熱加工にメリットを持つ、高出力ダイレクトダイオードレーザ
高出力ダイレクトダイオードレーザは、コンパクトなサイズと高い効率に加えて、最適な波長とビーム特性を備える
近年、ファイバレーザと高出力ダイレクトダイオードレーザ(Direct DiodeLaser:DDL、直接集光型半導体レーザ)の熱加工への適用がますます増加している。どちらの種類のレーザも優れた特性を備え、材料加工において従来のレーザの代わりに使用することができる。エンシュウは、応用技術、加工技術、周辺機器向けの包括的なシステムにおいて、これらのレーザを提供している。
加工用レーザ
表1に示すように、高出力DDL が、炭酸ガス(CO2)レーザやイットリウムアルミニウムガーネット(YAG)レーザといった従来の種類のものと比べて、省エネ効果に優れていることは明白である。エンシュウは、日本製の高出力DDLに基づく、最大5kW出力のレーザ発振装置を提供している。
エンシュウは当初から、主に金属やプラスチックの溶接を対象に、DDL技術を採用するレーザ加工機を提供してきた。また、ファイバレーザの提供を開始したことで、キーホールタイプの溶接による、高精度な重ね合わせ接合にも対応することができる。表2に、エンシュウのレーザ加工機のラインナップを示す。
エンシュウは2002年の創業以来、浜松ホトニクスと協業している。その背景の下で、高出力ダイレクトダイオードレーザを中心としたレーザ加工機の開発と製造を行っている。当社は、ファイバレーザと日本製高出力DDLのメリットの実用的な活用方法を各顧客に提案することにより、日本製DDLの市場シェア拡大に取り組んでいる。当社は現在、それらのレーザを搭載して開発したさまざまな加工システムを主に推進している。
エンシュウは現在、周辺機器を備えるDDLを提供している。図1に示すように、DDLは非常に小さい。当社は、電源やチラーの設計と製造も手掛けており、完全なレーザ装置を顧客に提供することができる。このDDLはコンパクトで、4kWの出力で重量はわずか15kgしかなく、従来のロボットや機械に簡単に搭載することができる。直接照射型であるため、光学系に損失はほとんどない。
また、ファイバケーブルは使用されていない。ヘッド周りの配線は、電力線、信号線、冷却水ラインで、モーション駆動装置用の配線や配管は簡素化されている。DDLは、トップハット型のプロファイルを持つ矩形のビームスポットにより、熱伝導溶接が可能で、隙間の許容範囲が広く、溶接スパッタが少ない(図2)。
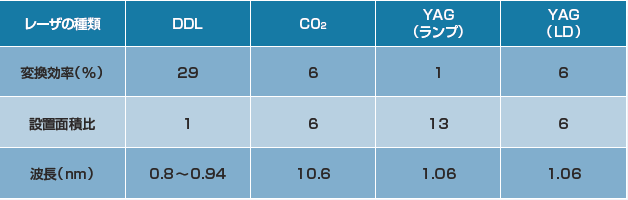
表1 レーザ比較表
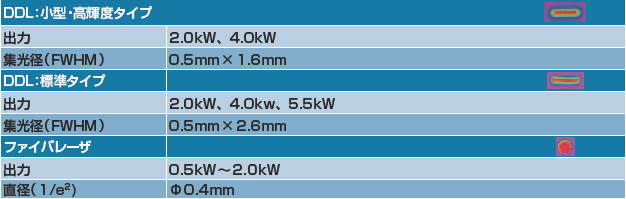
表2 ラインナップと標準特性
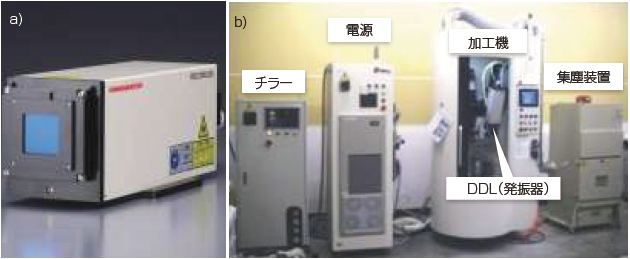
図1
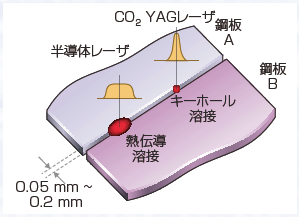
図2 DDLと従来型レーザのレーザビーム特性の比較。
溶接事例
自動車排気系の溶接:自動車排気系部品は、板金の重ね溶接によって生成される。重ね溶接には一般的に貫通結合が用いられるが、排気系の場合は、溶接部品をしっかりと結合することが必要である。また、下の鋼板の下側部分にスパッタなどの異物が混入するのを防ぐ必要がある。そこで、ビード幅が広く、伝導溶接が可能なDDLを採用した。図3には、広い溶接幅が得られ、下面部分に非貫通溶接が生成されていることが示されている。
産業用リチウムイオン電池の溶接:この電池部品(図4)の加工も、DDLを適用することにメリットがある事例である。円筒形の板金部品の上にディスクを配置して突合せ溶接が行われるが、板金部品であるため、接合部には隙間と位置ずれが生じる。高出力DDLを使用すれば、隙間の許容範囲が広く、照射位置を変えることができるため、この問題が解決される。部品上にスパッタが残る心配も軽減される。DDLはビーム幅が広いため、スパッタの少ない熱伝導型溶接が可能で、非貫通溶接において十分な溶接領域を生成することができる。
アルミニウム箔のスポット溶接:この例(図5)では、DDLの大きな矩形スポットによる溶接が活用されている。この加工では、アルミニウム箔でラミネートされた部分(10~20枚)とフラットプレートの上面に矩形ビームを照射することにより、それらを接合する。キーホール溶接にファイバレーザとガルボミラーを組み合わせると、溶融部分に突起が生成され、溶融金属が飛び散り、接合部に不具合が生じる。一方、熱伝導型溶接を用いれば、安定した溶融池が形成されるため、突起は生成されにくく、部品は適切に接合される。
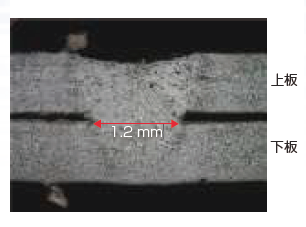
図3 非貫通の重ね溶接。
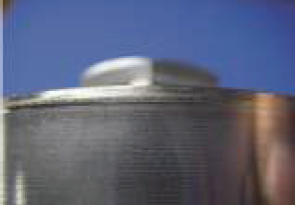
図4 円筒突合せ溶接。
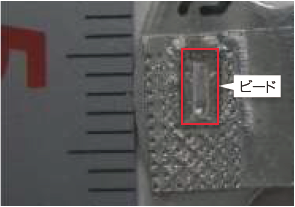
図5 アルミニウム箔の重ねスポット溶接。
(もっと読む場合は出典元PDFへ)
出典元
http://ex-press.jp/wp-content/uploads/2020/07/028_ar_high-power.pdf