全反射トップハット型ビームシェーパーによる自動繊維配置の改善
ロボット・オートメーションを利用した複合材のレーザ製造。
近年、環境に対する配慮と燃料消費削減のニーズに促されて、航空業界ではますます多くの複合材アセンブリが、航空機に使われるようになっている。複合材には、金属材と同等の機械的強度を保ちながら軽量化できるというメリットがある。
Airbus A350は、その典型的かつ先駆的な例で、主要構造の半分以上に複合材が使われている。その結果、大型で複雑な形状の複合部品を、効率的かつ反復可能な形で製造するプロセスに対するニーズが出現している。規模はそれよりも小さいが、このニーズは、風力タービンのブレードの製造など、他の業界においても現れている。
このニーズを満たすプロセスの1つが、自動繊維配置(Automated Fiber Placement:AFP)である。これを踏まえて仏カイラブズ社(Cailabs)は、仏コリオリ・コンポジッツ社(Coriolis Com posites)の仕様表に基づいて、超小型レーザ繊維配置ヘッドを開発した。このヘッドは、AFP装置に組み込まれている。これによって複雑な形状の複合部品を、良好な品質を保証しつつ製造することができる。
AFPとは
AFPとは、繊維テープを金型の上に連続的に配置して複合部品を製造する、積層造形(付加製造)の一種である(図 1)。テープは、スプールからロボットアームを通して、型穴または既に積層された構造の上に供給され、積層間を確実に接合するための十分な圧力が印加される。通常は処理中に、テープとその延長として基材を加熱することが必要である。中には、複数のテープを同時に配置でき、テープをさまざまな位置で個別に切断できる装置も存在する。
金型にも、オス型とメス型という種類がある。このプロセスは、熱硬化性または熱可塑性樹脂を繊維に浸み込ませたプリプレグや、ドライファイバなど、さまざまな種類の材料に対応する。また、より従来型の手法とは異なり、オートクレーブを必要としない。プリプレグは、金型の上で直接硬化し、ドライファイバは、低圧トランスファ成形によって樹脂とともに注入または射出することができる( 1)、( 2)。
この手法には、従来型の方法に勝るメリットがある。曲率半径が小さいため、ロボットアームは、装置の造形体積内の複雑な形状の金型の上に、テープを配置することができる。このプロセスを自動化すれば、反復が可能となり、例えば、堆積構造の長さを最適化することにより、材料ロスを削減することもできる。
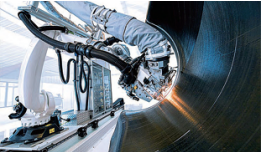
図1 曲面部品を製造するためのAFP装置。
レーザ:複合材の加熱に適した手段
重合温度が200℃の熱硬化性樹脂を使用する場合は、赤外線ランプを使用して複合材テープを加熱することができる。しかし、さらに高い加工温度(300〜400℃)を必要とする熱可塑性樹脂に対しては、赤外線ランプでは出力が足りない。熱可塑性樹脂の使用は増加している。ガラス転移温度が高い代わりに、リサイクル可能で、加工中のやり直しが可能といったメリットがあるためだ。従ってレーザが、テープの加熱に適切な手段ということになる。レーザは高い出力を、限られた表面に指向的に照射することができる。これによって、必要なすべての出力密度が加工対象の熱可塑性樹脂に、適切な加工速度で供給される。
繊維を加熱するレーザビームを成形(シェーピング)することにより、ビームを加熱領域の形状に適応させて、積層間の接合品質を高めることができる。実際、接合品質に対するレーザ出力の卓越した効果(79%)は、マジュムダール(Mazumdar)とホア(Hoa)によって示されている(3)。
(もっと読む場合は出典元へ)
出典元
http://ex-press.jp/wp-content/uploads/2022/05/042-043_ilsft_robotics.pdf