑になる。ここでの一般的な方法は、測定データとエネルギーの両方を誘導結合によって送信する、誘導性のテレメトリシステムを使用することである。しかし、そのようなシステムは、非常に高額で特に堅牢ではないため、連続生産に適切に適用できるケースは限られる。表面弾性波(Surface Acoustic Wa ve:SAW)や磁気ひずみセンサ技術といったその他の手段は、一部の材料にしか適さず、現場で使用すると干渉の影響を受けやすいことが判明している。そのため、これらの手段はまだ確立された状態にはない。無線データ通信のための低消費電力の産業用ソリューションの開発が進んでおり、これは新しい可能性を切り拓いている。本稿後半では、これを利用した、外部のエネルギー源を必要としないセンサ技術の実用化について説明する。
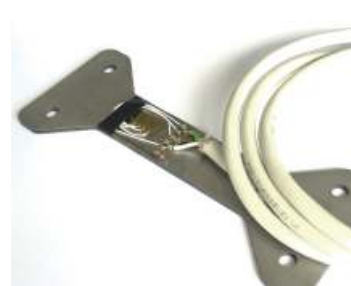
図1 従来の方法でステンレス鋼製の部品に貼り付けられた接続線付きのひずみゲージ(画像はすべてフラウンホーファー ILT提供)。
ひずみゲージセンサのための付加的な材料プリント
上述の問題に対し、積層造形がどのように利用できるのだろうか。既に多くの3D部品が、さまざまな材料からプリント可能となっている。独フラウンホーファーレーザー技術研究所(Fraunhofer Institute for Laser Technology:Fraunhofer ILT)と独i4Mテクノロジーズ社(i4M Technologies)はこの疑問に応えて、プロトタイプを開発した。以下では、このプロトタイプについて説明する。
従来のひずみゲージは一般的に、抵抗性の測定グリッドがキャリアとカバーフィルムの間に挟まれた構造となっている。この箔ひずみゲージが、接着剤によって部品に貼り付けられる。部品のひずみは、2つの中間層を介して測定グリッドに伝送される(図 2左)。原則として、力の伝送損失を防ぐために、測定グリッドは部品表面のできるだけ近くに配置する必要がある。接着層の厚みのばらつきは、力の伝送に影響を与え、ひずみゲージの測定点の応答性を変化させる可能性がある。プリント処理(インクジェット印刷など)によってひずみゲージを直接取り付ければ、部品と測定グリッドの間の層構造を簡素化することができる(図2右)。必要な中間層は、部品と測定グリッドの間の力伝送と電気絶縁の機能を統合した1つの層だけとなる。
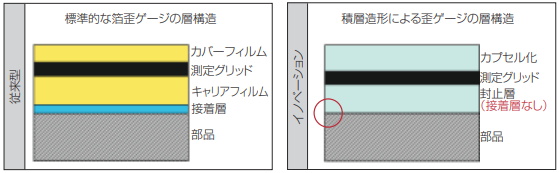
図2 従来のひずみゲージ(左)と積層造形によるひずみゲージ(右)の層構造の比較。
(もっと読む場合は出典元へ)
出典元
http://ex-press.jp/wp-content/uploads/2021/09/032-035_ils_3d_printing-1.pdf