高出力青色レーザで、製造スループットが向上
溶接に定性的および定量的メリットをもたらす青色レーザ
新しい種類の高出力青色レーザは、製造部門に可視光の能力をもたらす。これらのレーザを使用すれば、レーザによる加工と製造の速度と精度を、さらに幅広い材料に適用することができる。数百Wの出力を備えるこれらのレーザは、これまで利用できなかった定性的および定量的なメリットを提供する。
多くの用途に対し、レーザ溶接は従来の溶接手法よりもスループットと接合効率が高い。一般的に提供されている高出力産業用レーザは、赤外(IR:infrared)波長で動作する。多くの用途でそのことに問題はないが、一部の金属は表面に入射した赤外光の90%以上を反射するため、制約が生じる。特に、赤外レーザ溶接は、銅や金などの黄色の金属に対して問題がある。
赤外波長での吸収率が低いということは、溶接プロセスを開始するために大量の光学粉末が必要になることを意味する。溶接プロセスには、材料を単純に溶融してリフローする伝導モード溶接と、レーザによって金属を蒸発させて、蒸気圧でキャビティまたはキーホールを形成するキーホール溶接の2種類がある。
キーホールモード溶接は、レーザビームの吸収率が高くなる。ビームが材料を伝播する間に、金属や金属蒸気に複数回作用するためである。しかし、IRモードでキーホール形成を開始しようとすると、溶接する材料の反射率が高い場合は特に、かなりの入射レーザ強度が必要になる。キーホールが一旦形成されると、吸収率は急激に増加するので、レーザ出力や溶接速度を慎重に制御して、溶接パドルから過剰なスパッタが発生するのを防ぐ必要がある。
高いIRレーザ出力は、溶融プールに高圧の金属蒸気を生成し、それがスパッタやボイド(空洞)の要因となる可能性がある。溶融プールが凝固するときに、金属蒸気とプロセスガスからの「気泡」がトラップされることにより、接合部に空洞ができる。このポロシティは溶接の強度を低下させ、抵抗を増加させるので、接合部の品質は低くなる。溶融パドルから飛散する溶滴であるスパッタは、高圧の金属蒸気によって、溶融パドルが沸騰し材料が飛び散ることによって、発生する。
高出力可視光波長レーザを使用すれば、溶接パドルを安定させてスパッタを抑えることができる。黄色の金属に対する可視光波長の吸収率は、赤外波長よりも約1ケタ高い。吸収率が高ければ、材料に供給されたレーザエネルギーの大部分が材料に吸収されるので、レーザ溶接を制御することができる。現在のところ、問題は、産業用途向けの適切な高出力可視光波長レーザの開発が難しいことである。高出力レーザはほとんど提供されておらず、存在するのは高額なプロトタイプに限られている。新しい種類の青色レーザは、この問題を解決する。
青色域へ
高出力青色レーザには定性的にも定量的にも、従来のIRレーザによる溶接プロセスに勝るメリットがある。青色波長の吸収率が高いことがその主な理由である。定量的なメリットは、溶接速度が高く、プロセスウィンドウが広いことで、それはそのまま、生産時間の短縮につながる。このレーザ溶接プロセスのような生産工程をできる限り堅牢にして、生産のダウンタイムを最小限に抑えることに、メーカーは常に努めている。 青色レーザは、メーカーが求めるプロセスウィンドウの拡大を実現する。それにより、溶接部品の許容誤差が緩和される。一方、定性的なメリットは、溶接部にスパッタや空洞が生じないことで、それによって、機械的強度が高まり、電気抵抗が低下する。一貫した溶接品質は、製造歩留まりの向上にもつながる(図1)。青色レーザは、IR レーザでは実行できない伝導モード溶接も行うことができる(図2)。米ヌブル社(NUBURU)の青色レーザ「AO-150」は、200μmの光ファイバを通して450nmの光を150Wで出力する。その内部では、窒化ガリウム(GaN)半導体レーザで構成されたアセンブリからのビームに革新的な光学部品を組み合わせることにより(表紙を参照)、単一の出力ビームが生成されている。
上述の理論上のメリットは、測定可能な著しい性能改善という形で実証されている。ヌブル社は現在、最大で1.4MW/cm2 を達成し、500μmの銅を毎秒20mmを超える速度で完全溶け込み溶接することのできる、500W、450nm のレーザをテストしている。IRレーザ溶接と比べて、この青色レーザによるキーホールは、はるかに安定しており、高品質でスパッタのない溶接が得られる。また、この青色レーザはキーホール溶接に限定されず、非常になめらかで空洞やスパッタのない伝導溶接も可能で、その点においてもIRレーザに勝る。
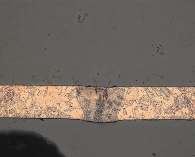
図1 キーホールモードで溶接した254μmの銅板の断面図。
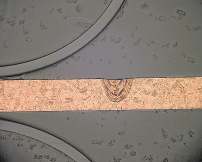
図2 伝導モードで溶接した500μmの銅板の断面図。
前途に広がる青空
青色レーザは、何の役に立つのかまだわからない解決策ではなく、差し迫った問題に対する解決策である。たとえば、化石燃料にともなう環境問題に対する意識の高まりから、燃料に対するより柔軟な解決策を求める声は高まっている。電気自動車への移行は、全般的な環境影響を低減するための新しいアプローチの1つの側面かもしれない。しかし、電気自動車にはバッテリーが必要で、しかも、できるだけエネルギー密度の高いバッテリーが多数必要である。リチウムイオンバッテリーのエネルギー密度は、電極の表面作用に依存し、表面積が広いほど、エネルギー密度は高くなる。
リチウムイオンバッテリーの負極は、被覆された銅箔によって作製される。性能を最大限に高めるために、複数の薄箔層によって負極を構成することにより、銅の表面積を広くすることが行われる。銅箔を、1 層ずつ互いにきれいに溶接した後、各バッテリーセルのエッジに溶接することにより、機械的強度が高く、抵抗の低い接合部が生成される。続いて各セルのエッジを結合することにより、内部タブとバスバーから外部バスバーへの一連の統合が行われる。つまり、かなりの接合処理が必要で、プロセスウィンドウが狭く、効率が低いと、コストが高くなり、エネルギー密度は低くなってしまう。
(もっと読む場合は出典元PDFへ)
出典元
http://ex-press.jp/wp-content/uploads/2018/09/p6_tr_high-power-blue-laser.pdf